Heat-resistant paint on metal: how to choose and where to apply?
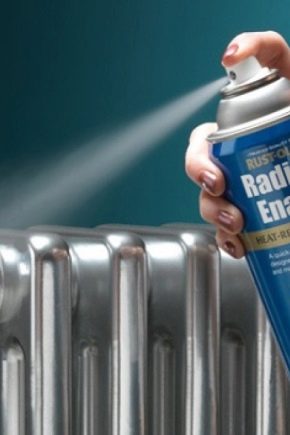
Metal is a durable, reliable and refractory material, its properties have been actively used since ancient times. However, under the action of high temperatures, even the most reliable structures are not strong enough. To reduce the negative impact of strong heating, and ideally block it completely, you need to use protective coatings for the metal. Of great importance in such cases is a special heat-resistant paint.
Special features
Fire retardant paint has a varied level of protection, special properties and nuances of application.There are two main categories: intumescent (intumescent) and non-swelling dyes. The second type is very expensive and not too claimed.
The protective parameters are achieved by reagents, which belong to one of three groups:
- containing nitrogen;
- containing phosphoric acids and derivatives of these acids;
- polyhydric alcohols.
Fire protection paints are formed by such components by 40-60%. Under normal conditions, they work as a standard paintwork, and as soon as the temperature rises, the generation of gases begins. A coke layer is formed, which lowers the effect of high temperature. Despite the identity of the principles of work, paints may have a different chemical composition.
Thus, nitrogen-based substances such as melamine, dicyandiamide and urea are often created - they make the paint less wear-resistant. The main polyols used by specialists are dextrin, dipentaethrin, pentaerythritol and starch. In addition to preventing burnout, alcohols enhance the adhesion of heat-resistant paint on metal.
Phosphoric acids also improve adhesion to the surface,guarantee durability of paint and varnish composition. When a fire starts, bloating occurs very quickly and intensely. As a result, the formation of smoke is reduced, smoldering and burning are significantly slowed down. The main components containing phosphorus inks are: ammonium polyphosphate, melamine phosphate, various salts and esters. Any standard fire retardant substances do not emit poisonous gases in the event of a fire; therefore, they are considered as safe as possible.
Specifications
In normal situations, fire paint is not much different from the standard, the difference begins to manifest itself only with a significant increase in temperature when the surface layer is heated. This circumstance becomes a catalyst for the synthesis of porous oligomers, their curing. The speed of processes is determined by the nuances of the chemical composition, the characteristics of the application and the degree of heating. The process itself will be:
Fireproof paint emits gaseous products.which start the subsequent process and prevent the temperature from destroying the coating layer. Phosphoric acid is released, forming coke foam.The foaming agent is destroyed, which is filled with a cushion of gases to prevent heating under the action of increasing temperature.
Chemical decomposition of substances containing phosphorus: the top of the reaction occurs when heated to 360 degrees.
Pyrolysis of mesh structures. In heat-resistant paint, it starts at 340 and goes when heated to 450 degrees with intensive foaming of protective layers.
At a temperature of 200 degrees the metal is strong enough, but as soon as they become heated to 250 degrees, as it very quickly loses its strength. When heated to high temperatures - 400 degrees and above, the smallest loads can damage the structure. But if you use good paint, you can maintain the basic qualities of the metal, even at 1200 degrees. The standard of protection is the preservation of basic qualities up to 800 ° C. How much paint can maintain its quality is determined by its chemical composition and purpose.
So far, technologists have created 7 categories of fire protection, the differences between them are expressed in the duration of fire resistance. The 7th digit means that the protection is running for a quarter of an hour, and the highest level is 2.5 hours.Heat resistant paint is usually able to transfer heat up to 1000 degrees. Such coatings are applied to heating equipment and other heating systems of similar purpose.
These parameters help to identify the labels on the labels. To provide sufficient protection for the brazier, various additional components are used - oxygen, silicon, organic matter and aluminum powder.
The purpose of the high-temperature compositions is the coloring of radiators and engines of transport, the joints of masonry brick kilns. If the heating is not too great - as on the details of a gas boiler - heat-resistant lacquers can be used, which do not lose their appearance at temperatures of 250 and even 300 degrees.
Heat-resistant paint can be made from alkyd, epoxy, composite, silicone components. Also, chemists have learned how to use ethyl silicate, epoxy ether combinations and a number of dyes based on heat-resistant glass for such purposes.
When choosing, always be interested in how fire-resistant composition is subject to cracking and other mechanical defects. After all, because of them, there may be significant problems at a critical moment ...
Manufacturers Overview
Since the actual characteristics of paint products are extremely important, there are a number of leaders who best protect the supporting structures. Coating "Thermal barrier" guarantees protection of steel up to two hours, the minimum level is three quarters of an hour.
Cost, parameters of paints can vary greatly. Nertex, for example, it is created on a water basis and reliably covers a design from high heating.
"Frizol" fully meets the standards of GOST, may have the properties of the second-sixth groups. The time of use of the coating is a quarter of a century, fire resistance meets all requirements.
Brand protection "Joker" works well, but it is advisable to apply it only in rooms where the level of security is equal to the second, third or fourth groups.
"Avangard" - products of the same name of the newly emerging company, but it has already managed to gain solid authority, become famous for the excellent ratio of efficiency and price.
It is important to consider that paint of any brand is less effective than the coatings specially designed to resist flame and heat.
Purpose
Heat-resistant paint can transform the product in any color. Designed for painting furnaces, the compositions have an excellent level of protection against corrosion and are not destroyed by moisture. Mandatory requirements for this group of paints - reliable protection against electric shock and the ability to transfer contact with aggressive substances.
All the target properties of the coating should be maintained both with significant heating and at low temperature, even if the drops are very sharp. Additionally, it is worth mentioning such a valuable parameter as ductility - the decorative layer should stretch along with the heating base, and not split. The lack of the necessary properties ensures the appearance of cracks after drying.
Heat-resistant paints for metal can be applied to any type of ferrous metal or alloy. The existing classification subdivides coloring materials according to various criteria. First of all, the packaging method. As containers use cartridges, jars, buckets and barrels. Another gradation is produced by dyeing methods, which determine the amount of paint consumed.
In everyday life, heat-resistant coloring compositions are applied to metal structures in baths, saunas, and wood drying chambers. They cover stoves and braziers, fireplaces, radiators, silencers and brakes of cars.
Kinds
In practice, the decorative properties of the paintwork are of considerable importance. In most cases, consumers are offered gray and black varieties of silverfish. Other colors are much less common, although if necessary you can use red, white and even green paint. The range of leading manufacturers found matte and glossy coatings of each particular shade.
Dyes in cans are relatively inexpensive compared to aerosol preparations. The aerosol, at an apparent low cost, is actually consumed very intensively.
If you want to paint the brakes of the car, then at best two of them will have to spend one spray. In addition, the risk of clogging paint other parts of the car is great, they need to thoroughly cover for the time of work. Drying time in most cases does not exceed two hours.
Important: for coloring non-ferrous metals have their own special coloring compositions.Be sure to ask about this when buying.
What to consider when choosing?
With the help of alkyd and acrylic dyes they decorate the constituent parts of the heating complexes - they will be able to transfer the heat to 100 degrees. The fee per kilogram of the composition ranges from 2.5 to 5.5 thousand rubles.
Using epoxy mixtures can be painted structureswhich heat up to a maximum of 200 degrees. Some of these paints do not require pre-priming. The price spread is much larger - from 2 to 8 thousand. The price tag is influenced by the capacity of the container and the brand of the manufacturer.
If you need paints for application on the brazier or barbecue, you need to use ethyl silicate and epoxy ether coloring compositions. Then the permissible heating temperature will be 400 degrees. Applying a one-component silicone compound, you can protect the metal from heating to 650 degrees; The basis for the mixture is a polymer silicone resin, occasionally mixed with aluminum powder.
When heat-resistant glass and composites are added to the paint, it can transfer temperatures up to 1000 degrees. It should be noted that the cheapest formulations can be used for apartment radiators, because they do not heat up more than 100 degrees. But metal furnaces in private homes regularly heat up to eight times stronger.The higher the allowable heating bar, the more expensive the coloring mixture is. According to the level of ecological and sanitary safety, water-based drugs are leading.
Additionally, you need to find out whether a particular paint is suitable for exterior or interior work. Glossy and light dyes heat up less well and give off heat to the outside for a longer period than dark ones. This is very important if you are going to paint the furnace, heating systems.
Recommendations for use
Proper application of fire protection agents is critical to their proper operation. Metal surfaces must be completely clean and free from all corrosion. The slightest raids of oils and mineral crusts are unacceptable. Additionally, remove all the dust, metal planes degrease. It is unacceptable to put fire retardant paint on without a primer, which must be completely dry.
The composition before use is thoroughly mixed with a construction mixerIt is left for about half an hour for air to escape. The best method of flame retardant painting is vacuum spraying, and if the surface area is small, you can do with a brush.
It is strictly not recommended to use rollers. They create an uneven layer that poorly protects against fire and high temperatures.
The average consumption of fire retardant paint is from 1.5 to 2.5 kg per 1 square meter. It is important to understand that these indicators are determined by the thickness of the coating, the type of application and the density of the composition. The minimum amount of paint is two layers, and in most cases there are 3-5 of them.
When the structure is located in sight, it can be covered with a decorative layer over the protective composition. The surface must be prepared as thoroughly as possible, strictly following the staining scheme and temperature conditions prescribed by the manufacturer. Clearly separate heat-resistant and heat-resistant paints. The last compositions are suitable only for registration of the most strongly heated parts.
If you decide to paint car calipers, do not remove them - these are useless costs and the risk of spoiling the brakes. First, remove the wheels, then the parts are cleaned of plaque and rust, only then paint them in two layers.
Getting ready to cover a metal furnace, always get acquainted with the original instruction to the preparation.Some formulations can be applied only after carefully thought out preparation. When there are no special instructions on this matter, you need to start by cleaning the surface from all traces of the previous coatings - oil, raids and dirt.
Rust should be removed with sandpaper, a drill with a special nozzle or a chemical rust converter. After removing even insignificant stains, the upper layer must be washed and dried.
The furnace must be degreased with a solvent, xylene or solvent.
Exposure after such treatment before dyeing is:
- in the street - 6 hours;
- in a room or technical room - 24 hours.
Paint the ovens with necessarily several layers of paint, which are applied in different directions, each after the previous one dries.
Important: the higher the permissible heating level, the thinner the coating should be. For example, if the paint is able to withstand temperatures above 650 degrees, it is applied with a layer of no more than 100 microns. This is due to the minimal risk of corrosion with significant heat compared with the risk of thermal rupture.
Always find out how large the temperature range at which paint can be used.In most cases, you can paint in the interval from -5 to +40 degrees. But some modifications have more features, be sure to know about them.
To learn how to paint the exhaust system with heat-resistant paint, see the following video.