How to make a waterproofing foundation?
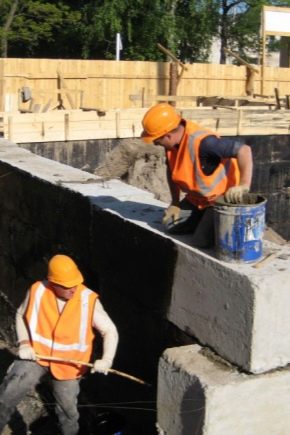
Everyone knows that the foundation, its stability and stability determine the life of the structure, its permissible parameters and the safety of residents and their property. But even the most durable materials and structures can quickly lose their qualities if they are not protected from groundwater and precipitation. Solving this problem correctly is the responsibility of every developer.
Special features
Foundation waterproofing is fundamentally different from works on walls or roofs that are similar in their manifestations — they only need to prevent the action of liquid water and the ingress (or delay) of water vapor inside.The foundation can collapse even if it is covered with a layer of ice, but not soaked with liquid. In addition, water found in the ground can never be considered clean.
It is inevitably clogged:
- oil products;
- car exhaust;
- emissions from industrial enterprises and boiler houses;
- agricultural fertilizers;
- chemicals and many other substances.
If the protection of the cap is not able to withstand such powerful destructive agents, then its value decreases sharply.
In addition, it is necessary to fear the air dissolved in water (more precisely, oxygen). Rarely what substance can be compared with him by chemical activity. And finally, we must not forget about the mechanical impact of the flowing water - the top layer of underground fluids comes with rain and snow, falls into the soil during spills.
Foundation protection should always consider:
- how powerful and stable the upper horizon;
- how effective is the prevention of its occurrence (storm sewers and drainage);
- what are the capillary properties of the soil, the type of its rock and fraction;
- how deep is the freezing point.
The addition of a waterproofing layer laid around the house drainage is necessary if the upper soil horizon is very powerful and sustainably maintained throughout the year.
The next factor is groundwater. The depth of their location is determined by the ratio of impermeable layers
The amount of groundwater is in direct proportion to seasonal changes. The wells help to control all these moments, but you need to take into account the distance to them and the fact that in a particular place the situation may be different.
Waterproofing is represented by such types of work as:
- enhancing the hydrophobic properties of structural materials;
- the formation of impermeable to water coatings on the walls of the foundations;
- isolation of horizontal seams from the liquid, preventing water from going upwards through the capillaries;
- cover the main structures and waterproofing layer from mechanical destructive effects.
Even if the foundation is made of a monolithic slab, it is recommended to warm it and the basement in order to reduce the harmful effects of cold.
An additional element of prevention can be considered the formation of ventilation structures.From tamped cushions of sand and gravel, on which the foundations of houses usually rest, are separated by a cut-off horizontal waterproofing. This design is always overlapped with insulation prepared in the basement floor. The outer vertical wall is supplied with a coating covering, covered by a special membrane and geotextile.
To protect the upper edge of the basement, it is covered with a roll-up waterproofing, after which it is possible to erect walls and floors. Drainage is provided by pipes laid around the perimeter that are surrounded by gravel. Elevated protection from the penetration of precipitation helps clay locks around the entire house. In areas with a particularly harsh climate, where the ground freezes deeply, and for the construction of a residential or warehouse basement, the foundation will also have to be warmed.
Regulatory requirements
The standardized approach to waterproofing the foundation and basement of the JV and SNiP define quite clearly. According to these documents, it is impossible not to conduct waterproofing, if the effect of groundwater and wastewater, any other liquids on the base of the house has medium or high intensity.
But even when at the time of the survey there is no such threat, this does not mean that these works can be neglected.
It is strictly necessary to conduct waterproofing foundations, if:
- the soil tends to swell, is filler or swells;
- there is a shift in chemical balance towards acids or alkalis;
- In the ground there is a significant amount of organic compounds.
Engineers and builders can learn from the same SNiP how to apply different materials, what their characteristics should be, where they should be stored, how to organize production, and much more. Concrete waterproofing is allowed only when its moisture content is not more than 4%. The minimum number of layers of waterproofing paint is two, and twice as much is recommended. Each layer should be strictly from 3 to 6 mm.
Contiguous strips make always overlapping - this is mandatory for both pile and slab foundations.
The types of materials used for waterproofing, means of protection from capillary inflow of groundwater are normalized in SNiP. The latest editions regulate the use of polymer remedies.You can not work at low temperatures and in hot weather.
Waterproofing according to Russian standards is not allowed when exposed to significant levels of ultraviolet radiation, as well as in strong winds.
The chemical composition of injection waterproofing and the procedure for its use are regulated.
Kinds
Horizontal
The device of horizontal waterproofing is designed to block the capillary pull of water from the soil. Even a well-insulated foundation can be wetted through the base. The problem is compounded when isolation is at least a little broken. Porous materials draw water in no worse than lumps of sugar; it even goes to the lower floors of the house itself.
There are three main methods of horizontal covering of foundations:
- roll (only after preparing the base);
- impregnating;
- injections.
The first option is practiced only before the construction of the walls, while the other two can be applied later, when repairs will be carried out. The prerequisite is the formation of leveling screeds, which are made from cement-sand mortars.Be sure these solutions are complemented by components that increase the hydrophobic properties of concrete. If bitumen or polymer based rolls are used, then only materials with increased strength are selected.
Failure to comply with at least one of these requirements can create serious problems in the future.
Horizontal waterproofing is divided, albeit arbitrarily, into three levels: the first is created under the foundation, the other is mounted on the base, and the third is related to the protection of floors.
Despite the difference, the technological principles are the same.
If in the special literature or in the accompanying materials it is indicated that some solution can be applied in the normal humidity regime, then this indicates the permissible humidity of the walls up to 75%. Only those rooms for which this level is 15% less fall into the dry group.
Vertical
For all the importance of horizontal waterproofing, the main role still belongs to the protection of vertical planes. Primary vertical processing is carried out in the process of construction itself, when the quality of concrete is improved with special additives. If the primary protection is not implemented, executed, but poorly or was violated, then re-processing is carried out.The methods of vertical insulation are generally the same as when working in a horizontal plane.
It is important to know that the level of protection of the foundation and even its individual parts from water is not always the same.
For example, the first class of protection completely allows the formation of wet spots on the inside and even minor leaks. For obvious reasons, this level is suitable only for objects where there is no electrical outlet. In housing construction, such foundations are not used - they apply protection not lower than the second level, without moisture stains. It is considered sufficient for technical premises.
Materials
Rolled waterproofing using modern materials based on bitumen and polymers allows you to guarantee at the same time:
- excellent reliability;
- affordable price for the consumer;
- the ability to do all the work yourself.
The bitumen-based coating system is little susceptible to cracking and will be able to withstand various types of groundwater. Temperature effects are not too scary for him either. In addition to improving the reliability of the insulation helps its combination with a coating on a polymer-bitumen base.
Despite the variety of brands, the vast majority of professional installers prefer rolls "TechnoNikol."
- CCI1 get, adding to the basis of fiberglass bitumen with special additives by fusing. Outside such a product is covered with a film of polymers. Despite the decent characteristics when buying, the overall service life is about 7 years, which seriously limits the demand for such protection.
- The budget category also falls "Linokrom EPP"which serves up to 10 years. Polyester fibers are chosen as the basis for it; installation is also carried out by fusing. The developers promise excellent adhesion to concrete and metal.
- "Bikroelast TPP" can be made on the basis of polyester, and fiberglass, the minimum time of use of 15 years. Mounted such a coating by welding. It is important to know that before surfacing the surface of the foundation will have to be thoroughly prepared. The main difference between the roll materials is the thickness of the formed layer. For bases that lie shallowly (up to three meters), even 2 mm of insulation is enough, if only everything is sealed reliably and protection against layer destruction during ground movements is provided.
It is necessary to take into account that the use of materials of an economical class results in the need to make insulation in two layers.
At the same time, the seams of sheets are shifted relative to each other in order to impede the formation of through security breaches. Deep foundations (3-5 m) should be covered with waterproofing of at least 4-8 mm - the exact parameters are determined by the characteristics of the soil. And if the sole goes deeper than 5 m, you will have to make the protection thicker than 0.8 cm. But it is extremely unlikely that this will be required in private housing construction.
Obmazochnaya waterproofing can be practiced both in close bundle with the roll coating, and separately from it. The thickness of the layer applied in this way can be 1 mm and 3-5 cm - it depends on how great the danger is. Technological methods for coating the foundations from inside and outside have been developed. Internal insulation is designed to block the concentration of capillary water. If it is made qualitatively, then even the spring flood or prolonged rains will not affect the microclimate in the basement.
There are two main types of coating: bitumen and cement.
What unites them is that the coating covers the entire surface at once.A serious advantage is the absence of the need to attract highly qualified specialists, as well as the lack of payment of big money for the material itself.
The most commonly used coatings are based on bitumen, the choice of a specific version is determined by:
- temperature when working;
- required area;
- the urgency of applying waterproofing;
- homeowners ’financial opportunities;
- processing inside or outside;
- assumed loads.
Hot bituminous treatment began to be used earlier than any other options.
Over it, however, technologists and chemists thoroughly worked. As a result, this coating has become much more perfect than its counterparts in the past: increased elasticity, easier penetration into the thickness of the concrete slab. But there are undeniable shortcomings that are associated with the fundamental features of the technological process. For example, it is impossible to do without heating devices on a building site.
It is necessary to strictly observe safety precautions to prevent fire or burn.
However, hot bitumen can be used even in the cold season.The best options are considered to be a mixture, including any organic solvent. You can apply them with a brush and spatula, not knowing any professional techniques.
If polymers are included in the composition of bitumen mastic, then it turns out to be more elastic, better adheres to the substrate and differs in an extended temperature range. The only drawback is the multiplied cost of polymer mastic. Mixtures containing any solvent should not be used indoors in the basement. Water based coatings are preferred there - they are completely safe for health. But with this method of processing, you need to choose the time when the air warms up to 5 degrees Celsius and above.
For waterproofing foundations quite widely used liquid rubber.
The similar method began to be applied rather recently and is preferable on continuous and hard-to-reach sites. It is very difficult to apply roll protection on them, and with a rubber coating such problems do not arise.
Immediately it should be clarified that chemically this mixture is not a "real" rubber, but a combination of bitumen with polymers.Application of the composition on different surfaces is not difficult, it does not matter whether they are located horizontally, vertically or tilted.
Liquid rubber can be:
- sprayed;
- bulk;
- painting.
The first option is rarely used: mainly in large-scale construction and with significant amounts of work. Independently use a draft or coloring coating option. In any case, a uniform layer is formed on the surface without a single seam. Manual application leads to a thickening of the coating and increased emulsion costs. Therefore, sometimes inviting professionals with special equipment is justified.
Mechanized processing is also preferred because it allows for higher quality. No roller will not help to embed the material in the base as effectively as the injection under pressure: adhesion improves, the work progress is accelerated. The cost of such a composition strongly depends on the chosen company, and the difference can be dozens of times. Most often it is just a fee for a big company name.
Even the need to attract trained professionals and pay them for high-quality processing does not impair the attractiveness of liquid rubber.As usual, before treating an exploited building, its entire underground portion is freed from the soil and carefully inspected. Convenient for work and not too laborious for builders will be a trench 70-100 cm wide, reaching to the bottom of the base of the house.
It is important to know that whatever method of treatment with liquid rubber is practiced, it is better to avoid doing work in rainy weather or in snowfall.
The coefficient of material loss is determined by the method of application:
- for manual application - 1.1;
- at vacuum deposition - 1.25;
- during spraying in the air flow - 1.4;
- when processing more complex forms - 1.6.
Manual work is carried out in several layers (up to the standard thickness), the machines apply waterproofing almost always in one go. Liquid rubber is applied in the direction from the base of the foundation to the basement of the building. Checking the quality of work is made by cutting the upper lobe of the rubber layer and trying to lift the material. When it comes off little by little, the result should be recognized as satisfactory, but if the separation occurs immediately along a large strip, then you need to remove the coating and start all over again.
The waterproofing of the tape base has its own characteristics. For this purpose, all the methods described above can be applied: roll, coating and spray. Among the materials of the first group above the others are valued by experts:
- film polyethylene;
- ruberoid;
- geotextiles.
Horizontal waterproofing tape grounds spend, maximally cutting off the effects of moisture on the structure. A watertight cushion of gravel and sand with a total thickness of 250 mm is laid down. Then a screed of a thickness of about 100 mm is formed, and for 12 days they take a break from work. While the screed dries and strengthens, you can calculate the right amount of bitumen mastic.
On a dry base impose several layers of roofing material and formwork prepared under the second line of screed. The final stage of work is usually the insulation of floors and the application of a decorative coating on them.
Vertical protection against water is provided by applying plaster on the strip foundation, surrounding it with special rolls, spraying mixtures. In the opinion of professionals, in this case it is recommended to combine a coating and glued materials.They start work with coating the surface with bitumen, then paste it on the technoelastic base. It is necessary to take into account that the surge of rolled coatings must be at least 150 mm. Sealing the seams is ensured by melting them with a gas burner flame, in which adjacent sheets stick together.
Pasting waterproofing is preferable in cases when it is impossible to use complex equipment. Before starting work it is recommended to check the surface readiness:
- removing the bulging parts of the reinforcement;
- removing concrete overflows;
- closing recesses;
- cleaning and ensuring the dryness of the outer edge.
Sticking materials on vertical surfaces is carried out from top to bottom (the opposite technique is not recommended for technical reasons). Experts advise to pre-cut the rolls into sections of the required length. The outer joints of the strips are coated with a putty and smeared with hydrophobic mastic for 1-1.3 mm. The raid of the bands is required from 15 cm and more. When sticking bitumen bricks, it is better to melt them in a mixture with transmission or used oils (20% of the mass of the briquette itself) - then the mixture will become more viscous.
Self-adhesive materials are the easiest to apply.
Rolls of a mixture of bitumen with polymers occurring in most building stores are glued after heating with a gas burner.
It is important to know that you should only heat that part of the roll, with which they work at a particular moment.
Pasting of roofing material is the most traditional option, but it is not necessary to give preference to it, because there are more reliable and effective methods for waterproofing foundations.
Where groundwater is high, conventional ground protection measures have only a limited effect. The cut-off waterproofing helps to solve this problem 100%. Its action is provided by penetrating reagents that appear during chemical reactions of applied compositions with concrete or bricks. Cracks and smallest pores overlap in the massif of the structure. Automatically blocks the flow of water into the wall sections above.
Cut-off waterproofing begin to create a preliminary drilling holes, entering the material at 2/3. Insulating tools are selected according to the type of foundation. For example, Silicone siloxane reagents are intended for processing:
- natural stone;
- bricks;
- concrete blocks.
As a result of this treatment, stable water-impermeable films occur, enveloping any capillary or micro-crack outside. When the foundation contains lime, it is required to use penetrating insulating means, obtained from solutions of alkaline silicates. The result will be the same - the formation of a microscopic barrier that completely stops water during the reaction. If damage to the plaster is detected, then before applying the cut-off waterproofing, it should be removed at a distance of at least 80 cm from the wetting point.
Gypsum plaster mixes are subject to total removal.
Drilling holes is carried out in two rows, they are placed in a checkerboard pattern. The hole diameter ranges from 2.5 to 3.2 cm, and the gap between them is allowed from 250 to 300 mm. For basement walls not exceeding 60 cm in thickness, the hole is wound up by a maximum of 2/3, always leaving 100 mm to the opposite edge. If the walls are thicker, then they are drilled from two sides, making a run.
In either case, the hole is drilled at an angle of 35 degrees or more to the horizon line. Each hole lead so that it crossed the horizontal seam of the masonry. In thick foundations it is necessary to ensure the intersection immediately with a pair of stitches.When drilling stops, each hole is washed with water so that there is no dirt in it. Further work is carried out only after the final drying.
In hollow foundations, holes are filled with special mixtures, and when they freeze, they are re-drilled with drill bits of reduced diameter.
Through the newly obtained holes, the remaining dust is blown through.
This technique allows you to minimize the consumption of penetrating impregnations. The injection of the shut-off waterproofing can be done with or without pressure. Feeding the mixture under pressure, thereby achieving a better result and enhancing the protective properties. Non-pressure version is valid only for those cases where the moisture content in the wall is minimal. The fill is made in the bore holes drilled at an angle downwards - for this it is good to use a watering can with a funnel.
It is important to know that the liquid will penetrate the wall at least 24 hours. Pressure injection of waterproofing involves the creation of an overpressure pump.
After the penetration of the penetrating material into the wall, it is supposed to seal the holes with typical construction mixtures. If there is no experience of such works, it is better to turn to professionals. This is exactly the situation when attempts to save money turn into serious problems. Skillfully prepared water cutoff will allow the walls of the foundation to stand for several decades without any problems. Choosing the right material is also better to provide knowledgeable people.
Foundation waterproofing is often performed using various types of film. The advantages of using them are obvious:
- 100% liquid tightness guaranteed;
- the occurrence of fungal and putrefactive lesions is excluded;
- processing is simplified;
- the coating is light and flexible;
- waterproofing the foundation is cheaper than usual.
But there are also disadvantages: the cheapest film has low UV resistance. Regardless of the price, the coating is easily torn, cut or scratched with ordinary tools. When it is laid, you will have to take care of protection from rodents. If the film thickness starts at 200 microns, and it itself is made of strong stabilized polyethylene, the stability of the coating will be even greater than that of bitumen solutions.
Unsuccessful stabilization polyethylene and polyvinyl chloride serve less.
But to get around this limitation is easy - you just need to apply a thicker material. The best coating is considered to be a film from 0.06 to 0.12 cm. Cheaper than other coatings, but also more vulnerable than them, is ordinary polyethylene. In modern versions it is even supplemented with special additives that compensate for this weakness.
The reinforced type of polyethylene rolled up has a core made of polypropylene or nonwoven materials. Separate modifications are additionally perforated, but only products without perforation are suitable for the foundation of a house. The optimum density of hardened polyethylene is from 0.1 to 0.25 kg per 1 sq. Km. Membranes with diffusion effect also have many layers, allow steam to pass and at the same time keep liquid water qualitatively. Professionals consider superdiffusion membranes to be the best variety.
PVC film is used more often than other options, because 1 mm is enough for reliable protection from accidental mechanical effects. Under film construction, the base is supposed to be moistened and coated with standard mortar.Films are put with a foray of 350 mm or so, a mounting tape or specialized glue is used to glue the edges. Top is applied another layer of the solution. The use of polyethylene is allowed even in the case when the basement is not organized, and the slab is made the basis for the first floor of the house.
For many decades, all these materials were unknown or not used specifically for waterproofing the foundation.
Therefore, there were no special alternatives to its protection from moisture with roofing felt. But even in a situation where the choice is very large, you should not ignore this material - it is still one of the best solutions. The classic type of roofing felt is made by impregnating cardboard with bitumen.
In newer versions, a different constructional basis is used:
- polyester fiberglass (any kind of hardened paper that goes far in strength);
- cellulose fibers;
- various grades of nonwovens.
It is important to know that the use of European roofing material for the foundation is impractical - this coating is intended for finishing roofing elements.
Rubemast (based on cardboard sheet) is much better. It is not recommended to nail ruberoid with nails or press it with rails - specialists use special mastics to attach roll material. All cleaved areas, cracked areas and any other deformations must be removed beforehand.
First, bitumen heated to fluidity is applied to the surface and a sheet is immediately applied. The raid of the ruberoid on each other should be from 70 to 120 mm. At the edges of the material is bent, put on top of the vertical insulation. Most often two lines of roofing material are mounted: one above the other.
Using this approach, the reliability of protection grows dramatically. All work is carried out only in dry warm weather. But if you break this rule, the effort will be in vain.
Only occasionally do home craftsmen apply insulation with rubber and rubber in a bundle. Ignoring this method in vain, because it gives amazing results. The bottom line is that the stone and roofing material are bound with thin rubber. It turns out the coating is both monolithic and characterized by high elasticity.
The benefits are obvious:
- much less rubber is spent than when used in its pure form;
- roofing material does not need to heat or prepare glue;
- work is accelerating and becoming safer in fire respect;
- waterproofing is being formed, capable of serving as much as the foundation of the protected house.
In those days, when ruberoid was not yet produced, the main method of protecting buildings from moisture was ordinary clay. Today it is used much less frequently, but still, clay rocks remain an indispensable aid in the formation of a water intake gate. The first step is to soak the clay for 24 hours using a small amount of water. When time passes, the mass is kneaded so that it acquires the consistency of thick cream. To improve the practical characteristics of the mixture can be the introduction of fiber shavings.
Then the foundation is poured around the perimeter of the prepared composition and kept open until the mixture completely dries. Judging by experience, the clay valves dry up in about a month, but by the middle of the second week, if there is an urgent need, work can be resumed. On dry hot days, the filled mass is covered with polyethylene and sprinkled with water every day.Ignoring this technique may lead to the formation of cracks.
Clay shutters complete waterproofing. They are especially important when using roofing material or fragile and unstable mechanically materials.
You can not use for a long time stored roofing material - it can stick together inside and become covered with cracks during promotion.
You have to either buy a new material, or put up with the poor quality of waterproofing. Bitumen should be heated not only at the joints, but also in all areas where it is adjacent to the surface. Recommended working temperatures are not lower than 12 and not higher than 25 degrees. Qualitatively perform work on the waterproofing of the foundation with roofing felt without assistants will not work.
How to choose?
After reviewing the various options to protect the foundation of the house from the water, you need to decide which of these methods is better in a particular case. Before choosing a waterproofing scheme, you should not rely on the experience of neighboring areas (even closely located), on technical documentation or on information obtained once upon a time.
Responsible owners prefer to carry out surveying their land.The advantage of this manipulation is that it will provide valuable information for other phases of the construction and development of the site. When building a house in a swampy or wetland place you will have to spend a lot of effort and money on waterproofing and drainage work.
Shallow foundations cover in this case, the outside of the protective walls. Each of the sides of the base is to be treated with a mastic, overlapped with any rolled material on the outside. Bored support structures in particularly difficult areas are subject to impregnation or external coating with reinforced mastics. Belt foundations cover at once with several layers of protection - after the coating with bitumen a roll coating is put.
It must be placed so as to exclude the appearance of cracks or poorly covered places.
When problems are great, it is recommended to carry out penetrating waterproofing. Houses that do not have basements are covered from below with horizontal protection. If there is a basement, it will also be necessary to equip the vertical insulation, complementing it with a drainage system. The simplest method of hydraulic protection available to non-specialists is the use of bitumen. If the work was not carried out on time, you will have to resort to one of three ways:
- cut the walls, placing bitumen or roofing felt in the holes formed;
- raise the foundation and lay the same layers normally;
- carrying out a crystalline injection.
“Prick” into foundation structures is a relatively simple and fast way. But the cost of it is very high. The bottom line is to make holes at the intersection of the base and the bearing walls. A combination of water, silicate actives and cement is poured into these holes. Mineral mass becomes an excellent barrier to fluid.
Thermal injections are made by entering heated air into the same holes; walls should warm up to 30 and even up to 40 degrees.
In addition to choosing the right option, it is important to take into account the consumption per 1 m2 of a specific type of waterproofing. When calculating take into account:
- type of protective agent;
- thickness of the formed layer;
- type of base;
- conditions in which the foundation will be operated.
Impregnating bitumen waterproofing is recommended for porous substrates and basement structures.If you apply the material on a flat surface with a layer from 0.1 to 0.3 cm, then you need to expend 0.8 kg per 1 square meter. If cracks are detected, the recommended flow rate grows by another 300 g. When using a Kalmatron in two layers, it will be necessary to apply 1600-3200 g of material each. When the decision is made to glue the foundation with rolled materials, the calculation is carried out taking into account the number of layers, the width of the blocks and the required run of strips against each other.
Liquid dye mixtures (bitumen and some others) should be applied at 800-2200 g to cover 1 m2 of base. The coating option is less economical - consumption ranges from 2 to 3 kg. If the choice is made in favor of pure bitumen, then it is necessary to take into account the appearance of the treated surface and the processing conditions. The average figure reaches 2 kg per 1 square. It is recommended not to forget about how much material will remain after the final drying.
Preparatory work
The figures for the consumption of waterproofing materials in terms of entire walls are very impressive - you have to spend a lot of money. So that the money invested and the effort spent are not wasted, it is worth carefully and thoughtfully prepare for work.
Prevention of water penetration through the base of the foundation is provided by the bottom waterproofing. It is usually done as follows:
- pulling out the pit, level and compact the mixture of rubble and sand;
- impose on them geotextiles;
- put a membrane film;
- put a new line of geotextiles;
- lay out polyethylene.
The bottom of the trench so equipped is sprinkled with 0.2 m of greasy clay. The clay layer is leveled and rammed. Then pour concrete 50-80 mm into the screed. When everything hardens, waterproofing is carried out with bitumen mastic. A ruberoid is laid out above the pillow, covered by another mastic shell.
She, in turn, becomes the support for the next roll. Now it is required to fill in a coupler of 50 mm. After 120-180 minutes, the technology is supposed to sprinkle the tie with a fine fraction of the sifted dry cement and level it. Once the concrete mass gains full strength, you can begin to fill the main part of the foundation. Of course, such preparation does not mean that other measures to protect against water can be ignored.
The foundation itself is prepared for waterproofing, cutting off all reinforcement that goes beyond the contour of the structure.
No protrusions should remain, otherwise the protection layer can then be destroyed by the action of solid particles of soil.
To remove dust and various kinds of dirt will help a metal brush. Solvents remove rusty and greasy stains, deposits of paint and varnish, because the smallest foreign film can degrade the adhesion between the structure and waterproofing.
When the foundation is opened and cleaned, preparations cannot be considered a completed task. Experienced craftsmen at this moment literally centimeter inspect the structure. Any sink, crevice or damage should be sealed with cement mortar. Construction sealants will help close the seams. A bitumen primer is always applied outside and inside.
How to do it yourself?
Correctly performing waterproofing, you can significantly simplify the use of various materials and structures for insulation of the foundation. Horizontal waterproofing is created under a wooden house, usually for 12-17 days. It is useful to consider that the upper parts of the foundations are also subject to waterproofing - the service life of the lower rims of the house depends on it.
The trench used for drainage is placed 200-250 mm below the line of the foundation to be poured, it is directed by a slope into the well concentrating the water.The bottom of the trench is laid with geotextile, its edges are wrapped on walls (0.6-0.7 m of overlap is enough).
50 mm of gravel should be poured into the prepared trench, putting a drain pipe on it, the slope of which should be 5 degrees for every 1000 mm of the path. It is necessary to take into account that it is possible to achieve the necessary inclination if gravel is added in certain places. Stone backfill above the pipe is 200-250 mm, then the protruding ends of the geotextile are laid over it and press them with soil. Carefully follow the instructions, you can skip to the pipe all the liquid and guaranteed to eliminate its clogging. The magnitude of the diversion pits or wells is calculated for each site individually.
Tips and tricks
- When working with hot bitumen and types of materials based on it, they should not be allowed to cool, otherwise the waterproofing will lose some valuable properties. If you can not use the burner to warm the joints, you can apply mastic with an adhesive effect. But this method is considered less reliable than heat. When using plaster to protect against water, you can use a putty mesh held by dowels.Such a lining reduces the risk that the finishing layer will suddenly disappear.
- Liquid rubber is divided into two groups. "Elasstomix" is always applied in one run and wait 2 hours for drying. An open container should be immediately used or disposed of. "Elastopaz", although somewhat more accessible, should fit into two layers.
- Recently appeared mats with clay filling should be laid out with the approach of one layer to another 100-150 mm. Panels of clay and concrete can replace the matte design, but the joints will have to be further processed.
It is important to know that all methods of protection with clay materials - both classical and modern - can be used only for non-residential buildings.
- For monolithic slab bases that are not equipped with horizontal protection during the construction phase, bitumen-based rolls are excellent. Alternatively, they can be treated with liquid rubber. Waterproofing of pile-screw and pole foundations often does not make sense, if not take care of the corrosion protection of metal parts. But the final decision on this matter should be taken only after consulting with experts.
- Finishing with bitumen makes it possible not to think about putting up small gaps. The material itself will leak into them and block the water inlet channels. On monolithic reinforced concrete foundations, a considerable part of experts recommends the use of Penecrit suture material in combination with penetrating Penetron. As carefully as possible it is necessary to approach the waterproofing of those areas where the gym, sauna or steam room, as well as other places of leisure are located. Even if the instruction to the material allows you to work at temperatures below +5 degrees, it is better to act without haste and in more comfortable conditions.
- When choosing waterproofing options do not need to be limited to previous experience, the advice of friends or information about the foundations of neighboring houses. Often, new solutions are much better and more practical. It is recommended to conduct not only geological surveys, but also chemical analysis of soils at different levels in order to assess the potential aggressiveness of the fluid passing through them.
Waterproofing plaster is not the best choice for prefabricated underground structures. Even their insignificant movements provoke the formation of cracks and peeling of the protective coating.
To clean the surfaces of the foundation you can use:
- percussion machines with pneumatic and electric drives;
- hand brushes;
- sandblasting technique.
Acceleration of drying is achieved by electric heaters and infrared emitters. When installing reinforced concrete blocks, a place for striking should be provided in each seam. If this condition is not initially met, then all such places will have to be opened and minted. Cutting seams using a perforator or a jackhammer should be carried out immediately to the full depth. When cracks are discovered that are 0.3 cm or more exposed outside, each such defect must be cut at least the same depth.
Smaller flaws are usually washed with high pressure water.
This procedure is performed with mechanically opened cracks. Paint waterproofing should be used strictly on the side where the water acts. It is preferable for the monolithic base.
It is important to remember that only penetrating treatment can compensate for external pressure.
If water passes through walls or floors, any other waterproofing will peel off and degrade.
The initial layer of bitumen is placed only on a dry surface. Among the rolled coatings, the best results come from the latest developments: ecoflex and isoplast. It is impossible to dig up the entire foundation in order to equip or repair the protection against water - a bare foundation can provoke uneven deposition of the structure and the appearance of cracks. The high cost of penetrating insulating compositions is fully justified, because their effectiveness is higher than when pasting or coating.
In some cases, waterproofing is carried out impermeable to water concrete. It is obtained from conventional formulations by introducing various components: liquids, powders or pastes. Choosing a specific option, it is desirable to take into account the temperature characteristics of the terrain, as well as the level of seismic and landslide hazard. In any case, waterproofing should be raised above the highest level of groundwater at least 500 mm.
The height of the capillary rise of liquid water for different breeds is assumed as follows:
- sand with coarse grain 0.03-0.15 m;
- sand with fine grains of sand from 0.35 to 1.10 m;
- sandy loam - from 1.1 to 2 m;
- light loam - up to 250 cm;
- loess and clay soil - from 400 cm;
- clay - up to 1200 cm.
If a certain structure is designed with a crack tolerance of 0.2 mm, then painting waterproofing of both bitumen and plastic, as well as cement plaster will not work. Attention should be paid to stray currents, details of protection from which are set out in the regulatory documentation. When it is known that the wall will carry intense shear, tensile or, conversely, compressive effects, waterproofing from a mixture of cement and sand is preferable. It is also recommended for places with an increased level of seismic hazard. For the preparation of any structures, the lining under the insulating layer is formed of concrete category B12.5.
When circulating aggressive water in the soil, it is recommended to use a lining of 4 cm thick asphalt concrete.
This lining is preceded by a cushion of 6 cm thick gravel, thoroughly spilled with bitumen. Paint waterproofing under hydrostatic pressure can be applied only in the absence of expansion joints. At the same time there are two more restrictions: access for a systematic inspection and the maximum value of the head of 500 cm.
According to technological standards it is prohibited to apply for waterproofing:
- tar lacquers;
- liquefied bitumens;
- varnishes bituminous.
The minimum adhesion to concrete in the painting version of waterproofing is 100 kPa. The thickness of the plaster coating can vary from 0.6 to 5 cm. It cannot be used if the surface can be subjected to a deforming load or vibration. If construction or concrete solutions with the additive “HYDRO-3” are selected for protection from water, then they will help prevent capillary suction, liquid moisture and hydrostatic head up to 200 cm. less than 50 and not more than 200 mm.
Suitable conventional masonry or mounting grid. But it should be removed from the bearing part of the foundation by at least 0.5 cm. Plaster-cement protection against water is carried out in a ratio of 1: 1 or 1: 2 (the second figure shows the proportion of sand). The method of gunning is recommended mainly for monolithic concretes. Plastering in more than three layers is not allowed.
If the hydrostatic pressure does not exceed 1000 cm, then their total thickness is limited to 2 cm, and at a larger value - 3 cm.
Waterproofing the foundation with cold asphalt is prohibited by regulations if water contains petroleum products or has a strong acidity.
Such waterproofing is almost always installed on the side from which the liquid comes from. If it is to interfere with capillary flow, an opposite mounting is allowed. The horizontal asphalt layer is covered with a cement or concrete screed. For a vertical surface protection is constructed on the basis of masonry, slab concrete. Flat asbestos cement and cement plasters (10-20 mm) are also allowed.
The process of waterproofing and warming the foundation, see the video below.