Valves: types, purpose and recommendations for installation
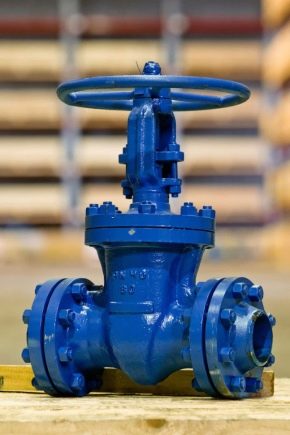
Shut-off valves are used in various industries dealing with pipelines of gaseous substances, steam, water, oil, oil-containing substances and other liquids. Such valves are necessary to shut off pipeline sections of any system, to perform installation or repair, to cut off the supply of transported substances to consumers, as well as to meter the supply of these substances and protect the pipeline network and its elements from overloads.
Purpose and device
The main purpose of valves is to reliably disconnect a section of the pipeline or other pipelines connected with it and devices from the flow of the medium transported through them, thus ensuring the safety of the planned works.In addition to the shutdown (cut-off) of the medium circulating in the system, the valve also has other purposes. With its help you can regulate, distribute, mix and delete the used environment.
In accordance with the pipe design, type and parameters of the flow of the medium, the necessary shut-off, control and discharge devices are selected. For example, they must comply with the pressure in the system, the type and temperature of the medium, the design features of the pipelines (diameter, type of connections) and meet all safety requirements. By appointment, locking devices are divided into several groups.
- General purpose. It is used on water and steam lines, in gas lines of urban networks and heating systems.
- Special purpose. It is used at high pressure, as well as in cases of low or high temperatures, toxicity, viscosity, corrosivity, radioactivity and abrasiveness of the transported substances.
- Target fittings. Designed for individual cases stipulated by the technical regulations.
- Plumbing. Fittings of small diameters for home appliances.
- Ship. She is equipped with sea and river vessels, are produced taking into account the specific operating conditions.
- Unique. Manufactured by special orders for industrial and experimental installations.
There are such types of locking devices:
- valves with cast iron and steel housings;
- shut-off or shut-off and control valves;
- cranes of various types and devices;
- butterfly valves;
- control valves;
- safety and protective products.
All listed locking devices are similar in design. They are a hermetically sealed case with a locking unit placed in it. This node must tightly block the pipeline in which it is installed, dividing it into parts — sections up to the valve along the medium and after it. The closure assembly consists of two main working elements: a saddle and a closure member mechanism. These two devices, touching their sealing surfaces, create an obstacle to the movement of the medium used in the pipeline. In addition to the valve, the valve has parts for connecting to the pipeline: flanges, threaded nozzles, smooth nozzles for the weld.
Classification
All pipeline fittings are classified in several categories depending on the application, functional purpose, design features, material, environmental parameters, method of attachment.
By application
Several types of fittings for use are considered.
- Shut-off. The most numerous class of devices, which is about 3/4 of all used valves. It is used to completely shut off the flow of the medium in the pipeline, as well as its start-up, if necessary. These include: valves, valves, taps, manufactured for pipelines of various diameters, working media and parameters. The scope of such devices is quite wide: from valves for pipelines of steam, water, gas to conventional valves for the heating system and the kitchen.
- Regulatory. This type of device includes all kinds of control valves, called at industrial enterprises regulators of fluid pressure, liquid level in vessels, pressure drops between different media, as well as throttling valves. Regulating valves are not considered to be purely shut-off members, therefore, they are usually used with shut-off units consisting of valves or valves installed both before and after the regulator.
- Safety. This type of device provides protection for steam lines, water pipes, gas pipelines and other pipelines with equipment located on them against excess pressure above the allowable value by automatically discharging a part of the working medium. Safety valves include the following devices: safety valves, ICS (pulse-safety devices), rupture discs and medium bypass valves.
- Protective. It is used to protect pipelines and equipment from breakdowns and accidents with unacceptable for them parameters of industrial technological processes, as well as to avoid changing the direction of flow of the working medium. In contrast to safety valves, safety devices eliminate emergency situations without discharging the working medium from the pipelines, acting only on disabling the movement of the working medium. Such devices include check and shut-off valves.
- Distribution and mixing. Such valves are also called three-way or multi-way. For example, it includes three-way valves and distribution valves. Apparatus is used for mixing media or distribution of workflows in directions.
- Control. It is designed to control the level of liquid in vessels and boilers, it is used as a shut-off valve for instrumentation. These are different taps and valves for pressure gauges, test and release taps and level gauges.
- Phase separation. It is used for the purpose of separation of working environments that are in different states and phases. These fittings are, for example, oil separators, condensate and air tappers.
It should be noted that stop valves (valves, taps, valves) should be used only in two working positions - “fully open” or “fully closed”. Most of these devices are not intended to operate as regulating or throttling valves. Otherwise, it quickly fails: the saddles are erased, valve gaskets are deformed, the fittings become leaky, and can no longer keep the flow of the working medium in the locked state. Ball armature can be called an exception to the rule: its opening angle does not have such a destructive effect on density. For spherical devices, the most important thing in extending their service life is to clean up the used working medium from solid abrasive impurities that erase balls.
For drainage and purge systems of high pressures on each line use two shut-off devices located side by side. One of them (the first in the course of the environment) is considered to be shut-off, and the other - adjustment. During short-term purging of the drainage lines, the first of them opens the shut-off valve, and then the regulating valve. After purging, the valves are closed in the reverse order (first closing the control valve). This procedure ensures a long service life of the gate valve.
Gate valves are used in engineering and industrial pipeline networks. It can be water pipes, steam pipes, heating and sewage systems. Gate valves depending on the type of shutter are:
- wedge, installed on sewers and water pipes for various purposes;
- disk used for pipelines of large diameters and low pressures of the working environment, they are often called dampers;
- parallel (two-disk), characterized by high reliability, they are installed in a wide range of pressures from two to two hundred atmospheres and working environments with elevated temperature.
The valve is a locking device in which the movement of the shutter is due to a simple threaded pair. The flywheel rod is connected to the shutter or valve through the clamp. When the flywheel is rotated to open, the shut-off valve stem is pulled through the clamp. Often these devices are used as regulating valves, although they belong to shut-off organs. The fact is that it is not always rational to install costly control valves. Cranes are used in different areas, many of them are familiar from everyday life: they overlap the hot and cold water lines in the bathroom and kitchen, supply gas to the stove, water supply to the hose for watering the garden and other devices. They have the simplest design, but this does not make it easier to work with their repair.
By way of connection
According to the design features of the connecting parts, pipe fittings can be divided into two large groups:
- flange;
- flangeless
The specific list of flange-type fittings is limited only by the difference in the shapes of the flanges themselves.
They are:
- round;
- square (rectangular);
- triangular.
The most common fittings with round and square flanges. Other forms are rarely used or not considered at all when designing new production facilities. Square flanges are used for environments with limited maximum pressure values — no more than twenty atmospheres. The main form of the flanges remains round: it is less labor-consuming in terms of production, and in terms of reliability has a tolerance for both low pressures and high pressures.
The range of flangeless fittings is more extensive in terms of the difference in the methods of its connection to pipelines, branch pipes of vessels and tanks.
This includes fittings:
- welded;
- coupled using couplings;
- choke;
- tsapkovaya.
It should be noted that all the above-mentioned types of connections of locking devices with pipelines, except for welded ones, are detachable. The fittings attached by welding, for replacement or repair, will only have to be cut using a “grinder”, a gas torch or a hacksaw for metal in domestic situations. In the choke, coupling and pin fittings, a thread is used to fasten the connecting elements.The tightness of the joints of flange locking devices provide flanges with gaskets or sealing rings laid between them. There are some other devices to improve the tightness and strength of flange connections (protrusions, chamfers, spikes and ring samples).
Materials and components
The materials used for the manufacture of valves and components must comply with the general specifications according to the standards of the Central Design Bureau of Valve Industry (CKBA) “Pipeline valves. General technical conditions, entered into force since January 2006, as well as applicable national standards and industry specifications. The main criterion in the choice of material for the body of any valve is its strength. The housing is the basis for installing all other parts into it. It is like a foundation in construction - the supporting structure for the whole building.
The housings of most pipeline locking devices are made of cast iron or steel. Other metal materials are sometimes used for this: bronze, copper, aluminum and brass taps and valves for household appliances are found on the market.The armature of non-ferrous metals and their alloys has a good feature - it is not subject to corrosion and has a good appearance.
The most economical material for reinforcement is plastic, which unites products from PVC (polyvinyl chloride), polypropylene, polyethylene and other artificial alloys of plastic material under its common name. But such fittings can not withstand high pressure and temperatures, as it does not differ in strength. But for pipes of small diameter and low pressures, this is quite a suitable alternative to metal products. In addition to low cost, pipelines and plastic fittings are valuable for their resistance to corrosion - the main scourge of the same type of steel devices.
Ductile, gray or high-strength cast iron is used for casting reinforcement housings, depending on the area and conditions of use of a particular product. The fittings with a cast-iron casing, due to their brittleness, are not used at high pressures in pipelines, as well as where the occurrence of hydraulic shocks and sudden temperature changes. In such situations, the cast iron housing can simply burst.
Steel hulls are made of various grades of steel: alloyed, heat-resistant and carbon. For the manufacture of valve bodies installed on pipelines with aggressive substances or having a particularly clean working environment, stainless steel with high corrosion resistance is used. Cases of heat-resistant steel are used for fittings operating in conditions of elevated temperatures of the working environment. The use of this or that material, as well as the design and type of flange are due to a number of factors, the main of which are as follows:
- nominal diameter of pipelines;
- working pressure;
- flow direction;
- temperature conditions.
Shutter valves are often made of the same material as the body, but more often it is made of another metal, based on high wear resistance and the parameters of the working environment. The material of the sealing surfaces must ensure the tightness and durability of the valve.
Sealing material are:
- metal products in the form of rings, possessing corrosion resistance, antifriction properties, well-treated (steel, brass, bronze, monel);
- fusion of various hard alloys: stellite (cobalt alloy), sormate (iron-based alloys);
- non-metal products (rubber and rubber rings, polymer seals);
- packing gaskets of plant material (cotton and linen fiber), talc, fiberglass;
- Teflon and graphite for packing seals under aggressive and high-temperature working environment;
- sheet rubber, paranit and ftoroplast for laying.
Pig-iron and steel fittings fitted with flanges have indisputable advantages in terms of tightness, maintainability and strength of the pipeline network compared to flangeless ones. But the weight and dimensions of such reinforcement sometimes reach large quantities (in tons and a few meters, respectively). To this still need to add control devices (handwheel, electric or pneumatic actuators, mounted on the valve). Flanges lead to increased consumption of metal and labor intensity in their manufacture.
Replacement and installation
The process of installation or replacement of valves should be approached responsibly.There is a wide variety of such valves, differing from each other in appearance, arrangement of the closure mechanism, method and mechanism of control, and features of installation on the pipeline. It is necessary to choose a locking device suitable for this type of pipeline, such a working medium and such its parameters. And also make sure that the locking device can be installed from the point of view of connecting devices. Pipelines and fittings to them must match each other according to the following indicators.
- Equal section shape. A round pipe needs a reinforcement having a circular cross section. This form of valves and other types of fittings is predominant. Pipelines of rectangular cross section are found in ventilation systems and furnace business, where slide or plate valves are used.
- Same diameter. The diameter of the locking device must be fully consistent with the diameter of the pipeline to which it is attached. The passport data of the valve, valve, regulator and pipelines always contain information about this. In addition to the passport (instructions), the data on the diameter of the device is applied to the body of the product in accordance with the requirements for marking the valve.For example, the label indicates Dy = 150, which means that such fittings are suitable for a pipeline with a diameter of 150 mm.
- Pipeline connecting parts and installed locking devices have all the possibilities of their reliable connection. This includes: the identity of the flanges in shape and size, the coincidence of the mounting holes, the diameters of the threaded connections, the correspondence of the external thread of the fastened fittings to the internal thread of the coupling, cap nuts, and the like.
You should know the basic rules of installation or replacement of valves on pipelines, without which it is impossible to do and even begin work.
- Any repair or installation work is performed only on the disconnected section of the pipeline, in which there is neither a working medium, nor residual high temperature, nor pressure. Drainage and air vents on the line are open, and on the disconnecting valves on both sides of the disconnected repair area hang safety signs, precluding their erroneous opening.
- A pre-assembly preparation of the fittings of the fittings and the pipeline is carried out: they are cleaned of possible dirt and rust, and the welded joints are brushed to the surface of the metal and prepared for conducting the weld.During cleaning, you need to pay attention to the absence of any hidden defects flanges, cracks, shells and other flaws that prevent the continuation of work.
- Installation of fittings should be made only on flat and straight pipe sections. It is unacceptable to install it on bends, as this will reduce the tightness of the connections.
- For heavy valves and valve elements, additional support structures and rigging devices should be provided in order to avoid accidents during the performance of work or breakdown of devices and sealing elements.
- The bolts and other fasteners are tightened using a special tool. Tightening the studs of the flanges should be uniform and according to this rule: the nut is tightened at one end of the flange, and then at the opposite, so that the flanges do not tilt.
- Welding works are performed only on valves, in which the valve is in the open state.
Such sections may be, for example, jumpers between two and a large number of lines with the same substance in pipelines. When connecting these sections during operation, the valve is fully opened first.the direction of flow in which is opposite to the expected, and then carefully open the second device corresponding to the direction of the medium. Here are some more important recommendations that are useful when replacing or installing certain types of fittings.
- All fittings intended for installation must be audited in advance for tightness and adjustment of all internal devices.
- In flange connections, periodically you need to tighten the fastening bolts. Immediately tighten them strongly can not, because you can pull the connection, as a result of which will become useless gaskets.
- When mounting the rotary valves, slightly open the valve disc.
- For a tight connection of ball valves, you must use special tapes wound on the thread of the joints.
- It is better to install the locking devices in such places so that there is always free access to them for quick disconnection, control, inspection and repair.
When installing, pay attention to the fitting of the valve to the direction of flow of the medium. On the cases of valves, valves, taps and other locking devices in recent times, the arrow indicates the direction of working environments.For pipelines, where the possibility of two-way flow of liquid, steam and other substances with high pressure is provided for, two stop valves with different directions of the working flow should be installed.
Welding works on fittings and pipelines should be performed only by experienced specialists. Independent attempts to weld cranes, valves and valves, as a rule, end up with poor-quality results and constantly arising problems in the places of welding (fistulas, cracks). And the look of such “homemade” leaves much to be desired. But to change the faucet or faucet in the bathroom - this is the real owner can take without fear.
Review the installation of valves in the next video.