Modern sound insulation materials for houses and apartments
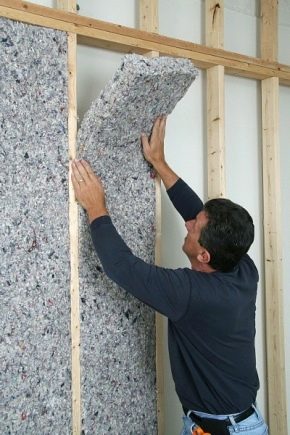
Constant noise is an obligatory companion of residents of large cities. Some people get used to knocking doors, footsteps and working televisions outside the bedroom wall, but most citizens try to protect themselves from too aggressive acoustics by installing sound insulation in apartments. Modern soundproofing materials for homes and apartments can counteract almost all types of noise: air, shock and structural.
Special features
Discomfort to a person is brought not by the presence of noise as such, but by the excess of permissible values of sound power.With a noise of 25-30 dB, the human body feels most comfortable, as sound stimuli increase, the attitude to noise changes to a tolerable one, which remains until a power of 60 dB is reached. When this index is exceeded, noise becomes an aggressive irritating factor that can significantly affect the state of mind.
In modern cities, noise can have a different nature:
- Airborne noise includes dogs barking, voices, medium and high frequencies of music, noise of cars, etc.
- Impact noise includes the low frequencies of music (subwoofer), the sounds of furniture rearrangement, indoor walking, punching and other construction tools.
- Structural noise is the mix of the above-mentioned noises, which is the transmission of vibrations from all types of sound effects through the construction of buildings.
- Acoustic noise occurs in half-empty rooms, this is all the usual echo.
Accordingly, to protect against each type of noise, sound insulation materials with certain physical characteristics are required: sound absorption and sound insulation.
One of the most important is the sound absorption coefficient, which is determined on the basis of acoustic tests conducted for each building material.The maximum is 100% sound absorption, which is characterized by a coefficient value equal to 1. This indicator is directly related to the degree of density and allows you to select the following categories:
- Solid materials, which include granulated or suspended mineral wool, as well as vermiculite, perlite or pumice. These materials have an average absorption coefficient of 0.5 and a fairly high bulk density of about 400 kg / m3.
- Semi-rigid: slabs made of mineral or fiberglass wool, as well as materials having a cellular structure, such as polyurethane foam, etc. from the variety.
- Felt felt, fiberglass and mineral wool, not pressed in the form of plates, are considered soft. They have a high absorption coefficient - 0.7-0.95 with a bulk density in the range of 70 kg / m3.
In order to successfully deal with noise, it is necessary to take into account such an indicator as the material sound insulation index. It is measured in the same magnitude as noise - in decibels (dB) and calculated for each type of building materials: concrete, plasterboard, brick, foam blocks, mineral wool, etc.Monolithic floor slab, which has a thickness of not less than 200 mm, has a sound insulation index of 74 dB. For a new brick wall with a thickness of half a brick (150 mm), the maximum is an index of 47 dB, which decreases with time due to the appearance of cracks and cracks.
To prevent the audibility of human speech, the wall must have a sound insulation index of at least 50 dB. Accordingly, thin walls in prefabricated houses that are not satisfactory in terms of this indicator should be further strengthened.
This can be done in several ways:
- to erect in addition dense and massive walls or floors, for example, from foam blocks, while observing maximum tightness;
- create a multi-layer construction of several soundproofing materials, alternating soft and hard types for maximum suppression of all types of noise and observing the rules of tightness;
- use ready-made soundproofing panels made of materials of different density and structure and designed for a wide frequency range of sound waves.
Due to the fact that the arrangement of powerful walls / partitions made of brick or concrete requires a corresponding thickness of the foundation,These indicators should be included in the architectural calculations at the stage of drawing up construction and design documentation.
In those cases when it is necessary to reinforce the sound-proofing qualities of an already built wall or to erect noise-insulating partitions in an apartment, either ready-made soundproofing panels are used, or prefabricated structures of various modern materials are mounted directly on the spot.
Species
Modern varieties of materials for sound insulation made to consider in terms of resistance to one or another type of noise.
Materials that successfully withstand shock noise are called sound-repellent, because they do not absorb, but repulse sound waves. Most often, such materials are used in the construction of "floating floors" as a substrate.
Modern industry provides a huge selection of insulation substrates:
- Staple fiberglass. The material belongs to the class of durable, has a high index of reducing the level of impact noise - 42 dB, not combustible. This category includes such material as "Shumostop - C2".
- The membrane is polymeric bitumen. The base is a sound-insulating layer of non-woven polyethylene, on the surface of which is coated with bitumen with plasticizers-polymers, reinforced with fiberglass. The material is resistant to decomposition and rotting, vapor-permeable, has an index of reduction of impact noise at 26-39 dB (depending on thickness). Flammability group - G2. A prime example is the FonoStop Duo and Izolonape.
- Fiberglass canvas with one-sided bitumen impregnation. Designed for long life, waterproof and fire resistant material. Noise reduction index - within 23-29 dB. This variety includes fiberglass brand "Shumanet", as well as "Isofon-super."
- Extruded polystyrene foam. This is a durable material (designed for 50 years), which has a noise reduction index of 25 dB, is characterized by low water absorption and high resistance to compression, a minus can be called a high fire risk index - G1. These are such brands as "Fomboard", "Penoplex", plates "TISplex", etc.
- Composite. This material consists of three layers: polystyrene foam granules are located between the layers of polyethylene or aluminum film.A feature of the composite is that the lower film has the ability to pass moisture into the internal space, from where it is removed along the expansion seams. Thus, the space is ventilated. The service life is 20 years, the noise reduction index is in the range of 18-20 dB, the material is not combustible. These are such brands as Tuplex, ThermoZvukoIzol, Vibrofilter.
- Probkoreziny substrate. These are mats of rubber granulate and cork. The material has an average fire safety (combustion class B2), however, it can contribute to the appearance of mold in structures, and therefore requires additional waterproofing. The noise reduction index is from 18 to 21 dB. These are such materials as UZIN RR 188, "Utsin PP 188", Ibola.
- Cork underlay. The material, which is produced from pressed cork crumb, is not subject to rotting and fungus, the service life reaches 40 years. Allows you to reduce the impact noise by 12 dB. An example would be Cork Roll roll material, Corksribas plates, Ipocork, etc.
- Foam polyester. The material of synthetic fiber impregnated with reinforcing fiberglass on both sides has a high vapor permeability, allowing the surfaces to "breathe", the sound insulation index is 8-10 dB. Flammable (class G2).
- PE foam (polyethylene foam). There are unstitched foam, having the smallest sound insulation effect; physically crosslinked and chemically crosslinked, the sound insulation quality of the last variety is the highest. The material has a high flammability class - G2, is destroyed when exposed to ultraviolet radiation, sags under prolonged loads, is unstable to mold. Sound insulation index ranges from 12 to 15 dB. These are such brands as "Isopenol", "Plenex", "Izolon" and many others.
- Tecsound. Thin synthetic material on an elastic polymer base, used to isolate two types of noise: air and vibration (shock). It is self-extinguishing and moisture-proof material, has a sound insulation index in the range of 25-30 dB. Effective in suppressing noise from a metal roof.
We should also consider the materials that suppress the impact noise and are used for the installation of acoustic ceilings:
- Perforated sound absorbing Knauf plates. This is a material based on drywall, on the one hand having a substrate made of synthetic fabric with holes-resonators. Thickness is 8.5 mm, fire hazard class - NG.As shown by the test tests, these plates are designed to repay low-frequency waves.
- Plate "Ecophon", representing a "sandwich" of high-strength fiberglass, additionally reinforced with a mesh of textiles. Available in thicknesses from 15 to 40 mm, not flammable.
In the case when the subject of concern is primarily airborne noise, it is worthwhile to identify the cracks and cracks in the construction of walls and their elimination. If, having provided the greatest possible tightness of the existing wall, it is not possible to achieve the desired effect, it is necessary to create additional sound insulation.
This should be a frame construction in which rigid and semi-rigid building materials are mounted. The main sound impact while taking on materials with sound absorption function.
Modern noise absorbing materials:
- Mineral (basalt) wool. This material is the result of the melting of rocks of the basalt group, metallurgical slags, as well as their mixtures. Available in the form of plates (mats). Having a fibrous structure and a small fiber length (15 mm), the mineral wool provides a high absorption coefficient of sound waves - from 0, 87 to 0, 95; has good vapor permeability and is non-flammable,inert and biologically passive building materials. The most popular brands are: Rockwool Acoustic Butts, Schumanet, Izolight, Bazaltin, Termozvukoizol.
- Glass wool. Fiberglass-based material (average fiber size is 50 mm), having a sound absorption coefficient of 0.85 to 1 (for an acoustic Knauf "Insulation" partition, which is distinguished by a special combination of fiber length). Available in the form of plates, non-flammable, vapor-permeable, biologically and chemically inert. Compared with mineral wool, glass wool is lighter. In the Russian Federation, such species as Knauf Insulation, Ursa Pureone 34 PN, Isover, etc. are presented.
- ZIPP (soundproof sandwich panels). These are frameless systems that can be purchased off-the-shelf, effective against all types of noise. The composition is usually the same: GVL + fiberglass (mineral wool) + attachment points to the wall. These systems have a high noise insulation index, which largely depends on the thickness of the structure (IPPCs can be from 40 to 130 mm in size). When using a 70 mm thick panel, this is 10 db. At the same time, the panel has a high sound absorption coefficient due to the presence of mineral wool or glass wool inside.The disadvantage can be called a significant weight, requiring partitions with high bearing capacity.
The next kind of soundproofing materials are those that “work” against the propagation of structural noise. They are gaskets or compositions used in the process of installation of adjacent structures: ZIPP systems, wooden or “floating floors”, frame partitions and facings. Among them:
- Fiberglass It is made from superthin fiber in the form of strip pads of various widths. It has a high index of reducing the spread of impact noise - 29 dB. An example is such a material as "Vibrostek M" or "Vibrostek V300", as well as piercing mats made of fiberglass "MTP-AS-30/50".
- Vibroacoustic sealant. Most often it has a silicone base, it can be either non-hardening or hardening. It has excellent adhesion to all types of building materials, when filling the seams reduces the spread of structural noise. The following brands are most familiar to the domestic buyer: Green Glue, Vibrosil, Bostic 3070, Silomer, and also vibration-absorbing mastic.
- Self-adhesive elastomeric gaskets for doors and windows. They are produced from porous rubber, microporous polyurethane, etc. in the form of plates or tapes, are installed between the structural elements and around the perimeter of the openings to reduce vibration, have an index of noise reduction within 23 dB. As an example, such brands as Varnamo, ArmaSound. Recently, such materials have been actively producing and Russian enterprises, for example, LLC Obninsgazpolimer.
- Silica fiber. This material is the most fireproof, while having a high noise insulation index - 27 dB. Available in mats and rolls. The most popular brands are: Vibrosil-K, Supersil, Ekowoo.
Scope of application
The properties of noise insulation materials have the widest range of applications. Most of them are used not only for their intended purpose, but at the same time as insulation. This mainly applies to all types of mineral wool, glass wool, fiberglass, polystyrene foam, sandwich panels and cork substrates.
It is up to the professional to decide how to use this or that soundproof material to make it work as fully as possible.which is able to correctly assess the acoustic features and problems of a particular room. It may be necessary to create a sound-absorbing flooring in the room to avoid conflicts with neighbors from the bottom, or to completely isolate the walls when equipping a home theater. It may be necessary to protect the bedroom from the noise coming from the street.
Therefore, it is recommended to seek advice from a construction and repair company dealing with sound insulation on a professional level, because it is easier to pay for the services of a competent expert assessment than to invest funds in repair without having confidence in the final result.
The greatest effect can be obtained by integrating this or that material into building structures directly in the process of erection of buildings, the construction of floors, walls and partitions:
- when laying slabs of mineral wool in the cavity of partitions;
- by installing plates or strip pads between elements of building structures to absorb structural noise;
- when installing sound-insulating panels on the surface of walls with their subsequent plastering;
- in the construction of "floating floors", at the base of which is soundproof material, followed by the installation of reinforced cement-sand screed.
To improve sound insulation in already constructed premises, the following methods are used:
- Creation of a sound-proof layer on the surface of interfloor overlappings by placing mats of mineral wool (glass wool), covered with either a cement or composite screed.
- Installation of soundproofing frame structures, which represent the alternation of gypsum plasterboards, mineral wool or glass wool slabs, as well as a superdiffusion membrane (if necessary), a damper tape and vibro-acoustic sealant.
- Placement on the walls of soundproof sandwich panels. These are frameless systems that are sold in finished form. They usually consist of sheets GVL, between which there is fiberglass (mineral wool) and built-in units for attachment to the bearing walls. The sealing of the structure is carried out by means of damping gaskets and sealant.
- Arrangement of "acoustic ceilings", which are mounted on a frame of galvanized metal profile.The design consists of sheets of drywall and slabs of mineral wool and is fixed on vibration-proof suspensions. Gaskets are used for sealing in combination with vibration sealing. It is also worth considering the possibility of installing stretch ceilings with a sound insulating effect.
- Installation of the “ventilated facade”, which is carried out on the outer wall of the building and also performs a heat-saving function.
How to choose?
It is necessary to approach rationally the choice of any building material. This fully applies to noise-absorbing materials, the properties of which should correspond to the tasks that need to be solved. At the same time, it is desirable that the cost of the work does not “strain” the owner’s purse unnecessarily.
Being engaged in arrangement of sound insulation, you should either trust the time-tested (and reviews of friends) repair company, either study the issue yourself or following the recommendations of sales assistants. You can save in each of these options.
Advantages of applying to the construction and repair company:
- assessment of the problem and ways to eliminate it is carried out by a specialist repairman (foreman), who recommends certain soundproof materials;
- serious repair companies give a guarantee for the work done (usually 3 years), therefore they offer materials and technologies of which they are sure;
- when contacting the company at a time of the year that is not considered to be the construction season (late autumn, winter, early spring), the customer is offered a discount on the cost of work;
- large firms usually have proven suppliers who often sell materials to customers at a discount.
Advantages of self-selection of materials and work:
- in the process of studying the issue, useful knowledge is acquired that may be useful in the future;
- the buyer saves a significant amount on the payment of workers;
- You can spend the savings on the use of more expensive sound insulation materials.
Analyzing the problem of noise on your own, it is worth finding out what its nature is and whether the noise is airborne or shock.
These types of noise can be eliminated in almost any room and at any stage of repair / construction, in contrast to structural noise, which is required to be insulated at the stage of building construction.
Most often in the premises there are noises of both types. For example, in the apartment downstairs there is an office, whose visitors constantly slam doors and talk. In this case, we can talk about the combination of all three types of noise, which can be extinguished using sound insulation of the floor, including the use of two types of material - noise absorbing and noise-repellent, with the mandatory use of damper pads, which can partially suppress structural noise. This involves the installation of acoustic "floating floors", having at the base of not less than 100 mm a layer of mineral wool and a mandatory powerful screed on the surface.
Sound insulation of "cardboard" walls is usually required to protect against airborne noise. This issue is solved through the use of frame or frameless systems of gypsum plasterboards and mineral wool, the thickness of which is the greater, the more disturbing the residents sounds. In the case when music is heard from behind the walls, there must be added an anti-repellent material, such as extruded polystyrene foam or staple fiberglass.
You can also enhance the effect by increasing the GCR layers.In the case of the use of prefabricated IPPs, it is necessary to select a brand with high noise-repellent characteristics. Such structures have significant weight, so you need to make sure in advance that the walls are able to withstand a similar load.
For a wooden house, materials are used that have the lowest flammability class (NG), resisting the appearance of mold and fungus, resistant to rodent attacks and, of course, vapor-permeable.
How to do it yourself?
It should be understood that in itself the acquisition of even the best sound insulation materials will not provide silence in the room, if the technology of their installation is violated. To achieve this goal, you need the correct installation, which can provide professionals-acoustics. In the case when, for any reason, it is impossible to contact a construction company, you should carefully study the recommendations in order to carry out the work on sound insulation with your own hands. The use of improvised means as an insulating material, most likely, will not give the desired result.
For the proper installation of soundproofing cladding need exactly those materials that are provided by technology.
Necessary materials:
- guiding and post galvanized profile, which can be replaced by wooden bars;
- suspensions (preferably using vibrating hangers);
- self-tapping screws, which, for better sound insulation of structural noise, should be equipped with rubber washers;
- damping gaskets in the form of a tape;
- vibroacoustic sealant;
- sheets GKL or GVL thickness of 12.5 mm;
- fiber plates: mineral wool, glass wool, having a thickness of 50mm.
Sound insulation of walls "on the ground" will take from 50 to 120 mm of free space, which will have to sacrifice in order to obtain acoustic comfort.
The sequence of execution of work on the installation of structures soundproofing frame-sheath partitions:
- Installing the gasket (damper) tape with a minimum thickness of 4 mm along the contour of the mounted partitions. Gaskets are glued to the walls, floor and ceiling with a sealant.
- Installation of the frame is carried out on the level, guide profiles are set at a distance of not less than 10 mm from the surface of the insulated walls.
- Rack-mount profiles are mounted with a pitch of 600 mm, their length should be less than the height of the room by 10 mm.
- Vertical pillars designed for the doorway,it is necessary to strengthen by means of the locking connection of two elements of the rack profile; It is possible to use wooden bars for this purpose.
- The internal space in the rack profiles is filled with mineral wool or glass wool plates, and the plates should be inserted as tightly as possible to avoid gaps.
- The frame is sheathed with sheets of plasterboard with a pitch of 500 mm. In the case when 2 or 3 layers of skin are being mounted, it is recommended to choose a GVL-sheet that is more resistant to loads for the primary layer. Finishing facing is mounted with a step of 200-250 mm.
- A technological gap is left between the cladding sheets and the ceiling / floor, which is filled with vibro-sealant.
- Excess damper tape is trimmed flush with the finishing layer of sheets HL.
- When mounting the door, the joints between the frame and the door frame are filled with sealant; on the surface of the box at the points of contact with the door leaf it is necessary to install sealing tape.
The implementation of sound insulation of the ceiling requires a sufficient height in the room, because the design takes about 120 mm from the height of the room. Stages of work:
- A damper tape is glued to the surface of the walls adjacent to the ceiling.
- A dowel-nails guide profile is temporarily fixed along the perimeter of the walls.
- Vibration isolators are attached to the ceiling surface, the pitch is 800-900 mm. From the wall to the first suspension should be no more than 150 mm.
- The suspensions are fixed bearing profiles of the frame, the distance between which should not exceed 600 mm.
- On the profiles of the first level are mounted minor profiles that ensure the presence of an air gap between the floor slabs and the insulating material.
- Removed dowel-nails, holding the guide profile (this is done to avoid the appearance of noise bridges).
- Sound absorbing plates are installed in the frame.
- The first layer of ceiling lining is carried out, with GVL sheets with a thickness of 10 mm being applied.
- The seams between the sheets are filled with vibro-acoustic sealant.
- Set the second layer of plating with the use of gypsum board, which is mounted with the run-up of the joints.
- Excess damping tape is cut with a construction knife, the seams are filled with sealant.
When installing floor sound insulation several different technologies can be applied depending on the materials used. The most popular technologies of the floating floors Rockwool and methods of the company Acoustics Group, based on the use of plates Shumostop.
Soundproofing floor (on the system "Shumostop"):
- The surface of the floor slabs is being prepared: irregularities are smoothed, construction debris is removed, adjacent communications are isolated using elastic pads or tape.
- Along the perimeter of the walls is laid slab soundproof material brand "Shumostop" to prevent the alignment of the screed with walling. The height of the edge should slightly exceed the thickness of the screed. It is acceptable to use a damper tape to minimize the thickness of the seam between the tie and the wall.
- A layer of more dense material is laid out along the perimeter of the room - this is “Shumostop K2”.
- The floor surface is covered with the main working material - “Shumostop C2”. Laying is made as tight as possible, without gaps and gaps.
- The surface is covered with a reinforced plastic film, lifted also along the wall to the height of the edge. Joints are combined overlap and taped.
- The film is laid on a solution of a sand mixture of a grade not lower than M-300, which is then reinforced with a reinforcing mesh (mesh fragments are necessarily fixed together).
- A concrete mortar is poured over the mesh, which is leveled using a plastering rule.
- After the screed gains strength (on average, it takes 28 days to dry), the edge layer of the film and the damper strip are cut to the level of the screed.
- The seam formed between the wall and the coupler is filled with vibro-acoustic sealant.
Tips and tricks
To date, there is no doubt about the effectiveness of the activities for sound insulation of premises. However, this statement applies only to those works that are performed in full compliance with the technology recommended by manufacturers of noise insulation materials that have long been present in the construction market of our country and have been tested by practice.
There are a lot of enthusiastic clips on the Web about super-wonderful new developments that do not require space in the room and eliminate annoying noise. Construction forums that are devoted to discussing sound insulation problems very often serve as advertising sites for this kind of new products, so it is easy for a layperson to get lost in a variety of terms.
It makes no sense to take a word for such statements, it is all the more unwise to test fashionable innovations on your own experience,since the cost of such sound insulation materials is usually quite high.
A brief overview of time-tested tips and tricks:
- If the dimensions of the room allow, it is better to apply the frame soundproofing system as having the most positive feedback.
- In the case when frame-sheath partitions are constructed in a room, you can also worry about sound-proofing equipment in advance: in this case, mineral wool boards are mounted inside the partition and do not occupy additional space.
- In cases where it is required to save as much space or height of the room, it is worth using ultra-thin materials from proven manufacturers, for example, Rockwoll Acoustic Butt Ultra-thin or ultra-thin ZIPPS sandwich panels.
- During the work, it is necessary to achieve maximum tightness of structures, which will prevent both the appearance of sound bridges and the ingress of tiny dust particles of mineral wool or fiberglass to the respiratory organs.
- For fixing vibro-hangers to the ceiling, it is desirable to use a special type of fastener - a wedge anchor with a plastic nozzle.
- When connecting communications, they must be tied up with sealing tape in order to avoid the preservation of the so-called “sound bridges”.
- In wooden buildings it is not recommended to erect soundproof walls earlier than one year after the construction of the building. This is due to the process of primary shrinkage at home, during which it is impractical to carry out work.
When purchasing materials through online stores you should not start from the rating, it is better to compare the characteristics given in the tables that are present on the pages of all large trading platforms.
On the modern sound insulation of the walls in the apartment with their own hands, see the following video.