Sound insulation Rockwool "Acoustic Butts": application
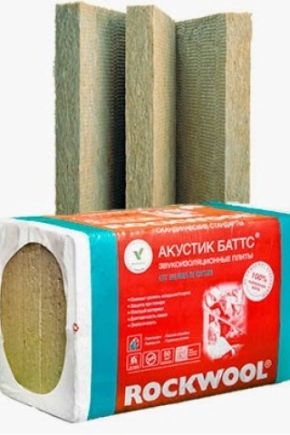
A modern comfortable apartment is unthinkable without good sound insulation, since in a big city conditions a huge number of sound stimuli are piling on residents.
Such material as Rockwool "Acoustic Butts", which has a widespread use in construction, helps to achieve the maximum sound insulation effect with minimal material costs.
What it is?
Basalt insulation Rockwool "Acoustic Butts" is a product of processing of stone rocks, namely the varieties of rocks of the basalt group. To be more precise, it is a product of remelting, since the temperature in the smelting furnace reaches + 1500 ° C, which makes basalt look like volcanic lava. The hot stream is sent to a centrifuge, where it cools with constant rotation and blowing, turning into individual fibers, which are then transported for processing with binder compositions and impregnations that enhance the water-repellent and refractory qualities of the material. A carpet of necessary density and thickness is formed from individual fibers.
Since stacking is performed by the pendulum method in a chaotic manner, a large number of superimposed fibers provide absorption of propagating sound waves, which explains the excellent noise-suppressing properties of this material.
Passing between the layers of fibers, external noise is repeatedly reflected and attenuated, ensuring silence inside the room. The technological process is completed in the heat treatment chamber, where sintering of bonding impregnations takes place, which ensures the durability of the insulation. After cooling, a single carpet is cut into individual plates and packed in plastic film.
Specifications
All Rockwool Acoustic Butts slabs have good noise absorption, strength and hydrophobic properties, thanks to which this material has become a leader in this segment of the domestic construction market. Today, there are plates on the market, the size of which can be 1000x600x27 mm (ultrathin), 1000x600x50 mm and 1000x600x100 mm.
Rockwool Acoustic Butts and Rockwool Acoustic Butts PRO plates have the following characteristics:
- The noise absorption index depends on the type of plate: for Rockwool Acoustic Butts PRO, it corresponds to class A (1 is the absolute level of noise reduction), and for Rockwool Acoustic Butts it is class C (0.7 is partial noise reduction), especially effective medium and high frequency sounds are absorbed;
- density is 37 kg / m³, 45 kg / m³, 60 kg / m³;
- weight varies from 125 kg to 150 kg per 1 cubic meter;
- thermal conductivity has a coefficient λ10 = 0.034 W / (mK), which is a rather low value;
- water absorption during short-term immersion is not more than 1.0 kg / m²;
- vapor permeability coefficient - 0.3 mg / mch · Pa, which is low and allows using this material on wooden structures;
- flammability group - NG (the material is not subject to burning and can be used when heating surfaces to + 750 ° C);
- ecological compatibility is confirmed by the EcoMaterialGreen sign;
- chemical resistance corresponds to the class of inert materials;
- biostability completely excludes material damage by fungus, mold and rodents;
- resistance to compression and deformation ensures no shrinkage during the entire period of operation.
Advantages and disadvantages
When evaluating the pros and cons of various Rockwool Acoustic Butts slabs, it is worth starting from user reviews, since this material has been used in construction for quite some time. The manufacturer notes that when creating a “working” sound insulation, it is not enough just to use basalt fiber mats. Sound insulation is the arrangement of a system for fixing noise absorbing material that meets certain technological requirements.
In the case when the technology is violated, the user remains dissatisfied with the work done, notes a weak effect and usually believes that the reason is the poor quality of the insulating material.
Those of the consumers who equipped the similar soundproofing system and successfully use it, The following advantages of using Rockwool Acoustic Butts are noted:
- pleasant cost in comparison with similar materials;
- small weight, convenience when transporting;
- convenience in work: the material is elastic and not as frayed as other varieties of mineral wool, allowing you to perform work quickly and cleanly;
- the material does not impose any special requirements on the surface on which it is mounted;
- when arranging home theaters, they note this effect: indoors, the sound does not “press on the ears”, since it does not reflect from the walls and ceiling, which is partially absorbed by the material of the plates;
- when using basalt fiber to insulate the walls in the room there is no background noise;
- The main advantage is the preservation of good sound insulation characteristics even with a small thickness of insulation. This applies especially to the newest varieties, called ultrathin and having a thickness of 27 mm;
- the material "breathes" in contrast to synthetic analogues, therefore it is suitable for wood construction;
- biostability and incombustibility;
- at the same time with the soundproofing effect, this material is also a heater.
By cons include a few points.
- Installation of Rockwool plates, as well as other soundproofing options, leads to the loss of free space inside the room. Partly help in this can use the ultra-thin variety Rockwool "Acoustic Butts."
- Builders-practitioners do not recommend the use of fiber plates for sound insulation of floors, as the material is compacted with time from walking and other loads, which leads to a loss of sound-absorbing effect and the appearance of floor subsidence. However, the manufacturer notes that this defect is due to non-observance of technology and when conducting sound insulation of floors and the device “floating floors” recommends the application of cement-sand reinforced screed over insulating plates or team screed at least two layers of sheet material.
- The material requires the most hermetic coating with sheets of gypsum boards and the treatment of seams with non-drying sealant.
How to choose?
When protecting against unwanted sounds, it is worthwhile to take a comprehensive approach to choosing a specific variety of Rockwoll slabs for acoustic insulation, reasonably evaluating the requirements for noise absorption and the cost of the material.
- For the private sector, where maximum protection against external noise is not required, the manufacturer offers Rockwool Acoustic Light Butts. It has the lowest density from the entire Rockwool Acoustics family, which is 37 kg / m³ and good compression performance, providing flexibility and quick installation.
- The best choice for an apartment building is Rockwool Acoustical Butts, which, with a thickness of 100 mm or 2x50 mm, provides optimum sound insulation performance.
- For rooms in which work is required to be carried out with maximum preservation of the internal space, for example, in kitchens of panel houses measuring 6 square meters. m, used Rockwool "Acoustic Ultrathin", perfectly coping with the absorption of noise at high frequencies (dogs barking, music, and others).
- Rockwool "Acoustical Butts PRO", having the highest density and cost, is intended for arranging cinema halls, public premises and other places that cause additional low-frequency noise.
How to install?
Rockwool experts recommend not to violate the installation technology, otherwise the effect of effective sound insulation will not be achieved.
For installation, you will need the following elements of the mounting system:
- vertical and horizontal guides: galvanized steel profile or wooden bars for use as frame racks;
- direct suspensions;
- screws, preferably with a rubber washer;
- Rockwool damping (sealing) tape;
- silicone sealant (vibroacoustic);
- GCR sheets, which are selected in accordance with the manufacturer's recommendations. The thickness is usually 12.5 mm;
- fiber plates Rockwool "Acoustic".
The installation scheme is quite simple: for laying soundproofing plates, it is necessary to mount a frame in which the plates will be laid later.
The sequence of works for partitions and ceilings is the same and includes the following actions:
- a sealing tape is fastened to the walls and ceiling, which is necessary to reduce the transmission of acoustic vibration through the surface;
- Rack constructions are installed on top of the tape, a step of 600 mm is observed - this is the width of the plate that must be maintained for fixing the plates;
- Rockwool "Acoustics" plates are installed in the formed cavities, while it is important to place them as tightly as possible, in other words - fit.In order not to damage the material, first one side of the slab is installed in the frame, and then the second edge is carefully tucked into the batten;
- depending on the thickness of the plates used (27, 30, 50 mm), they can be installed in several layers;
- sheets of gypsum boards are mounted, while they are mounted with a pitch of 150 mm. In the case when 2 layers of gypsum boards are mounted, the seams should be offset relative to each other;
- slots and joints between sheets GCR (GVL) are treated with sealant.
Laying soundproof floors has important technical differences.
The layer of Rockwool Acoustic plate should be at least 100 mm thick.
To ensure a long service life, sand-cement reinforced screed is poured over sound-insulating slabs as follows:
- the ceiling plate is covered with insulating material Rckwool "Acoustics";
- a layer of Rckwool Flor Butts slabs;
- Rckwool vapor-damp insulation layer is laid;
- fittings fit;
- poured cement mortar.
Massive team screed can be installed as follows:
- soundproofing is laid on the floor slabs;
- Nesting is done with Rockwool Flore Butts;
- a combined plywood or OSB screed is made, which is done in a “sticky” manner.
This technology allows laying a laminate floor over acoustic “floating floors”, without fear of cracking.
Analogs
In the construction market there are materials that have the same range of applications as the Rockwool Acoustic Butts sound-insulating slabs, but are distinguished by a lower price tag. Minerals are mineral wool Paroc.
Two types of noise-absorbing coatings are produced, such as:
- Parc SSB 1which is designed for sound insulation for "floating floors" due to the horizontal direction of the fibers;
- Parc SSB 4used for isolation from impact noise.
"Isomin"which is considered heat-insulating material based on basalt fiber, has a wide range of applications. This material is represented by more than a dozen titles. "TechnoNIKOL" which is also an economy class material, is represented by 8 basalt fiber-based denominations, among which the most popular are Technoblock and Technovent. Materials like "Izovol", "Schumanet SC" and "Tizol Eurolight" have a higher price tag compared to Rockwool plates.
The most expensive in this category of building materials is the newest European design - URSA Pure One, which has the highest level of environmental friendliness and a soft structure.
Useful recommendations
In order for the insulation to be of the highest quality, it is necessary to comply with the manufacturer’s technological recommendations.
- When constructing frame-sheath partitions, it is desirable to take care of the equipment for sound insulation. In this case, Rockwool Acoustic Butts slabs are mounted between the uprights inside the partition without affecting the interior of the room.
- In the case of a junction of a partition to the ceiling with a false ceiling, initially a partition should be erected, the false ceiling should be placed on both sides of it, preventing junction by means of a damper strip.
- When installing additional insulation in relation to, it is necessary to ensure that the facing of surfaces, if it is made of sheet material, does not rigidly adhere to the ceiling and floor structures, in order to avoid transmission of sound vibrations.For example, cladding sheets should not rest against the floor, it is required to leave a gap of 2–5 mm, which must be closed with a sealant or use a damper tape.
- Self-tapping screws for mounting are selected on the basis of the material on which they will be fixed. For a tree, self-tapping screws with large and wide threads are necessary, for metal profiles - pointed-pointed screws with a hidden cap, for a profile with a thickness of more than 2 mm, the use of self-tapping screws is required. For fixing to the ceiling, it is desirable to use plastic plugs that do not transmit sound.
- Sound insulation walls can be applied even in wet areas, for example, in bathrooms. However, it should not be forgotten that to cover them, it is necessary to use moisture-proof sheets GVL, laid out in two layers, covered on the surface with waterproofing impregnations and ceramic tiles.
- One of the main conditions for ensuring good insulation is the installation of stone-fiber plates in the case, that is, as close as possible to each other, which will exclude the appearance of even thinning gaps and gaps between them.
- Improve the sound insulation effect can use a double frame, which consists of two rows of racks,unrelated.
- If there are cracks or cracks on the surface of the walls or other bases, you should not use foam. The best option would be to use a vibration-based silicone sealant.
- Since sound propagates through the slits, it is necessary to carry out each node of the structure with high quality in order to prevent a sharp decrease in the sound insulating effect as a result of negligent work.
Life hacking from the company Rockwool - in the next video.