Production of concrete stairs for country houses: calculations and methods of pouring
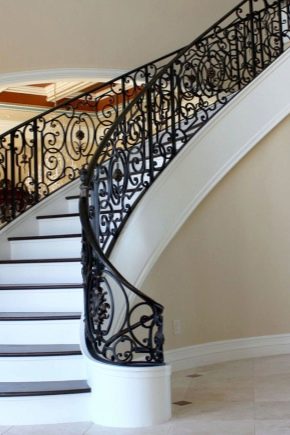
In any staircase, the most important thing is reliability, safety and beauty; therefore, most often, in the manufacture of stairs, an artificial material is used - concrete.
To date, this material has no rivals for strength and service life.
Special features
The versatility of concrete along with innovative design and finishing processes allows you to create monolithic structures that are visually pleasing and extremely stable in a private home. Using the leading production technology of Northern Europe, formwork provides excellent quality finishes.
Concrete is well known for its durable, reliable properties. Concrete structures are resistant to erosion and damage from flooding or fire, and are also supplied in units that can be installed quickly and efficiently at any stage of the construction process. Built into the wall, these separate step blocks (weighing about 130 kg per step) are supported vertically along the front edge, and the wall on which one end is built provides torsional retention.
Due to the thin overall thickness, the design provides greater aesthetics compared to traditional methods of designing a country house.
Safety conditions
Each residential staircase with four or more risers should be equipped with safety rails. Installers must install them 34–38 inches above the stairs, and handrails cannot protrude more than 4.5 inches from the wall on either side of the staircase.
Round handrails should be 1/4 to 2 inches in diameter, and handrails of other shapes should have an outer perimeter of no more than 4 inches in size. Large railings should include grooves to ensure safe exit and entry. Concrete structures should be tilted to ensure proper drainage, which can help prevent damage from frost or water. Structures must be properly supported and free from cracks, flaking or other signs of wear that may contribute to injury.
Construction conditions
An important step in the construction of concrete stairs is the use of proper formwork and correctly calculated flight of stairs. It is worth paying attention to the optimal size for concrete stairs and use solid wooden boards. Boards must be at least 2 cm thick to support the weight of the mix. The entire structure of the form must be supported by 4x4 messages. Wooden boards that create steps should be fastened with several screws to the side structure of the formwork.
The shape of the concrete structure on the second floor should be connected to the ceiling, if it is the second floor. It is recommended that the concrete ceiling and stairs be poured in one day in order to create a solid connection between the components. Use long screws and nails to secure the wooden formwork. Make sure that there are no gaps between the boards.
The stairs take at least 4 weeks to dry completely.
Advantages and disadvantages
There are many advantages to choosing precast concrete products for architectural and building products of all kinds. Reinforced concrete are durable, they are able to preserve the functionality and increase the long-term value of the property.
The main benefits include the following:
- able to withstand a fire, not flammable, therefore safe;
- low vibration and noise;
- low maintenance;
- high quality;
- durability of the mixture;
- year-round production and installation;
- economic efficiency;
- immediate secure access to the upper floors;
- the use of the mixture as an elastic, durable base allows the use of an attractive finish made of wood, stone, tile.
If we consider the shortcomings, it is worth highlighting the following:
- big weight;
- the need to attract heavy machinery during construction.
Kinds
A staircase is a set of steps leading from one floor of a building to another, usually inside. March spaces depend on the type of overlap, universal solution depends on the type of structure.You can use foreign projects for the central entrance.
The types of stairs used in building construction are generally based on form. There may be straight reinforced concrete, with a turn and continuous - it is a wide overlap. There are prefabricated screw or U-shaped structure. Can be used for the construction of concrete products or made of aerated concrete.
Straight
This type of staircase is used in conditions between two floors. It may consist of either one flight or more than one with a landing.
Swivel
Swivel structures are divided into the following:
- quarter turn;
- half turn;
- three quarters of a turn;
- bifurcated.
The quarter turn is one that changes its direction either to the right or to the left. It rotates 90 degrees when it rises to connect two different levels. It is also called the L-ladder. There are two types such as:
- The first variant has clearly visible positions at the beginning of the flight, as well as at the end. At the fourth turn, there may be a quarter landing;
- in a geometric staircase, the stringer and handrail are continuous.
In the case of turning halfway, the direction of movement changes by 180º. Such designs are quite common and are presented in the form of such three versions as:
- new racks at the beginning and at the end of each flight;
- has a space or well between the outer strings;
- The stringers and hand rails are continuous, without any intermediate racks.
The three-quarter direction changes three times, and the upper span intersects the lower one in the case of three-quarter-turn steps. A ladder of this type is usually used when the vertical distance between two floors is longer, and the length of the staircase is limited.
Bifurcated structures are usually used in public buildings, they have a wider flight, which forks, one turns to the left and the other to the right.
Continuous
This variety has a geometric shape, may be of the following types:
- round;
- spiral.
Prefabricated construction
Such floors are particularly suitable for the construction of high-speed staircases. High-quality finish provides a durable ladder for long service.They are ideal for the construction of high-quality private and residential buildings. Dense precast concrete has excellent acoustic properties associated with sound transmission problems.
Prepared concrete floors are the obvious choice for fire escapes. Maintenance and excellent durability are integral to the design. Precast concrete floors offer significant advantages during the construction phase of the project, providing quick installation and early safe access to subsequent floors.
Each prefabricated concrete flight of stairs is designed in accordance with regulations and is suitable for use.
Prefabricated floors can be designed as separate units or can be made as a complete prefabricated flight of stairs and an attached landing. Preparatory landings can be attached to the upper or lower part of the staircase, as well as provided with both upper and lower landings.
Details of the concrete structure provide a quick and safe connection between the stairs and the landing.Foot parts are designed for prefabricated structures, sitting on the flooring, prefabricated floor slabs or connections to intermediate prefabricated sites.
Payment
Whether it is site repair or its construction, it is necessary to make clear drawings, to make a high-quality project. The monolith is highly resistant to wear, you can make the steps of the standard type or start building a modernized structure. Each step consists of two main parts: the riser, which is the vertical part of the step, and the tread.
Other important terms you should be aware of when constructing a structure include such as:
- pitch line - it is an imaginary line that runs from the edge of the lower structure to the edge of the topmost step;
- construction step - this is the angle between the base of the structure and the pitch line;
- growth - this is the total height from the base to the top step;
- run - this is the depth that is measured from the front;
- stringers - these are lateral supports on either side of each step;
First stage
To begin with, it is necessary to find the total rise of the floor, measuring the total height from the planned base to a higher level or floor.Then measure the progress of the steps, setting the distance between the front and rear of the structure. Find the width of the overlap, measuring the distance between the extreme left and right borders of the planned steps.
Second phase
At the second stage, count the number of steps that will be needed. This can be done by setting the rise of the structure, the total height from the lower level to the upper level, and dividing this number by the height of the rise, that is, the height of each step.
The maximum lifting height can be 21 cm. If this number is displayed as a decimal, then it must be rounded to the next integer. If it is built in such a way that the uppermost protector is a step below the level of the floor on which you are building, then the number of protectors that you need will be 1 less than the number of risers. Otherwise, you need an equal number of steps and risers.
It is important to determine the dimensions of the height and depth of the tread. The depth of each tread, the upper surface of the step, is more flexible, but each of them must be at least 27.9 cm.To find the height of the risers, it is necessary to divide the total lift of the whole structure by the number of risers.
Steneni overlap form the angular side parts of the form on both sides of the overlap. To find the length of stringers, you need to multiply the total growth by the same value, then the total mileage - by its value. After that, you need to add an increase multiplied by itself, and mileage multiplied by itself, and then take the square root of this number. To find the angle of the stringers, you need to take the reverse sine (sin -1) growth, divided by the length of the stringers.
Third stage
The next step is to highlight the basis of the steps. Now that the general parameters of the step are known, it is necessary to divide the area where the steps will be installed. Measure from corner to corner to ensure that the layout is correctly inserted in the square, and the dimensions are correct. It is necessary to unearth the area where the steps will pour out. A spade should be used to dig holes 10.2–20.3 cm below ground level at the base of the slab.
Using dimensions, it is necessary to put together boards for lifting at every step and two boards for stringers (one for each side of the landing).
The ground-oriented side of the stringer forms should be cut to fit the height (angle) of the structure, and the upper part should be zigzagged. If concrete steps are poured out that form the correct angle (L-shape), then the stringer shapes should not be cut at an angle. It is worth using screws and a drill to attach each board. The space of the stringers should be approximately equal to the planned width of the structure.
Then you can lay the boards of crossbars along the zigzags of the stringer, which correspond to the upward rise of each step. The steps will lie on the subbase of the granulated filler, which will protect them from ground movement or wear. It will take 10.2–20.3 cm of filling.
Building codes
Building codes ensure the safety of the stairs in compliance with the rules that apply to the height and depth of each step, supports and handrails. During construction, standards must be taken seriously, as a small mistake can lead to serious injuries.
The International Building Code provides the rules of the step. A step that is different in height, width, or depth than the rest of the ladder can upset the person’s balance during use of the structure, causing a fall. Step building codes are based on the fact that people using overlaps expect each step to be the same height. Building codes provide safety.
Protectors support the weight of the user. The depth of all steps on the stairs should be the same in front and behind, with a maximum change of 0.375 inches between the deepest and shallowest steps. Protectors should be a minimum depth of 11 inches. Depth is measured from the front and rear edges of adjacent steps.
A step up is the distance from the top of one step to the top of the next, measured vertically. Risers should have a maximum dispersion of 0.375 inches between the highest and lowest risers on the stairs. They must have a maximum height of seven inches and a minimum height of four inches. Houses and townhouses have a maximum lifting height of 7.75 inches.
Structures must be at least 36 inches wide and have a minimum mark of 80 inches along the full stroke of the floor and one tread length per lower stage.Height is a vertical dimension from the front edge of the tread to the ceiling above. Each design requires landing with a length equal to the width of the overlapbut a landing length of more than 48 inches is required. Structures with a full vertical lift of more than 12 feet should have a landing between the upper and lower landings.
Production methods
Before the formwork will be filled, it is necessary to compare the sizes with those specified in the project. In identifying inaccuracies will have to recalculate the values. The steps must be carefully verified, otherwise the strength of the overlap is called into question. It is necessary to fill the interfloor transition with a monolith, since the transition will take part of the bearing load. Reinforcement is drilled into the wall - this is one of the reasons why it is so important to maintain the proper distance.
You can make the construction of the kosour. Material for formwork must be moisture resistant. Perfect fit plywood thickness of 2 centimeters. If the ladder is adjacent to the wall, a timber with a section of 8x8 centimeters is drilled, it is necessary for forming the angle of inclination.
You can fill the staircase with steps. The structure must withstand the weight of the concrete mix. The side parts and the bottom edge should be bonded without gaps. The assembly of the frame is carried out with the help of screws. The inner part is treated with oil or laid out with a film. Filling begins with the upper stage, one portion of the solution is a multiple of one stage. After 10 minutes, level the surface and lay the polyethylene. The side formwork is dismantled no earlier than after 21 days.
Lower shields are removed in a month.
Compound
Concrete floors that are cast in place require a lot of reinforcement, so when the stair system has a joint, it must support the load of the elements between them so that it is transferred to a reference point, such as a wall, beam or column. Walls, as a rule, are the elements that carry the main load for staircases.
If the building is surrounded by a concrete block or concrete walls, the floors can be maintained continuously on both sides with dowels or reinforcement laid into the walls. Autonomous systems are more structurally strong if cold joints are not created from one supported fit to another.
When a slab connection is required, it should include a third key depth of two thicknesses of the concrete surface and a depth of at least 1.5 inches with reinforcement dowels equal to the amount of reinforcement shown through the section. Additional dowels can be added if the depth and width is sufficient for their use.
Concrete slabs must have sufficient support under the formwork to support the mixture and reinforcement. A good safety factor must be taken into account, since concrete may accumulate on the ladder during pouring, which leads to a bearing weight exceeding the actual one.
Installation
Step-by-step instruction helps with his hands to make the construction of the ceiling. Assembly takes more than one day. Installation is faster if you bring assistants to work. If you do not plan to build a one-story building that is on the same level as the ground, then the overlap is vital for the tenants to move from one level of the floor to another, which is why the knot must be strong.
Concrete floors are especially popular because they are more durable than wood and are cheaper than installing metal stairs.With proper design, the concrete staircase is not only functional, but can also add aesthetic value to the overall design of the building. In order not to make a ladder consisting of uneven steps, you must first calculate the dimensions of each step based on the difference in floor height, the length of the overlap and the number of risers you would like to have.
After the differences between both floors are measured, it is necessary to divide the height value found by the number of risers that one would like to have on the stairs.
Then you need to determine the width. The usual rule of thumb is a budget for a girth that is at least 6 inches wider than the girth of a door. Although it is generally agreed that the wider it is, the more comfortable it is to walk. If you plan to create a landing, you should pay attention that the final landing should leave the house at 36 inches with a minimum width equivalent to the width of the door.
Creation of the frame
Now that you have a general idea of how the stairs will look, you need to prepare the foundation to prevent uneven steps. The general idea of ground preparation is simply to make sure that the land on which the ladder will be built is compact to prevent sinking during the pouring of cement.Just as it would be a bad idea to build a whole house on an uneven, loose surface, it is also dangerous to build a heavy concrete staircase on a bad foundation. The best way is to simply rent a mechanical seal.
Now you can begin to build wood panels, which are two panels made of wood. They will be the frame. It is very important that the panel of the finalized form is very durable, since it holds the shape of the cement structure as it is formed. First you need to make sure that the base of the skin is completely flat on the ground. Next, check for gaps between the base or the porch. If there are visible gaps, then you need to fill the holes. By the end of the fourth stage, it is necessary to have a sloping wooden paneling, which is perpendicular to the rest of the flat floor.
Reinforcement
Most see the importance of reinforcing a concrete structure with reinforcement, since floors are often viewed as simple, lightweight projects compared to the rest of the house.
Experts recommend spending time laying steel rods in a concrete base, which will extend the service life of the ceiling.
First, one should drill holes in the concrete foundation, and then block the reinforcement. Each hole should be about 4 inches deep and 8 inches apart from each other along the wall. Each riser should be cut and attached to the form panels with nails. It is recommended that each riser plate be manufactured in a size of 2x8 inches and have a height of approximately 7.5 inches.
Fixing the panels means using the structure to ensure that the concrete does not leak out and does not lose its shape before it completely hardens. The general rule for concrete is that it cannot be reused. After losing the form, it is no longer necessary. In the same way as the baking dish is greased, before pouring the dough mixture, it is necessary to lubricate the inner surface of the panel with oil or diesel fuel.
Fill
Concreting the floor will take less time if you order a ready-mix cement mortar. It is always better to do the filling work together, because cement is a rather complicated and heavy construction material. Alignment must be done until the cement has hardened, then nothing will help.
You can mix the solution yourself in a mixer, but this will take more time and effort.
The most important step in the casting process is to determine the ingredients that will make up the concrete and their proportions. EThere are many variables to consider, including the type of cement, the size and type of aggregate, the amount of water, and mineral and chemical impurities. Although a good mix composition can still lead to inadequate or poor quality concrete, if it is done incorrectly. Bad design will always give bad results.
To find the most economical composition should take into account several important points.
- Load Concrete can be made with a wide range of strength, so this is often the starting point. If the mixture will support only relatively small loads, you cannot use it to create an overlap. Concrete quality is determined by factors such as resistance to freezing or wear resistance.
- Performance The required workability depends primarily on how to place the concrete. It can be poured, pumped and even sprayed into place, and this will affect the performance that is needed.Other factors, such as the shape of the molds, the distance between the reinforcing bars, and the equipment available on site to consolidate fresh concrete after it has been placed, must also be taken into account. Efficiency is usually determined by the decline, which is a tendency for fresh concrete to spread under its own weight when placed on a flat surface.
- Environmental conditions. If the concrete is exposed to harsh conditions, this may well determine the quality needed, not the applied loads. In places with cold weather, it should be able to resist freezing.
- Surface wear. For some applications, physical exertion, as a rule, wears concrete, and does not destroy it. The wear resistance of the upper layer will determine how long the structure will last.
Ready mix
Most mixes are unloaded and mixed in one place, and then transported. As a result, the quality of concrete is high. Concrete mixers can be used to transport already-mixed concrete, or mixing can actually be carried out by a truck as it moves to the site.One of the potential drawbacks of finished concrete is that the time required to transport concrete to the site may take up most of the early period of good workability.
Mixing
Mixing concrete is a very important step to achieve good final properties, but it can be quite difficult without the right equipment. Therefore, many prefer to use ready-made concrete.
Mixing distributes the unit evenly throughout the cement paste, ensures that all the cement is completely saturated in water, and removes large air voids. In addition, mixing destroys agglomerated clusters of cement particles and allows air-entraining impurities to create the right system of air voids. Mixing leaves major shortcomings and, consequently, leads to lower strength, while excessive mixing of waste can destroy trapped air voids.
Accommodation
After the concrete has been properly mixed, it must be placed in the formwork, which determines its final position and shape.If the concrete needs to be reinforced, the reinforcement is laid in advance so that the mixture can flow around it.
If the mixer is located near the site, the mixture can be poured directly into the molds.
In cases where this is not possible, it is transported in buckets or a wheelbarrow. If this is impractical due to the required distance or size of the task, fresh concrete can be pumped through a system of pipes or hoses into place with special concrete pumps.
For the mixture to be pumped, there are more stringent requirements for workability. If it is too dry, it will not pump well, and if it is too wet, it will tend to separation. Segregation can also occur if concrete enters the formwork too quickly, as larger aggregate particles tend downward.
Consolidation
After the concrete has been poured, it is necessary to remove large air voids and make sure that the mixture is poured into all corners of the formwork. This process is also called compaction. Excessive compaction can lead to segregation, but lower concentrations result in less optimal properties.The two most common methods of consolidation are compaction rollers and vibrations. Roller compaction is a simpler and more economical method that is suitable for very large structures.
Vibration compaction is a mechanical process that transmits shear energy pulses into concrete, usually with a probe that is inserted several inches. Each pulse of shear energy instantly dilutes the mixture, allowing it to flow very freely. This is the standard consolidation method for general construction projects, with the exception of roads. The shear energy will only pass through a limited thickness, so when thick overlaps are placed, the fresh composition is poured into layers.
Each layer is compacted before the next one is poured onto it. Vibration is a noisy and time-consuming step, requiring expensive and specialized equipment. For this reason, the use of self-configured concrete, which flows so freely (with the help of chemical impurities), is growing, that mechanical consolidation is not needed.
Finishing work
For concrete floors and coatings, appearance is particularly important.smoothness and durability of the surface. Finishing refers to any final compaction treatment to achieve the desired properties. Grouting is the process of compacting and smoothing the surface, which is performed when the concrete begins to harden. This is a standard procedure for stairs.
After the grout has hardened, the mechanical finish can be used to roughen the surface to make it less slippery or to polish the surface as a decorative step to bring out the beauty of special aggregate such as marble chips.
The newly developed process, which is growing in popularity, involves the use of concrete dyes and surface forms to simulate the appearance of bricks. When the solution hardens and gains strength, it becomes less and less vulnerable, so the critical period is the first hours and days after filling out the forms. Proper curing usually comes down to two factors: you need to keep it moist and cover with film.
Hydration
Cement hydration, as the word suggests, involves reaction with water. In order to properly lay the mortar, the cement paste must be completely saturated with water.If the level of relative humidity inside falls to 90%, the hydration reaction will slow down and 80% stop completely. This not only prevents the solution from getting full strength, but also creates internal stresses that can cause cracking.
To preserve the surface, it can be covered with a plastic or damp cloth, because it will prevent evaporation, or periodically spray water.
Spraying is especially useful when the density is low, because the initial water for the mixture is not enough to completely wet the cement. The extra fluid will not penetrate the thick structure, but it will help create a stronger surface layer.
Usually there is a desire to remove the formwork as quickly as possible in order to continue the construction process. However, if it is done too early, the structure will deform under its own weight. This will lead to loss of size, cracking or even collapse. Similar problems arise if the loads affect the surface of the floor or slab too soon.
Weather plays an important role in the curing process. Hot windy weather leads to rapid evaporation, so special attention should be paid to ensure that the solution content is wet. Cold weather makes the mixture harden much slower. This delays the construction process, but ultimately leads to better quality, as hydration products develop differently at different temperatures.
In the form of the mixture is poured shovel, wheelbarrow or funnel. It is important that no voids form. The spatula helps to level the surface, you can use a long board. It is important to press the surface so that the water comes out. For this you should use a special construction tool that will speed up the process.
Only after complete drying of the mixture can the surface be treated.
To improve the grip is to clean the surface. You need to take a stiff brush and walk it on the surface of the concrete to create thin grooves on the surface. Smooth concrete can be very slippery, which can be especially dangerous.
There are several finishing methods that can be used to achieve a smooth surface. You can install a screed plate and use it on the front and rear side by side to drag excess mixture from the tread. Or you can use a wooden float to get a flat surface.
Finish
When entering or modeling overlap, we must not forget about the railing. They can be ennobled, made attractive and the main decoration of the ceiling. They are required to perform the main function - security. They provide a handle to keep from falling, and also serve as an attractive accent. The railing must be of a certain height. Most of the requirements regulate the height from 34 to 38 inches. They should also be able to support a certain weight against them at any angle (about 200 pounds).
There are also rules regarding the dimensions of the railing and the distance from the wall or any other structure.
The purpose of the rules is to ensure sufficient grip during ascent or descent. Finally, balusters (vertical pillars that rise along the open side of the floor) should be located close enough to each other to prevent an accident with a small child.Typically, this distance is 4 to 5 inches apart.
Although safety is the primary concern of hand guards, they should not look dull and utilitarian. Many designers have created railings that range from the ultra-modern to the rustic fancy style. Railings must be combined with the architectural style of the house. They can be made from a variety of different materials. Most people prefer wood, but wrought iron and other metals are also popular. Some choose beautiful metal elements with glass balusters for a sleek, modern look.
Wood railing today are the most common, they are not boring. The tree can be turned on a lathe and turned into various shapes and profiles. Whether it’s a classic Victorian look, a rustic look, or clean, modern lines, you can paint or paint it to fit any interior.
Metallic railings usually have a classic, decent look. Since metal is easy to shape, it is a popular choice for those who want a special design,for example, vines or even a musical motif (think of railings that look like notes). Metal is also a common choice for spiral or spiral staircases. Metal and glass railings are ideal for embodying the modern look.
Large sheets of thick glass, brushed with aluminum handrails, represent modern design and new directions.
How to make a monolithic staircase with your own hands, see the following video.