Choosing an apparatus for welding polyethylene pipes
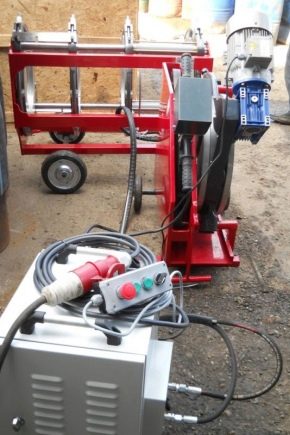
In recent years, polyethylene (PE) pipes have been actively gaining ground in the market of water and gas pipes, becoming the de facto standard for both the creation of new and the repair and modernization of existing pipelines. The most common method of installation of PE pipes is their welding using specialized equipment. The reliability of the pipe connection ultimately determines the durability of the gas or water supply system as a whole, so the choice of the apparatus for welding polyethylene pipes is an important task, which should be given special attention.
Special features
Choosing an apparatus for welding pipes made of PE, you need to be clear about what kind of work will be done with it.Features of the desired equipment will largely depend on the method of welding, which you plan to use most often.
There are four main methods of soldering polyethylene products.
- Butt joint welding - this method is the most common, and it is based on the connection of heated pipe ends with each other or with fittings using a special welding mirror. A butt joint allows to obtain a fairly high quality joint at a reasonable price for the equipment, but the method is not suitable for joining products with a wall thickness less than 4.5 mm. The use of butt welding requires thorough cleaning of the surfaces to be joined, maximum precision of the trimming of the products and application of the correct pressure on the pipes during their connection.
- Pipe joining to the socket (or clutch method) is a reliable, but less common and more expensive method based on joining products through a special coupling. There are also options for connecting directly two pipes of different diameters to each other. This method is not used for laying pipelines that are outdoors.
- Electrofusion (or thermistor) pipe welding - this method is similar to docking into a socket, but the coupling used in it contains a metal heating element, which contributes to a more uniform heating of the connected products and the electrofusion. At each electromultiplier there is a special barcode in which the parameters of the electric current necessary for this coupling are encrypted, therefore devices of this type are often equipped with a barcode scanner. The thermistor method is even more reliable (and more expensive) than the clutch one, therefore it is mainly used in cases when it is necessary to provide a very stable connection (for example, when conducting pipelines in areas of frequent earthquakes). This method is used to connect pipes with a diameter of 20 mm with any wall thickness, and the requirements for the accuracy of holding technological parameters in it are much lower than when soldering butt.
- Extrusion Welding is a method similar to electric welding; when applied, heated polyethylene is fed through a special extruder to the welding area, which forms the connection between the pipes. The strength of the obtained compound usually does not exceed 80% of the strength of polyethylene,Therefore, the extrusion method is usually used mainly to connect pipes with other plastic products and to install pipes with a diameter of 630 mm in places that are not likely to be subjected to high loads.
Kinds
All devices for welding of polyethylene consist of four main modules - a generator (usually operating on the principle of an inverter with a transformer or a switching power supply), a power control module, a temperature control module and a process unit, in which the connection process itself takes place. Each of the four welding methods discussed above is performed using an appropriate tool.
The machines existing for each of the 4 ways can be divided into 3 categories according to the degree of automation.
- Handhelds - they are usually the cheapest (the simplest soldering iron for manual butt welding costs from three thousand rubles), but the probability of an error during soldering is higher because they are very dependent on the human factor. Such devices are used only for connecting PE pipes of small diameter, most often in domestic conditions.Usually, devices for butt and socket welding are manual, although there are also manual extruders. Thermistor welding using a hand-held device is practically impossible due to the need to establish a specific current mode for each electric coupling.
- Semi-automatic welding machines - such devices are more reliable and more expensive than manual ones, and the operator’s role in them is to enter all the required welding characteristics (including wall thickness and pipe diameter, temperature of the welding process, heating time, application of pressure and cooling) to the control panel and process control. Semi-automatic units are made for all four types of soldering, semi-automatic devices for electrofusion welding are especially common.
- Automatic machine tools - in such devices, the operator only enters into the computer the basic parameters of the pipes being welded (material and dimensions), and the computer calculates all the necessary characteristics with the help of specialized software and transfers it to the machine, which performs all subsequent technological operations independently.A person needs only to enter the data correctly and ensure that the machine has enough consumables. Prices for such installations range from a few hundred thousand to a million rubles, and they are used for welding pipes of any diameter and allow you to ensure the best quality of the connection.
Semi-automatic devices are divided according to the type of drive used into mechanical and hydraulic. In devices with a mechanical drive, the force required to center and hold the pipes during the welding process is created by the operator, therefore they are used only when working with pipes with a diameter of less than 160 mm. The hydraulic drive does not require the application of force from the operator and is used for welding products of any diameter, including more than 160 mm.
Automatic PE pipe welding machines are exclusively equipped with a hydraulic drive.
Another important characteristic of the welding machine is the diameter of the pipes that it can connect, because the standard sizes of PE pipes are in the range from 16 to 1600 mm. For example, pipes with a diameter of 20 to 32 mm are usually used for conducting water supply in apartments.but for the installation of trunk pipelines may already need an apparatus capable of soldering pipes with a diameter of 90/315 mm or more.
The most popular devices are now firms Georg Fischer (Switzerland), Rothenberger (Germany), Advance Welding (United Kingdom), Eurostandard, Technodue and Ritmo (Italy), Dytron (Czech Republic), KamiTech and Nowatech (Poland). There are also Russian manufacturers of devices for welding of polyethylene, for example, the Volzhanin plant, which produces equipment for the soldering butt-welding of products with a diameter from 40 to 1600 mm and electromotive devices capable of connecting pipes with a diameter of up to 1200 mm.
How to choose?
When choosing welding equipment, first of all, it is necessary to clearly understand the planned volumes and conditions of work.
- A huge and expensive industrial machine will be useless to a simple plumber, and a cheap hand-held device will not help the company that builds an industrial high-pressure gas pipeline.
- If the laying of pipelines has nothing to do with your work, and you just want to repair the home plumbing yourself - you just need a very simple butt-top soldering iron for soldering, for example, Elitech SPT-800.
- When purchasing a device for butt welding, do not forget that this method requires strictly vertical cutting of the ends of the products being joined, so it will be reasonable to buy a special electrofetter with the welding unit that can cut pipes strictly at right angles to their axis.
- If you are not sure of your soldering skills, but are not constrained in finances, a semi-automatic machine for electrofusion welding, for example, Nowatech ZERN-800 PLUS, will allow you not to worry about a possible breakthrough of the water or gas pipeline after your repair.
If you are a professional, first of all carefully study the characteristics of the pipes you use to work and the possible conditions for their operation. Do not forget the limits of applicability of each of the methods (so, you should not perform soldering butt at ambient temperatures below 15 and above 45 degrees Celsius) and carefully read the instructions for any device before purchasing it.
In cases where the question ultimately boils down to the choice between a semi-automatic and automatic, remember that in order to properly use the semi-automatic you need to have experience in calculating all the required welding characteristics using special tables and charts.When buying a semi-automatic machine, you need to pay attention to the possibility of logging, which allows you to save the settings for welding in the same conditions (for example, using the same fittings), which saves time when you often perform the same type of work.
Some semi-automatic devices do not contain a built-in logging function, but may allow you to connect an external device for this.
If you have to work with a high-pressure main gas or oil pipeline, the best choice would be an automatic electrofusion machine, for example, the Georg Fischer MSA series.
It is important to remember that the effectiveness of the application of thermal resistance welding often depends more on the quality of the couplings used than on the parameters of the machine used, so never save on consumables.
When financial planning do not forget that, in addition to the cost of equipment, it is necessary to take into account the cost of consumables, because the use of an electrofusion method for installing a pipeline with a large number of connections can significantly increase the cost of work compared to butt or socket soldering.
If you do not plan to use the device regularly, you can use the rental service offered by many companies selling equipment for soldering polyethylene.
You can find out the technology of soldering plastic pipes by looking at the video below.