Butterfly valves: device and variations
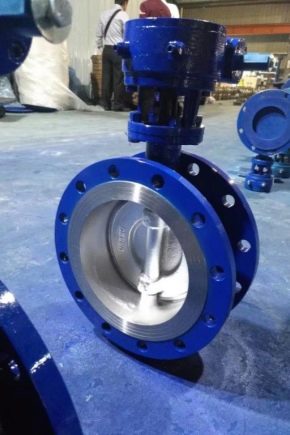
The rotary (disk) valve is a device used as a valve. It is an alternative to valves and cranes, the quality indicators of which are at a lower level. Today it is a popular type of locking devices, which is explained by its small construction length, ease of installation, unpretentious maintenance, low cost, and most importantly, good sealing.
Special features
A distinctive feature of these rotary mechanisms is the overlapping element having a disk configuration.It is located perpendicular to the movement of the flow of the working medium passing through the pipe. When the flow is blocked, the disk scrolls around its own axis by 90 degrees and blocks the armature passage. Also, a rotary flange valve may be called a pressure-tight valve, a thermal valve, or a valve. In accordance with the method of rotation of the locking element of the valve are divided into 2 types:
- axial (flap rotates around its own axis);
- eccentric (rotational movement occurs around the axis of the eccentric).
Both modifications of fittings have the similar area of use.
Principle of operation
The principle of operation of the rotary valve is based on the termination of the flow of the working medium through a flat disk, turning around the rod axis. The disk is rigidly fixed on the rod, whose axis is in a vertical position (at an angle of 90 degrees) relative to the movement of the working medium. In the closed state, the flap plane is in a perpendicular position relative to the axis of the pipeline and blocks the entire area of the flow-through portion of the valve body.Scrolling the handle 90 degrees rotates the flap in a plane corresponding to the movement of the flow, revealing the area of the flow section of the valve body.
Impermeable overlap is achieved by closely adjoining the edge of the thermal valve to the cuff made of polymer in the inside of the case. Along with the seal, the cuff protects the valve body from contact with the working medium, and when mounted between flanges it also serves as a seal between the casing of the hermetic valve and the flanges. The axis of rotation of the valve can be located parallel to the axis of the pipeline or be shifted with respect to it.
For manual control of a rotary damper having a diameter of not more than DN150, a handle is used, and larger ones are controlled by means of gear drives. To control the disk valve in auto mode, it can be equipped with an electric drive.
Kinds
According to the location of the valve body, the hermetic valves are divided into normally open ones, which, when the power supply is stopped, create a force transmitted by the output element of the actuator to the control element,the thermal valve opens and is normally closed, the flap of which closes in this situation.
By type of seals:
- elastic - in the case or on the disk;
- metal.
According to the method of fixing to the pipeline, the valves are divided into flange (completed with pipeline response elements), interflange (mounted and tightened between the flanges on the pipeline), welded (for welding) and coupling.
The power actuator of the hermetic valve can be:
- electric - excellently suited for control of automated process control systems for production processes due to the high degree of interpolation precision, it can be completed with a block of limit switches;
- hydraulic;
- pneumatic (small and light, not prone to overheating, has high speed and easy to install, often used in fire-hazardous environments);
- manual, equipped with gear;
- manual (it is controlled by means of a handle or a flywheel, which are capable of ensuring its rapid opening and closing);
- with the ability to control at a distance (remote control).
Rotary valve actuators must have the ability to block both automatic and manual control. The devices are set to automatically lock to counter the pressure of the working environment.
According to the design of the locking component (disk), the valves are divided into eccentric or symmetrical. By the level of disc shear, hermetic valves with displaced axes are divided into valves with double eccentricity and triple eccentricity. Such valves are an ideal solution for the assembly of technological valves, if a high degree of sealing of the equipment is necessary.
Materials
Disk hermetic valves are equipped with steel housings (from wear-resistant, low-alloyed, unalloyed constructional or tool, and stainless steel) or cast iron (from magnesium, with increased strength or gray iron). In addition, you can find modifications of non-ferrous metals - copper, bronze, aluminum and nickel alloys. For the protective coating of shells, compositions of ultra high molecular weight polyethylene, fluoronone, thermoplastic polymervinyl chloride, reinforced composite plastics and other materials are used.
Disks, as a rule, are made of cast iron or steel. Replaceable liners (segments) for discs are made of rubber and from various chemical substances based on it - ethylene-propylene rubber, fluorine-containing rubber, nitrile rubber, and also polyorganosiloxanes or thermoplastic polyethylene. Elastomeric or rubber-metal segments (liners) increase the service life of disc valves under high pressure and high temperatures.
Standard sizes and marking
By marking the valve, you can set its own regulatory document, pressure, conditional passage, the current mechanism and type of connection. The armature has a marking that conforms to the standard and has a symbol in the scheme in the form of “32с3п д50ру10”, where:
- 32 - type of reinforcement;
- c - the body is made of steel;
- 3 - drive complete set: a reducer (mechanical) with gear and screw gear;
- n - material for manufacturing sealing surfaces is plastic;
- Du50 - Ø of the connecting part is 50 millimeters;
- Ru10 - the greatest overpressure - 10 kgf / cm.
Types of disc hermetic valves according to the method of attachment are divided into flange, interflange and welded. The type of drive varies and can be pneumatic, hydraulic, flanged.
Wafer devices, in accordance with the provisions of GOST No12521, are manufactured in Ø from 100 to 1 600 millimeters. The valve is divided into 4 categories according to the highest pressure: up to 0.1 MPa; 0.25 MPa; 1 MPa; 1.6 MPa. Products intended for operation at temperatures of the substance transported through the pipeline from -60 to +300 degrees.
A separate category includes valves in cases made of titanium alloys, the scale of the diameters of which varies between 100 and 1 000 millimeters. They are designed for pressure up to 0.63 MPa and the highest temperature of +300 degrees.
The advantages of the design include:
- ease of mounting;
- have insignificant indicators of hydraulic losses;
- can exercise control and serve as a regulatory element;
- have an extensive range of diameters and sizes;
- in case of leakage, the sealing element changes without difficulty;
- have good heat resistance;
- relatively low price.
Minuses:
- with a manual method of controlling a system having a significant diameter, the necessary condition is to mount the gearbox;
- only mechanisms with a soft rubber-technical seal have a high degree of impenetrability, and modifications made entirely of metal do not so thoroughly block the passage of the work flow;
- in the case of using a locking body in the role of a regulating valve, obtaining flow characteristics is problematic;
- in the open position, the disc remains in the aisle, which complicates the mechanical cleaning of the pipeline.
Scope of application
Having such high technical functional properties of equipment, this device managed to find a suitable application - in the form of reinforcement to block the flow of the working environment of an extensive range of systems and industrial production.
Butterfly valves are practiced:
- in centralized systems of heat and water supply;
- in local water supply systems of housing and communal services;
- in systems of decentralized hot water supply;
- in the role of control components of gas pipelines of different pressure and technological ventilation;
- in cooling systems of industrial enterprises, power plants and energy facilities;
- at the enterprises for the production of chemicals;
- in the construction industry;
- for enterprises for the production of food;
- in the pharmaceutical industry.
In the role of taps and valves of centralized, local or local water supply systems, as a rule, hermetic valves with cast iron bodies and a valve diameter from 25 to 3000 millimeters are practiced. For these purposes, cranes are used both with the possibility of manual control, and equipped with specialized blocks and power drives for opening and fixing the thermal valve in the required position.
The discs themselves are made from steel or alloys. Valves used for contaminated and untreated water are equipped with reinforced plastic cuffs and special stem seals. The fixing of the rod to the rotary valve is multipoint - the rod and the disk are fixed at several points by means of electric welding, steel dowels and rivets. In systems of local hot water supply of cold and hot water, both ordinary gate valves with cast iron body and steel flange samples are used.For distribution points, boilers, and high-pressure steam supply pipelines, seals are made of heat-resistant plastic that is able to withstand considerable temperature under steam pressure.
Gas pipelines and air ducts are necessarily equipped with valves with a high degree of surface treatment and factory-tested vacuum.
Installation
Sealed valves can be mounted in open areas, in chambers, wells, rooms. Installation and maintenance of dampers should be handled by personnel who have learned the design of the product and the requirements of the operating instructions.
When mounting the valve is required to know the list of important rules.
- Before proceeding with the installation, it is necessary to verify the diameter of the valve itself with the diameter of the flanges. These two values must match. The difference in diameters can lead to improper functioning of the system and the occurrence of an emergency.
- By the preparatory work is the thorough removal of scale, corrosion and debris from the inner walls of the pipeline. This makes it possible to create conditions for a better hitch system.In addition, this garbage can harm the cuff during operation.
- When installing any kind of rotary shutter under any circumstances, do not use gaskets.
- Starting installation, it is necessary to partially open the disc valve. In this case, the disk should not go beyond the line of the device.
- In the process of tightening the bolts connecting the housing and the flanges, the procedure should be carried out evenly. Otherwise, incorrect tightening can cause damage to the threaded connection or skewed surface.
- After installation of the structure, it is required to test its performance. The disc should easily switch from closed to open position, and vice versa.
- If you follow all the recommendations, the system will work properly over a long period of time.
Installation of butterfly valves is not always performed in open space conditions, as a result of which it is necessary to know all sorts of installation options.
- Welding of special quick-release connection (mounting / dismounting insert). This mounting method is the most reliable and most often practiced by experts.Intermediate flanges put specialized installation insert, which secures the design during installation. This is followed by the procedure of welding the flanges to the pipeline. Then, as the flanges are securely fixed, the insert is removed, and a disk barrier is mounted in its place.
- Welding of the assembled pipeline with the valve already fixed. It is used if the system does not allow to apply the above method. Pieces of pipes (not less than 2 diameters of the hermetic valve) are fixed to the flanges by welding. Sealed valve between the flanges with bolts tightened into a holistic design. All processes are performed in accordance with the instructions from the manufacturer. Then pieces of pipe welded to the baseline. The negative side of this method is a large number of welds.
- Welding flanges with a sealed valve mounted. The installation resembles the first method, the only thing that instead of the mounting insert is a butterfly valve applied on the bolts. It must be remembered that the design is forbidden to end up, because after the initial welding of the flanges, the flap must be pulled out andperform complex welding. After that, you can make a final mount mechanism. This method requires special skills, because during the initial tacking of flanges the saddle seal may be damaged.
Choose one of the above mentioned methods according to the situation and qualification of the installation team. But the most important selection criterion is the place where the butterfly valve will be located.
In most cases, the valves are installed at the very beginning of the system and in a place where, if necessary, you can quickly stop the flow of water or any other working medium. Mounting of this component of the system is allowed when branching the pipeline. Several dampers are used if the pipeline has a large scale. When installing a sealed valve in any system, you must have an idea of its technical parameters. The flow rate of the working medium can be extremely large, which will lead to the mounting of more compliant equipment.
Also, butterfly valves are installed directly in front of the consumer.This makes it possible to ensure the speed of overlapping of the system in case of non-compliance with agreements by the consumer. Repair work and maintenance of the system is carried out by those who put the item. On the pipeline itself, the flanges should be placed parallel to each other and at a predetermined distance. In the middle of them must pass the hermetic valve without difficulty. Such installation provides subsequent comfort during repairs and maintenance.
When operating the valve element in an environment that causes the destruction of materials, it must be mounted with a slight slope. The best option - in a horizontal position. Then the system does not litter with garbage and other substances.
After mounting of the butterfly valve is completed, it is necessary to make sure that it was made correctly and the equipment is ready for safe operation. To do this, the first step is to check the uniformity of tightening the bolts around the perimeter of the flange connections. If everything is normal, then it is necessary to open slowly and smoothly, and then close the flap.The installation is correct if the equipment opens and closes easily and freely.
When choosing a butterfly valve, it is necessary to take into account the dimensions of the system and the valve. Gate valves are linear motion valves. This is particularly significant if the butterfly valve uses an upward stem. Valves must be mounted perpendicularly (horizontally in relation to the ground) with a manual drive in the upper position. This facilitates easy access for maintenance and parts rotation. Small mechanisms can be mounted in vertical lines, but the gravitational force has the desire to pull the rotary hermetic valve.
An overview of the principle of operation of the butterfly valves is viewed in the next video.