Granular expanded polystyrene: technical characteristics and scope of application
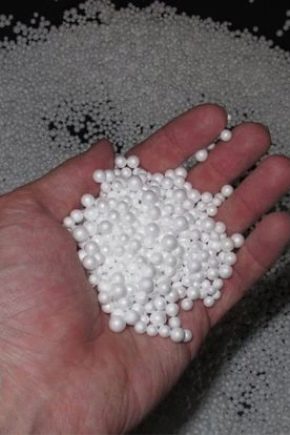
The accelerated development of the chemical industry made it possible to create a whole range of polymeric materials by the end of the twentieth century. These initially unusual substances were quickly appreciated.
One of these materials is granulated polystyrene foam. It stands out noticeably against other analogs, has a number of features and advantages.
Production features
The product under this name is made from a gas-filled mixture, the base component of which is polystyrene. In some cases, technologists decide to use additional components (polydichlorostyrene or polymonochlorostyrene) as a replacement.
In addition to the main active ingredient in production, fillers are introduced into the mixture, which increase plasticity, as well as additives that increase resistance to fire. In order to have a foam effect, lightly boiling carbonaceous reagents or special blowing agents are used.
Polystyrene foam granules are white. Balls of raw materials are placed in a special apparatus - the precursor. There, by adjusting the heating and pressure of the supplied reagent, one or other characteristics of the resulting sheets can be set.
Then the granules are cooled and dried. From the dryer they enter a temporary bunker, which is a polypropylene bag. In this tank, permeable to air, they are kept for 1-36 hours (the exposure time is determined by the fraction value).
Next, perform molding. In the block form, steam acts on the granules for 60-180 seconds. As a result, polystyrene foam forms rectangular blocks. The temperature and humidity indicators and pressure maintained during such processing are important: the consistency of the finished goods depends on them. The formed block is left to cool for 10–40 minutes; vacuum technology is used to accelerate this process.
The constructions stabilized on the holding platform are cut by another installation, in which heated wires act as knives.
Species
There are two main subspecies of it: primary and repeated. Initially, polystyrene granules are heated using:
- liquids;
- water vapor;
- of air.
When this occurs, the increase in size and transformation of the flat structure into round balls. In the second embodiment, the starting point is the passage of waste foam products through the crusher. It is not always possible to achieve such an even and comfortable external shape. About a third of all secondary products are far from the circumference. But it does not create any problems in purely practical terms. The size of the crumb ranges from 0.1 to 0.8 cm.
Manufacturers denote this by various indices. The smallest expanded polystyrene is classified as M-15, while the largest fraction is indicated by the marking M-50. Transition dimensions are marked with the word "Light" (for example, M-35 "Light"). Depending on the value, the practical properties of the material change, and its total cost is adjusted.
The following parameters are crucial when choosing:
- bulk density;
- compressive strength;
- level of thermal conductivity.
Scope of application
Granular expanded polystyrene has found the widest application in various fields of technology.
The most frequent options are:
- filler furniture and toys;
- internal heat protection of building structures;
- sound suppression in enclosing elements;
- preparation of polystyrene concrete;
- production of building mixtures with low thermal conductivity;
- purification of sewage to sanitary necessary indicators;
- improving the quality of agricultural land;
- fishing;
- do-it-yourself cooking of various decorative designs.
Advantages and disadvantages
Granular expanded polystyrene has a number of attractive characteristics. It perfectly retains heat in a given volume or prevents its overheating in the summer months.. Along with this property and damping of sounds, increased durability and minimal absorption of moisture into the mass are guaranteed. According to these indicators, the material bypasses the recognized insulation materials like mineral and ecological wool and expanded clay.Advantages when using polystyrene foam as a warming agent are quick steam and cold resistance.
Since the foam balls are saturated with special additives, they completely correspond to the class of fire protection G1 (hard combustible materials). At the same time, a carefully selected composition allows to ensure a zero degree of environmental risk. All these advantages of expanded polystyrene will remain unchanged under normal conditions for at least 50 years. But it is with “normal” conditions that problems most often arise.
The slightest impact of solvents for paints and varnishes, as well as ultraviolet rays in the open, can destroy expanded polystyrene.
Information for selection and work
According to its characteristics, polystyrene foam M-15 is not good enough for insulation of building structures. It is recommended to use for this purpose material categories from M-25 and above.. The only exception is made for cabins, containers and other household, auxiliary buildings for various purposes.
It is unacceptable to use M-15 even where a significant mechanical load can affect a material.The bending strength of plastic of this brand is not more than 70 kPa.
Granulated material with a fraction size of 1, 2 mm and any other after compression by 10% according to the standard must be restored to almost the original form. The limit of permanent deformation after testing according to the standard program cannot exceed 2%. The denser the granules, the higher the allowable compression, it allows you to choose the ideal solution for a particular case. Expanded polystyrene can be used for warming walls and roof structures. As an additive to concrete recommended its use for floor screed.
Additives of other binders are not particularly needed, they are used only for the preparation of polystyrene concrete. It is easy to paint styrofoam, it slows down the electric current well. Therefore, it can be mounted close to home wiring. Water absorption is relatively small, while gluing sheets or gluing them to the base is not difficult.
It is unacceptable to use this material where temperatures can occur more than 200 degrees, it will quickly lead to the destruction of structures and parts.
In the production of warm cement, the ratio between polystyrene foam and dry cement is 1: 1 in volume. When preparing such a mixture, only water should be added. There is no need to use sand.
It is necessary to work with granules during construction and repair carefully due to their light weight. The slightest movement of air leads to instantaneous dispersal of the material throughout the room. because it is necessary to close all windows and doors, it is impossible to turn on the fan and the conditioner, it is not necessary to make sharp movements. When cooking, it is not polystyrene foam that is put into the solution, but vice versa (the solution is added to a container with granules).
The features of expanded polystyrene are:
- lack of foreign odors;
- elimination of toxic emissions;
- processing without dust;
- resistance to fresh and salt water, gypsum, alcohols, construction paint;
- resistance to bitumen, fertilizers, silicone-based lubricating oils;
- the impossibility of the formation of fungal and bacterial colonies;
- eliminating the risk of insect eating.
Saving heat and sound damping is ensured because the granules contain a mass of microscopic cells with thin walls.The area of contact with air turns out to be huge, if you compare expanded polystyrene with other materials of similar purpose. Styrofoam spontaneously ignites only at 491 degrees of heat., which is much better than using wood. The slab, which is not exposed to the effect of an open flame for 4 seconds, fades itself (not supporting burning). The fact that the material does not absorb water allows not to be afraid of swelling of the material.
To insulate a tiled, parquet or plank floor, it is required to use polystyrene foam granules with a density of 300 kg per cubic meter. m
As a warming base for waterproofing roof structures, a material with a density of up to 200 kg per m³ is used, because each kg complicates the work of builders. Polystyrene concrete mixtures can be laid even on uneven surfaces.while the pressure on the floor increases only slightly. The solution is placed after preparing the base and cleaning it from the slightest dirt. At the bottom there should be a vapor-proof casing (most often they put a film of high-pressure polyethylene).
You will learn more information about granulated polystyrene foam from the following video.