How to make a boiler with your own hands?
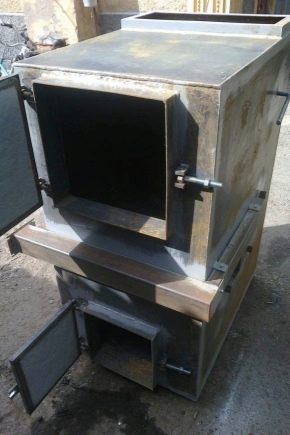
In the Russian market there are many models of heating boilers. But very often the cost of such structures turns out to be excessive, or something does not suit technically. Many find a way out of the situation in the independent production of boiler equipment.
Features homemade installation
Before taking on the case itself, it is necessary to find out what are the advantages and disadvantages of self-manufacturing of the heating boiler.
Positive sides will be:
- individual design (as fully as possible taking into account the peculiarities of the house and the heating system);
- cost reduction;
- pleasant emotions from a job well done;
- the highest responsibility (rarely in large enterprises works as well).
But there are also difficulties:
- the need to independently calculate everything;
- the need to understand construction materials;
- an obligatory condition is the skill of owning tools;
- availability of free space where you can safely perform basic work;
- the inability to make a complaint to anyone in the event of an unstable, abnormal operation of the boiler.
For all at least minimally trained home craftsmen, any of these problems is not very relevant. Most people prefer solid-fuel (rather than gas or liquid) structures, because their device is easier to perform. When working in artisanal conditions, this circumstance is very important. At the same time, among solid fuel boilers the most popular ones are based on the mining principle of operation, because they ensure long-term stable combustion. Such systems, in turn, are divided into two subclasses - classical and pyrolysis schemes.
Any mine boiler has two main chambers, divided vertically.One of them is used to burn fuel, and the other is a heat exchanger.
Most video tutorials and printed manuals show a simpler organization chart, including:
- firebox (it accounts for 50% of the total);
- loading hatch (located at the top or side);
- ash accumulating chamber;
- grate;
- door to remove ash (with gate);
- heat exchanger chambers;
- chimney.
When the boiler is put into operation, the hot gas rushes into the chamber with the heat exchanger and gives energy to it through the coolant. Smoke flows into the pipe allocated for it, the water goes into the heating circuit. The pyrolysis boiler is more complicated. If you watch a video showing the first launch of such an installation rated for 45 kW, the difference is noticeable quite clearly. The specificity of the equipment is due to the use of chambers for burning and post-combustion of carbon monoxide, a pipeline for re-supplying air and a wall valve separating the main working compartments.
The pipe through which the air is recycled has abundant perforations. The pyrolysis effect occurs due to the decomposition of the fuel with incomplete air supply to the compartment.Products of partial combustion are burned in a different compartment. Such a solution makes it possible to increase the efficiency of fuel combustion and “extract” a maximum of thermal energy from it. But there are a number of other nuances that must be taken into account.
What needs to be considered?
Kinds
The boiler of long burning can work on:
- wood (wood);
- hard coal;
- sawdust;
- pellets from wood waste (pellets);
- dissimilar types of fuel (universal type).
In this case, it is categorically unacceptable to use in such heating devices:
- laminate;
- chipboard;
- fiber board;
- glossy paper;
- liquid fuel;
- paintwork materials, alcohol, perfumery and cosmetic products;
- any prints.
Loading of fuel, with the help of which the heating of a private house takes place, can be carried out manually or be partially an automatic process. In the latter case, there is a capacious, periodically replenished bunker, from where the heating equipment takes new portions of fuel. Combustion of used fuel can occur not only according to the traditional or pyrolysis scheme, but also according to the type of "upper combustion".Additional differences can be associated with structural materials (steel or cast iron) and with the number of working chambers - 1 or 2. Systems with one circuit can only heat the heating system, and with two lines they can also supply hot water to the water tap.
Coal boilers, including those made by hand, are distinguished by an increased duration of burning at one gas station, and increased heat release. Connoisseurs of environmental characteristics choose mainly wood heating equipment. But it certainly requires a spacious working chamber, a door of wide width. This allows to some extent compensate for the relatively low efficiency of the use of firewood.
Pellet boilers, in contrast to the ordinary ones, farthest left the “oven” progenitors. Such heating equipment is distinguished by the highest degree of automation. Carefully prepared wood burns with almost no residue, so the amount of ash is minimal. But for gardeners and gardeners it is rather a minus, in addition, the prevalence of pellets is still small, in many places it is quite difficult to get them.In addition, any automation means a mandatory connection to the power grid (and dependence on it).
Another weakness of pellet-based automated systems is that they are more complicated than usual, and it is rather difficult to make such a boiler by hand. We'll have to thoroughly understand the device of automatic units and how they regulate the process of burning fuel. The use of the mining principle allows even when choosing wood to get heat for about 24 hours.
Coal in such systems burns even 6 times longer, but there is a significant drawback - it is impossible to replenish the outgoing fuel until complete exhaustion of the pledged mass.
If the classic type of heating boiler for long burning seems unnecessarily complicated, you can apply the construction of Kholmov at 25 kW. The choice of such a solution is justified when a very high efficiency is not too important, but you need the most convenient and comfortable product to use. It is always a mine structure, which, with full saturation of the combustion chamber, is able to warm up a house of average size from 12 to 16 hours. Holm boiler is found in both dependent and independent of electricity performance.
The system must include:
- thermal regulator:
- security group;
- grates of grates;
- branch pipes for connection to smoke discharge pipes;
- thermal expansion corrective devices;
- ash block;
- the doors.
The mass and dimensions of Kholmov’s boiler make it quite possible to put it in a normal doorway without extraordinary effort. In size, this water heater roughly coincides with most traditional stoves and can easily replace them in the same place. The upper doors are made double, with a layer of heat-shielding material. Thanks to him, the metal does not warm up to more than 80 degrees. The edges of the doors are glued over with an asbestos-based sealer; it is quite simple to reproduce this solution at home.
The design of the boiler according to Kholmov combines excellent efficiency and decent protection from fire. It can be safely installed even on floors made of wood. When an appliance circuit dependent on the power supply is selected, it must be supplemented with a fan and a device controlling the combustion process. The most popular are still simpler devices that do not need electric current and work on the command of a specialthermostat.
Accessories
It is very important to take into account the specifics of each component of the boiler. In solid fuel boilers you can find turbulizers (they are also swirlers) - this is the name of the parts that, due to their shape, significantly inhibit the flow of heated gases. This is necessary in order to increase the contact of the gases with the heat exchanger and increase the efficiency. Since the turbulizer is constantly working in an aggressive environment, it must be as resistant as possible to all harmful factors. By installing such a device in a homemade boiler, it is possible to significantly simplify the subsequent cleaning of the heat exchanger.
Also important is the thrust regulator. Independent of power supply adjustment is provided mechanically. Aluminum structures are most often made for this purpose because they are very “responsive” to temperature changes. The tubes at the top and bottom are placed near the wall of the boiler. Levers and fastenings of the crane axle box cut out angle grinders from sheet steel. The axis of the lever is located between the points of attachment of other parts to it.
The initial displacement of the tubes is determined by the crane. As soon as the tube at the top becomes longer, it pushes the lever.When the lever is rotated, the tube at the bottom starts moving, hitting the second lever, it causes it to release the chain. Since it no longer holds the damper flap, this flap descends and gradually burning subsides.
It is recommended to provide coordinated actions for the blower and the smoke channel. Then the flue gases will not go out too early. The reconciliation is that when opening the fan, the lumen of the chimney should also increase. A device that redistributes the force helps to solve this problem (most often it is a cable of small thickness connecting the second lever and the damper of the smoke channel). Additional details can be found by looking at a master class on thrust regulators.
With all the simplicity of non-volatile solid fuel boilers, yet the most comfortable for people are the options with the control unit. Those who speak a programming language should use an industrial device and customize it to suit their needs. Fully ready standardized systems can be mounted very quickly, but no adaptation to specific conditions can be provided. Another good option is the use of the Arduino platform.This allows you to use cheap controllers and supplement them with a variety of auxiliary equipment, but you will have to write program code in the SI language.
Instead of a blower, a considerable part of the boilers is equipped with a fan. This solution allows you to get a forced draft in the chimney, in addition to providing the most efficient combustion of fuel. Determine the required ventilation power can be given the highest boiler efficiency.
Competent selection and installation of the device will allow:
- extend the life of the structure as a whole;
- longer use insulating materials;
- reduce the risk of boiler room smoke.
Connectors for the fan, pump, mains connection and temperature sensor should be removed from the control unit. Usually, the automatic fan should start up when the fuel breaks out. When choosing a ventilation device, you should give preference to products of well-known and reputable companies. In addition to all the listed components, a home-made boiler should use a reliable tripod.
Materials
Most of the boilers, assembled and installed their own hands, made of stainless steel of various grades.
Almost always it is one of the AISI varieties:
- 309;
- 310;
- 304;
- 316;
- 321.
For chimneys of a solid fuel boiler, the metal category 309, 321 or 310 is preferably used with a thickness of 0.1 cm. This is quite enough for carrying gases in the desired direction, heated to 500 and even 700 degrees. Sometimes the smoke channel is made not from a steel pipe, but from a bricklaying (or both of these solutions are combined by inserting the pipe into a brick tunnel). It is imperative to use a fuzz that blocks the harmful effects of heat on the ceiling and roof structures.
For the manufacture of fuzz used natural stone, brick or concrete, since all three materials withstand even strong fire and remain strong.
Dimensions
The dimensions of each boiler and its auxiliary elements are selected separately each time. To facilitate decision making, you can use a ready-made device diagram, which is conceived by professionals. When preparing drawings, you should take into account the equipment of the cooking surface. Dual-circuit models are larger than single-circuit samples.
If the Kholmov boiler is going to be 25 kW, the typical dimensions are as follows:
- fuel loading hatch - 119 cm;
- coupling - 128.9 cm;
- ash door - 0.43 m;
- cold water supply - 76.5 cm;
- controller - 1.039 m;
- reverse input - 4.1 cm.
How to make?
It is necessary to take into account the general information about long-burning boilers to eliminate errors. If, however, selected not solid fuel, but an electric apparatus, it is necessary to give preference to a device that operates according to Tesla's law. There is nothing supernatural and contrary to the basic laws of nature. In the construction of the boiler, instead of the usual coil, a bifilar-type part is used. The essence of the principle of operation is simple: electricity does not counteract itself, since the reverse EMF is not created, and the potential is rapidly reaching its highest point.
Returning to the main topic, it should be noted that the developers always pay a lot of attention. It is mounted after finishing work on the boiler itself.
This is done like this:
- the fan is attached to the pipe;
- blowing joins the control system;
- all necessary equipment is connected to the network;
- adjusting the parameters of air pumping;
- a test ignition of the furnace is being done;
- after 5 minutes, an electric blow-up starts (then it “remembers” the optimal parameterswork).
Since any boiler is equipped with a heat exchanger, a booster is also required to effectively flush it. Buying such devices is not the most reasonable thing, because their cost starts from 20 thousand rubles, and these are clearly not the best versions. First, take a pair of solid plates of metal, their thickness must be exactly 0.25 cm. Drill holes (focusing on the fact that they coincide with the holes in the heat exchanger). “Americans” with an internal part are inserted into the bottom openings of the plates, then the plates are bolted to prevent the fittings from moving away from the heat exchanger.
The hoses are usually connected using brass fittings ¾, a container is also required (always cleaned properly). The fitting fixes the hose as tightly as possible. At this point it is necessary to prepare a reagent for washing; contrary to popular recommendations, it is impossible to use acids, even diluted. Now, having dealt with additional components for a solid fuel boiler and its maintenance, you can think about the design itself. Making the case to the exact size requires the use of welding.
It is much easier to make an ashpot, it's just a metal drawer with a handle.But the insulation of the boiler requires more attention. The amount of heat loss and the cost of heating directly depend on the clarity and correctness of this work. Light heat insulation is best created by an asbestos-cement solution, the boiler is closed with roofing felt, and a steel mesh is mounted on it, which holds the solution.
It is impossible to do without the advance formation of the frame, if you have to warm the boiler with mineral or basalt plates.
The frame is welded, then:
- mount a layer of thermal protection;
- strengthen it with a network of steel;
- lubricate the network with a solution of lime and slag;
- paint the resulting surface in the desired tone.
Prior to arranging thermal insulation by any method, the boiler body is cleaned and treated with anti-corrosion compounds. Be sure to warm the pipes associated with the heating equipment. To retain heat, the chimney is surrounded not only by cotton rolls, sometimes it is replaced by polyurethane foam. Important: it is possible to use polyurethane foam in liquid form only if you have the necessary training and specialized equipment. If neither one nor the other, it is better to think about other solutions to the problem.
Tips
Rinse a self-made boiler from the scale using the booster already mentioned. Preference should be given to products of well-known companies, then cleaning will take place without any risk to the equipment. Of course, before cleaning the boiler, it is necessary to disconnect it from the heating system, from the electricity grid and from the water supply system. Disassemble the heat exchanger only with a very strong blockage.
Ultrasonic cleaning, although mentioned in different sources, is unreasonably expensive for private owners.
Successful examples and options
There are various variations of solid fuel boilers. So, for example, a long-burning boiler is equipped with another version. The photo below shows a rectangular vertical black boiler with pink doors. This solution looks original and even unique. Waste oil boiler looks much more brutal, and is equipped with a number of vertical pipes.
How to make a boiler yourself, see the next video.