Dual-circuit gas boilers: technical characteristics and review of popular models
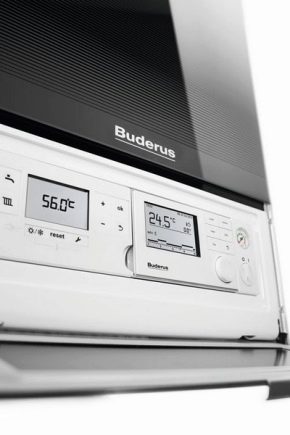
Dual-circuit gas boilers are compact two-in-one systems. They solve the problem of heating and supply the house with hot water. It is convenient and beneficial for premises that are autonomous from centralized communication systems. Select the appropriate boiler for specific operating conditions will help technical specifications and an overview of popular models.
Device
A gas boiler is a device for converting fuel into heat energy. There is a transformation in the process of combustion of substances of natural origin.Methane or propane-butane is commonly used as a fuel, but other compounds are also found. Fuel type is not the only difference. The boilers differ in terms of efficiency, thrust and type of ignition, in terms of placement and function. Efficiency ratio depends on fuel utilization. There are two types of boilers: convection and condensation.
The first type refers to the traditional. They are less efficient because they use only the heat of combustion of gases. Convection boilers are designed so that they do not form condensation. To do this, the temperature of the flow and return line varies slightly - by 15-25 degrees.
The second type is more modern. Its efficiency is higher due to the fact that not only the heat of combustion, but also a pair of condensate works on heating the room. The energy that the device has spent on the formation of condensate, also works, and does not fly into the street through the ventilation system.
According to the method of ignition emit electronic devices (autostart) and boilers with piezo ignition (manual start).
The type of thrust is natural and forced.The first is characterized by an open combustion chamber, the second - closed. According to the method of placement, wall and floor models are distinguished. On functionality - single-circuit and double-circuit. This characteristic is fundamental when choosing equipment for an autonomous communications system.
Single-circuit boilers provide only heating in the room. In order for such a boiler to also heat water for sanitary needs, it is required to connect an indirectly heated water heater to it.
The functionality of a single-circuit boiler is limited for several reasons:
- The contour of the heating system has a closed loop. It is necessary for economical and efficient operation.
- Water in the system is too hot for plumbing needs. Its temperature is close to the boiling point.
- For domestic needs need running water. Due to the fact that it contains a lot of natural impurities that seep through the filter, scum forms inside the radiators. It reduces heat transfer and leads to wear of system elements.
In this connection, a separate system combined with a boiler is required to heat the sanitary water.
The double-circuit gas boiler is arranged differently.Behind the small building there is a mini-boiler room. Thus, a double-circuit boiler differs from a single-circuit boiler in that it performs both functions at once. It provides both heat in the house and heats the water for hot water supply. In addition, it is equipped with automatics, which controls the safety and efficiency of this mini-boiler room.
The boiler is different from the gas column. Its main purpose is to heat water. While the boiler is designed for space heating, the column will not cope with heating due to the small capacity.
Boiler design
- Housing It has a small size and looks like a neat metal cabinet. Performs two functions: aesthetic and protective. Beautiful appearance gives the chance to mount a copper in a visible place. The robust housing protects the internal system from water, dust, and mechanical damage. Outside the enclosure, surrounding objects are protected from ignition.
- Circular pump. Required for forced ventilation. The working cycle of the device begins with it.
- Three-way valve. It starts up gas and makes it possible to switch the device to the heating mode or the heating of sanitary water.
- Elements of ignition. Modern boilers are mostly equipped with automatic ignition.
- The combustion chamber. Open or closed burner compartment.
- Burner. Source of thermal energy. It is it that heats the coolant and releases thermal energy for the heating system and the needs of hot water. The operation of the burner controls the automation.
- Heat carrier. This is a liquid medium, which is necessary for the distribution of heat along the heating system circuit. Non-freezing water based liquid with ethylene glycol and special chemical additives. The heat transfer fluid does not harm the elements of the system and does not adversely affect human health. In addition, it protects the batteries from corrosion inside. High-quality coolant provides a high heating temperature (up to 110 degrees Celsius), does not ignite, and maintains a sub-zero temperature to -65 degrees Celsius. Thanks to these properties, the boiler can be used even in harsh climates and lay part of the communications on the street.
- Heat exchanger A device for transferring heat along the contours of the boiler. Heat exchangers are primary, secondary and combined.
- Automation. This is a system of sensors that monitor the operation of the boiler.They are responsible for stability, efficiency and safety. The first group of sensors starts and stops the burner as needed. The second group shuts down the system in potentially dangerous situations. For example, if the gas goes, and the ignition does not work, the system automatically stops the flow of gas and signals the presence of a fault.
The design of double-circuit boilers is almost 100% identical, but the elements themselves in different models may differ from each other.
Types of heat exchangers
The heat exchanger is a constructive element of a double-circuit boiler, which is responsible for the transfer of thermal energy. Between themselves, heat exchangers differ in two criteria: design features and material of manufacture.
According to the structure there are two types of heat exchangers:
Separate
Split heat exchangers represent a system of primary and secondary heat exchangers. Primary is used to heat the coolant in the heating system. Secondary is responsible for heating the sanitary water.
Since the heating circuit needs a higher temperature, the primary heat exchanger is considered the main one.It is located directly above the source of thermal energy - a gas burner.
Secondary heat exchangerusually located after the primary. Heated not from the heat of the burner, but from the previous heat exchanger. Such an arrangement is convenient, economical and efficient, as for plumbing needs do not need water as high as possible.
The appearance of heat exchangers with a separate structure differs in boilers from different manufacturers.
Curved metal pipes with fins of metal plates are used as the main element. In the upper and lower corner diagonally there are two branch pipes: for entry and exit. The secondary heat exchanger is usually more compact. It is a plate construction of small width, length and thickness. There are already four branch pipes here, they are located at the corners of the upper plate. This design have a radiator-lattice heat exchangers. Heat is spreading efficiently through it, but this is not the best option.
Another type of heat exchangers - with a metal "shirt"through which the pipes with coolant.
Pluses of separate heat exchangers:
- Service life is longer than that of the combined models. This is due to the fact that the cross-section of the pipes is larger and they are less likely to clog.
- Elements of the system can be repaired separately. No need to change the entire heat exchanger. You can fix a local problem and save time and financial resources.
- Comfortable water temperature in both circuits. In the closed heating system, it is high, and in the sanitary one it is acceptable to use the temperature. There is no risk of getting burned by opening a hot water tap in the shower or in the kitchen.
- Slowly build up inside the tubes. This is due to the fact that the fluid in both circuits is constantly circulating and does not stagnate.
Disadvantages:
- large dimensions in comparison with boilers with heat exchangers of bithermic type;
- In such a system, a weak point is a three-way valve.
Bitermichesky
Bitermic heat exchangers are distinguished by the fact that both circuits (for heating and DHW) are combined into one node. That is, they are not structurally separated from each other, both primary and secondary. Bitermic heat exchangers are mainly of a radiator-lattice type. They consist of a coil and plates that increase the heat exchange area.Only nozzles are no longer 2, but 4 - a pair for each circuit.
Pluses of bithermic heat exchangers:
- highest possible compactness;
- effective work.
Disadvantages:
- failure of one element leads to a failure of the entire heat exchanger;
- service life is less than that of a split type boiler;
- when opening the tap in the kitchen or in the shower room, care must be taken, because the water temperature is very high, you can get burned.
Both types of heat exchangers are made from metals. This material is durable, long serving, effective as an element that transmits the thermal energy of the liquid.
Different metals are used for their production: cast iron, copper, steel, stainless steel, aluminum alloys. Let's compare these materials according to the main characteristics: weight, price, durability, installation, service life, susceptibility to corrosion, heat transfer efficiency.
Cast iron heat exchanger
- Weight. The hardest of all metals. It is twice as heavy as steel and three times as heavy as copper. This feature is important to consider when designing the location of the boiler, since the product with a cast-iron heat exchanger placed on the wall will not work. There will always be a risk that the structure will fall.
- Low-power boiler with cast-iron "heart" does not require strengthening the foundation, but wears out faster and less effective. For an impressive unit with high power it is necessary to strengthen the foundation for the boiler.
- Price. At cost, boilers with cast iron heat exchangers are in the low price segment. This is due to the availability of the material and the fact that such a heat exchanger is of only one type - with a separate structure. And they are by default cheaper bithermic. However, the complexity of the installation of such a boiler can cost more than steel or copper.
- Strength. It sounds paradoxical, but with its thickness and resistance to fading, cast iron heat exchangers are very fragile. They are easily damaged during transportation, and they are also afraid of thermal shock. That is, if cold water gets on a hot cast iron heat exchanger, it will crack.
- Installation. It is possible to install a boiler with a cast-iron heat exchanger only on the floor. It will take at least two pairs of hands to move a heavy product from place to place. When installing it is important to be careful. Pig-iron heat exchangers do not tolerate condensation and cold water, which can get on thermal elements through poor-quality ventilation. The special feature of cast iron heat exchangers is that they are collapsible.In this form, it is more convenient to mount and repair them.
- Life time. This indicator is as high as possible in cast iron - up to 50 years on the condition of careful operation of the boiler.
- Corrosion. Cast iron, though weakly amenable to chemical reactions, is nonetheless susceptible to both dry and wet corrosion. In addition, over the years, it accumulates scale, which reduces the efficiency of heat transfer.
- Heat transfer. Cast iron copes with the task of sending heat from the burner to the coolant. When starting the boiler, it is important to take into account that the cast iron heats up and cools very slowly. After shutting down the system, it will continue to heat the pipes for a few more hours.
Steel heat exchanger
- Weight. It does not make the boiler heavier, so it is used in equipment of any capacity. You can place the device with a steel heat exchanger on the floor and on the wall.
- Price. Steel - enough "running metal". Its cost may be higher than that of cast iron, but at the same time, boilers with steel elements are found in the economy segment and among more expensive models.
- Strength. Steel is quite resistant to burning, not afraid of mechanical damage and thermal shock. But she has a weak spot.With frequent changes in temperature, the product wears out at the seams, in places of poor-quality welding.
- Installation. Lightweight heat exchangers are easier to install because of their low weight, but the design is no longer collapsible. In the event of a malfunction, it will be necessary to extract and repair the whole element.
- Life time. In this regard, steel loses cast iron for several decades. Many manufacturers give a sure guarantee for 10-15 years. Some are limited to 5 years.
- Corrosion. Products made of ordinary steel when exposed to water are subject to chemical reactions. Stainless steel heat exchangers do not know such a problem.
- Heat transfer. The boiler with the steel "inside" heats up quickly and cools quickly. Differs in high efficiency of heat exchange.
Copper Heat Exchanger
- Weight. Coppers with copper elements are the lightest and most compact.
- Price. Imported products are always more expensive than domestic ones, and copper is mainly used in European models. Therefore, a boiler with such a filling is more expensive than with a cast iron or steel heat exchanger.
- Strength. Copper serpentine and the plates on the ribs are very thin. They are prone to burning and wear out due to chemical reactions with the liquid.And because of the softness of the material, they are least resistant to mechanical damage. All this requires careful handling of the boiler.
- Installation. Small weight and dimensions make the boiler with a copper heat exchanger convenient for installation with their own hands. The design is integral, which affects the subsequent repair.
- Life time. Copper is the lowest. If for steel 15 years is an average figure, then for a copper heat exchanger this is the ceiling.
- Corrosion. Copper products do not rust, but oxidize. This reduces the efficiency of heat transfer and reduces service life.
- Heat transfer. Copper heats up and cools as fast as possible.
Aluminum heat exchanger
The aluminum heat exchanger is used in many modern condensing boilers. It is ideal for this purpose due to the fact that it is not susceptible to corrosion and oxidation.
For all other parameters, except for the service life, it is close to copper: light, soft, effective in terms of thermal conductivity. In terms of service life, it exceeds copper by 5-10 years.
In some models of double-circuit boilers with an aluminum heat exchanger, steel plates are used to make it more rigid and resistant to damage.
Types of burners and combustion chambers
Dual-circuit gas boilers for domestic use come with an open and closed combustion chamber. Devices with an open chamber are based on natural fatigue. Oxygen, necessary for the combustion reaction, they suck from the room. Combustion products are returned to the room. Therefore, a powerful ventilation system is required in the room. It should work continuously, cleaning the air from pollution.
Even good ventilation does not always relieve carbon monoxide and lack of air in the room. In order not to be stuffy at home, boilers with open fire chambers are recommended to be carried out in separate rooms. It is simpler to equip such furnace or boiler room according to requirements of safety measures. And in accordance with building codes, it is easier to obtain a permit, because equipment with an open firebox cannot be installed in residential premises.
But there are advantages to this type of boilers. They are many times cheaper than wall-mounted units with a closed firebox, they work silently and often do not depend on electricity.
Boilers with a closed chamber suck air from the street. Combustion products are returned there.For this, the boiler is equipped with a ventilation and smoke removal system. Inside the ventilation system, the fan is continuously running. This makes the system volatile.
The advantage of devices with a closed firebox is in their compactness, high efficiency, neat appearance and safety. They do not burn oxygen from the room, so there is no feeling of stuffiness. In addition, the air from the street is colder than the products of combustion. It cools the system and increases the safety of the gas boiler.
Inside the chamber is a burner. In it, oxygen interacts with the fuel, then, at the outlet of the mixing device, is ignited. A steady flame is formed. Fuel combustion devices vary in the type of fuel used. In addition, the method of interaction of the fuel with oxygen, the type of regulation of the flame, the method of igniting the finished mixture: electric and manual.
Another classification - domestic or industrial burners, is not important. In the scale of a residential house or apartment, only household burners can be used. The remaining devices are used only on industrial facilities.
Types of heating burners differ in several parameters.
On fuel:
- Liquid fuel. Function on liquefied gas, gasoline, kerosene. For stationary models, liquefied gas is preferred. Other types of fuel-liquid is used in mobile burners.
- Solid fuel. Often used in cottages and country houses. They are relevant when the boiler is mounted in a decorative case that simulates a stove or fireplace. Firewood, coal, pellets are suitable as solid fuels.
- Gas fuel. As a rule, these are natural gases: propane, methane, methyl butane. Under the natural gas "sharpened" most double-boiler.
- Multi fuel. Universal, but rare. To function, they are suitable for several types of fuel at the same time.
On oxygen supply:
- Injection. Catalyst intake occurs before the gas supply to the chamber.
- Atmospheric. Identical on the principle of working with injection, but the amount of oxygen with which the chamber is enriched is less.
- Regenerative. The gas is mixed with oxygen in a heated state. There is one more version of this type - regenerative. It is heated and gas, and oxygen, and then they are mixed.
- Diffuse. The gas is mixed with oxygen in the combustion process. There are also pre-mix, full and partial devices.
- Blow (blown). The air enters the chamber compartment in portions. Instantly mixed with gas.
Consider the most common types of burners for the method of oxygen supply and operation.
Atmospheric
Boilers with this type of burners provide the needs of small premises of up to 100 square meters. m. Their standard grade. On production, the device is supplied with a gas burner. To switch to liquid or solid fuel, the boiler must be converted. Despite the simplicity of the design, this can only be done by a professional.
Atmospheric burners work by sucking air naturally. He enters the place of the gas outlet. Natural gas passes under pressure through a perforated hollow pipe. When mixed, the substances ignite. Formed steady "torch". As ignition, a piezoelectric element or electrical ignition is used. Devices with atmospheric burners are light, compact, cheap, safe, emit minimal noise.
Blowing
Often they are called ventilating or blowing.Unlike atmospheric burners, they are not installed on the boiler during factory assembly. They need to be purchased separately. Blast burners are used in closed-type chambers. The fan is part of the device burning fuel, so the oxygen enters the gas outlet instantly, and the mixture also ignites in a split second. The main feature of blast burners is high efficiency. In addition, they are efficient, compact, safe, easy to manage, reliable and durable. They can be used with any kind of fuel.
Disadvantages of equipment with ventilation burners - in high price, energy dependence and energy costs. Such equipment is more noisy. The noise creates both the fan and the gas-air flow that leaves the burner nozzle under pressure.
To reduce the noise level can an additional element in the design - a silencer. This increases the cost of installing the boiler, but makes the neighborhood with him in a residential area more comfortable.
Diffuse
Sometimes the name diffusion-kinetic occurs. The principle of operation of such a device is that the fuel is first ignited, and then oxygen is added.Air flows in portions, as needed.
Such burners in domestic boilers are rarely used. More common on an industrial scale.
Combined
Their peculiarity is that it is possible to use both gas and liquid fuel. At the same time, reconfiguration of the equipment takes a little time. There are two disadvantages of such burners: overpriced at low efficiency. Modern boilers are equipped with a function to regulate the intensity of the torch torch. There are three of them:
- Single Stage. Work in one mode. From time to time, the automatic switch on and off the burner when the coolant heats up to the desired temperature. Boilers with a single-stage burner control system are cheaper, but their life expectancy is small. Constant on and off does not benefit the equipment.
- Two stage. In turn, they are divided into two types: with instant and smooth switching. The essence of the operation of such burners is that they do not turn off when the desired coolant temperature is reached, but reduce the intensity of work from 100% to 50-60%. Switching of modes is regulated by automatics. This mode of operation is gentle.It increases the efficiency of the boiler and prolongs the life of the internal mechanisms.
- Modulated. They can still be called multistage. The intensity level in them is regulated by automatics in the range from 10 to 100%. The burners are mechanically regulated, pneumatic or electronic.
This is the most functional and economical type of burner. They reduce fuel consumption by 15-20% and do not fall into disrepair with the whole boiler when its service life goes out. The modulated burner can be removed from one device and rearranged to another.
Automation and protection levels
The automatic control system ensures stable and safe operation of the gas boiler without constant monitoring.
Automation functions:
- protection of the boiler from overheating and the entire system from overload;
- gas supply shutdown in emergency situations: ignition does not work, too much or too little gas is released, the ventilation system is not working;
- adjusts the intensity of the burner;
- economical fuel consumption;
- prolongs the life of the boiler.
Automation is easy to manage. The clear settings system helps the owner to tune the equipment to work in the desired mode.Automatic systems are volatile and non-volatile. Devices whose work is supported by electrical energy, more complex structurally and correctly. Externally, they are represented by a control panel.
To work, they need uninterrupted power supply.
Tasks of electronic automation:
- activates the gas supply and stops it;
- automatically starts the operation of the heating system, focusing on the indicators of thermometers;
- adjusts the intensity of the burner, according to the thermostat;
- controls the operation of the boiler in emergency situations;
- shows indicators of the current state of the device on the display;
- protects the three-way valve from malfunction;
- does not allow equipment to overheat or freeze.
The newer and more complex an automatic system is, the wider its functions are. The most modern units are remotely controlled and require virtually no intervention of the owners in the work.
Automatic equipment independently diagnoses the operational state of the boiler, detects faults and signals them. Thanks to this, it is possible at the initial stage to detect breakdowns and shortcomings and quickly fix them.This increases safety and prolongs equipment life.
Independent devices are mechanical. Their design is simpler, and the functionality is more modest. However, it is more practical to use a mechanical system, since it does not depend on a power outage.
Manual control is carried out with the help of toggle switches. Their location and purpose is extremely understandable. Toggle switches are marked and equipped with a scale of divisions. On this scale, you can set the required heating temperature for the heating system and sanitary water. When the desired temperature is set, the thermostat controls the operation of the burner. After that, the system stops working until the heat level drops to a critical minimum. Critical is only for the system. A person at this moment can be quite warm and comfortable.
Independent automation also has sensors that are sensitive to traction and flame. That is, the gas supply stops if the ventilation system stops working or the fire goes out on the burner.
The structure of different types of burners in most models is the same:
- gas valve;
- two types of thermostats with sensors: limit and adjustable;
- thrust sensor;
- fuel (gas) pressure stabilizer;
- two-stage burner valve;
- buttons, toggle switches or knobs.
Principle of operation
Dual-gas boilers are used primarily for heating a private house. Less often for an autonomous system of heating and hot water supply in the apartment. In the first case, the installation of a boiler with an open or closed firebox is relevant, in the second case - only with a closed one.
Differences in boiler operation depend on the type of furnace and some other design features (method of operation of the burner, type of heat exchanger, device of the ventilation system). However, the principle of its operation in any device is one - it is based on the heating of the coolant, which is in the heat exchanger. Consider how the system works when heating the heating medium for heating and how it works when heating sanitary water (DHW).
Heat carrier is heated as follows:
- The gas boiler is started automatically or manually using the toggle switch.
- Turns on the circular pump. His task is to forcibly suck air in order to get oxygen into the combustion chamber. The secondary task of the pump is to dispose of the combustion products through the ventilation system.
- The gas valve opens, gas is released under pressure and mixed with oxygen. Different types of burners provide a different sequence. The gas can be mixed with oxygen before ignition, at the same time or after.
- Triggers or piezo ignition. A stable "torch" of fire appears on the burner.
- Heat exchanger is heated. Inside it there is a coolant (water, antifreeze, or other liquid suitable for transferring heat through the pipes of the heating system), it also heats up. Hot fluid (heating temperature 30-90 degrees) circulates through the pipes, warming the air in the room.
- The system works in this mode for some time until the sensors on the boiler record the required parameters. When the air temperature warms to a comfortable (manually set by the room owners) level, the system temporarily turns off the gas supply and the burner. In addition, the sensors continuously record such readings: flow and return temperatures, gas pressure, system pressure, torch stability, and thrust. In case of a malfunction in one of the components of the system, the automation switches to emergency mode and turns off.
The system can regulate the temperature of the flow or return. It works like this: the heating system warms up, the temperature sensor sends a signal to the electronic board, the board processes the signal and stops the gas supply. The coolant also ceases to circulate through the pipes. This is how the most primitive devices work.
Boilers with modulated burners take into account an important factor: the coolant and heat exchanger do not cool down instantly. Therefore, after switching off the gas, the circulating pump continues to operate for a set time. It cools the heat exchanger so that the liquid inside the pipes does not boil and the elements of the heating system do not fail. This function is called the coast down.
When the coolant cools down to a certain level, the sensor detects a drop in temperature, gives the board a signal, and the operation of the boiler resumes.
Water heating for domestic needs is a little different:
- The pump is started, then the valve starts up gas, the fuel mixture lights up above the burner.
- Heats up the primary heat exchanger.
- A person turns on hot water in the kitchen or in the shower.
- Cold water begins to flow through the boiler.
- Triggers the sensor duct, sends a signal to the board.
- The board switches the three-way valve to the heating of the secondary heat exchanger. At this time, the water in the heating pipes does not circulate. The primary heat exchanger heats the secondary, and the secondary, in turn, gives off heat to the DHW. Do not heat the plumbing water directly above the burner; it will be too hot. There is a risk of getting burned by opening the faucet.
- When the tap in the kitchen or in the shower is closed, the system performs the actions in the reverse order: the sensor detects that the water flow is stopped, the board switches the valve back to the heating needs.
There is nothing wrong with such a boiler. For an hour of work for the needs of the DHW heating system is almost not affected. The air temperature in the room drops by only 1-2 degrees. The valve does not serve both the heating system and the DHW at the same time, because it has the priority of servicing the plumbing needs, that is, the DHW.
The most modern models of boilers are equipped with a quick start function. In such boilers, the secondary heat exchanger is stably hot. The water in the kitchen immediately goes warm or hot. No need to wait until the system heats it, and in vain to drain the water.
Advantages and disadvantages
Details to consider the pros and cons of specific models can be in the reviews of the owners and recommendations of experts. Here we consider the generalized characteristics of two types of gas boilers: floor and wall boilers. The floor double-circuit copper is a powerful non-volatile device for heating and needs of GVS. It is made mainly of iron or steel, has an open combustion chamber.
Its advantages are:
- cheap and reliable;
- power range - 10-700 kW (will be able to heat a huge cottage with an area of up to 800 sq. m);
- runs on natural fuel (gas, wood, coal);
- makes little noise for two reasons: it works on natural friction and is taken out to non-residential premises;
- has high efficiency - up to 90% of the heat during the combustion of fuel work on heating the room and water;
- can be of different configuration: with open or closed firebox, automatic and mechanical control, additional features;
- long service life due to cast iron or steel heat exchanger - up to 50 years.
Disadvantages:
- large dimensions and weight;
- can be used only in a private house;
- a separate room for the boiler room (furnace) is required, because the floor boilers make the air in the room stuffy and hot;
- piping elements of the floor-standing boiler are not included in the basic package, they must be purchased separately;
- cast iron heat exchangers are fragile and are only separate in their design, and bithermic are more economical to use;
- installation of the floor boiler is more difficult than the wall.
Wall-mounted boilers are becoming more common, despite the lower power and volatility.
Their advantages:
- can be installed in any room, including the apartment, in order to make it autonomous from central heating systems and hot water supply;
- compact size and low weight;
- polyfunctionality: electronics provides additional functions in the form of self-diagnosis and maximum independence in work;
- safe and reliable work;
- the absence of harmful emissions into the air inside the room, since it works only on artificial plastics, that is, the exhaust air is discharged outside;
- economical work: low fuel consumption and electricity due to automation;
- efficiency sufficient to heat 200 square meters. m;
- high efficiency;
- several points of water intake: provides hot water and in the kitchen, and in the bathroom, and in other places where there is a tap;
- there are models with a boiler, which stores a supply of sanitary hot water up to 60 liters;
- affordable price.
Disadvantages:
- Volatility - when the power goes out, the system stops working;
- service life - 5-15 years, because the heat exchangers are as light as possible (copper, aluminum, stainless steel), and such metals burn through;
- Additional structural elements are not included in the basic kit, sometimes even the burner needs to be purchased separately;
- limited power - 3 times less than that of the floor boiler;
- high-quality heat carrier is required;
- noisy work.
The list of advantages and disadvantages may differ not only among different manufacturers, but also among boilers of different design. So, condensation has a higher efficiency than convection. It provides the thermal energy of the fuel and the resulting steam. Turbocharged boiler is effective, but the fan and heat exchanger are not included in the basic kit. This makes it expensive to install.
Parapet boiler has more advantages than chimney, but it is more expensive and loses to other types of power.
Power calculation
Boiler power is the decisive criterion for device selection.It depends on it whether the equipment will cope with its task and whether it will not work in too intensive mode. There are several ways to calculate the power of a gas boiler. The first method is the easiest: multiply 1 kW of power for every 10 square meters. m area of the entire heated space. In addition, you need to lay 15-20% of power in case of unforeseen circumstances. For example, a sharp drop in temperature during the cold season and even a cooling in summer.
For small rooms (up to 100 sq. M.) There are enough boilers with a capacity of 10–16 kW, for houses up to 200 squares - 30–40 kW. This formula is bad because it does not take into account the features of the layout, the height of the ceilings, sources of heat loss, the quality of thermal insulation, the cost of hot water per person, the climate in the region and other important aspects.
As an alternative, you can use a more detailed formula for typical rooms. MK (calculated power) = S (area of all rooms) x CME / 10 (specific power per each 10 squares of area).
CMD has a fixed value for different regions of the country:
- for the south - 0.7-0.8 kW;
- for the middle band - 1-1.2 kW;
- for the north - 1.5-2 kW.
After calculating the MK, you need to add another 20-25% for the maintenance of hot water supply and unforeseen situations.
If difficulties arise in the calculations, you can contact the specialists of the company that will install the equipment for help.
Connection Features
Installation of gas equipment requires professional skills. Self-installation is not recommended. It is fraught with different consequences - from damage to equipment to an emergency. Special attention should be paid to the strapping scheme. This is a piping system that performs important functions: it controls pressure, removes polluted air, is responsible for maintaining the system and the absence of blockages, makes it possible to connect additional circuits to the system and disconnect it. For example, connect the boiler to a boiler of indirect water heating or a tank with a reserve.
Equipment, components and strapping system are selected individually for each case. Its features are in the installation.
There are general recommendations:
- system installation must comply with SNiP;
- the boiler needs free access for repairs;
- there must be non-combustible material under the floor boiler;
- all joints between elements must be made impenetrable;
- the elements responsible for safety are installed in a specific order: pressure gauge, valve, air vent;
- the boiler can be connected to the heating system only from materials resistant to high temperatures.
Criterias of choice
There is no unequivocal decision as to which boiler is best to choose. As with the installation, everything is too individual. For the apartment "Khrushchev" and a country cottage on two floors you need different equipment.
A few general rules of choice can be identified:
- Rate power. For a typical apartment and a small house, 24 kW is enough. For an area of 100 squares need a more powerful heater. It is important: to choose the equipment according to the power, taking into account 30% for the maintenance of hot water supply and about 10% for heat losses through windows, floors and other ways.
- Rate the location. For an area of up to 200 square meters. m enough wall equipment. Floor boilers are non-volatile, but against the background of a stable flow of electricity this is not a plus. And install them more difficult.
- Choose a closed firebox and a model with a good exhaust.
- Choose a heat exchanger for the quality of the metal. Copper is best avoided.
- Provide connection for a hot water tank or quick start function.
- Pay attention to the popular heating and "water-heating" systems from manufacturers who have received good reviews from the owners.
- Take into account the availability of the service center and the conditions of repair under warranty.
Manufacturers
Identify the strengths and weaknesses of the equipment help reviews. Review of a manufacturer on the forum is always honest. Therefore, the “national rating” should be paid attention to as an additional guarantee of reliability and practicality.
An unequivocal leader is difficult to select. Many users choose German boilers. Vaillant, Viessmann, Wolf, Bosh. The owners note their good performance, simple operation, stylish design and minimum noise during operation.
A significant market share is Italian goods. Popular are such "Italians" as Ariston, Baxi, Ferroli, Nova Florida. They have a compact size, stylish design and a pleasant price in comparison with European counterparts. The equipment is well adapted to the Russian realities (low temperatures, poor-quality water), it economically consumes fuel. It is easy to operate and equipped with automatics. On budget models, there are additional functions, up to the system of self-diagnosis. "Italians" are capricious in the installation. To work you need an experienced specialist.
Among European brands a lot of positive reviews collected Czech gas boilers Mora Sirius, Proxima, Protherm. The popularity of them provided a comfortable control, high power and reliable automation.
Cheaper, but not less quality products provide Asian manufacturers: Navien, Daewoo, Kiturami. "Koreans" and "Japanese" fell in love with the compactness and neat appearance, power, stability and adaptability to Russian conditions.
No less demanded boilers of Russian production. Although in design they are often inferior to European models, they have impressive power, a pleasant price and decent quality. And the main thing is that Russian equipment fully takes into account such nuances as water hardness, features of typical apartments and houses, climatic conditions in different regions of the country.
In the video below, see how to choose the right boiler for power, what nuances and main units in the design should be paid attention to when choosing, as well as what innovative solutions are really important for stable operation and convenient use.