Subtleties of fittings selection and methods of connecting PND-pipes
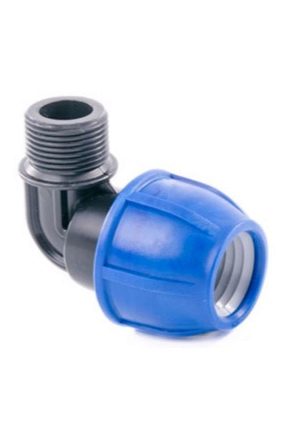
Polymer pipes are often used both in industry and in the installation of plumbing systems in private construction. Their popularity is due to ease of installation and low price of products. The reason for such a low cost is the limitation of the working temperature of the PND-pipes to 65 degrees. Nevertheless, the supply of both cold and hot water to a house or apartment is almost always done with their help; therefore, the connection of such pipes is a rather urgent question.
Special features
In addition to the installation of pipelines, the performance properties of PND-pipes are reflected in the following applications:
- protection of electrical cables and cable communication systems laid in the soil from corrosion;
- the formation of a waterproofing layer for various materials - concrete, metal, wood;
- installation of irrigation and sewage systems, as well as gas supply.
Their high popularity is also connected with the fact that it is possible to connect pipe segments to each other in several ways, which makes them practically universal.
Kinds
There are several classifications of such connecting elements for HDPE systems. The main one is the classification by the method of their installation. All connections of PND-products can be divided into two types: one-piece and detachable.
Permanent joints can be created with or without a fitting. However, the connection without an additional element is less reliable and durable, therefore it is practically not used.
All-in-one
Such connections are rarely used and are performed using special welding, performed either as a conventional butt joint or using an electric coupling. In the first case, with the help of professional welding equipment, the ends of the cut products are heated to a soft plastic state, after which they are pressed against each other and cooled in this position until hardening.Such a connection will be strong only if the lengths of the two pipes to be joined are not oval, but have a circular section.
To work with electrofusion also need special equipment that will heat the coil located in it. Cut-off pieces of pipes are inserted into both coupler outlets, the coil heats up and melts their connected edges. After the helix cools down, the heater is disconnected from the sleeve, and it is left as a connecting element protecting the seam.
Thus, the welding of PND-products can be performed end-to-end, socket welding with a fitting, using a press (edge welding) and using electrofusion.
Detachable
Most often for connecting products from HDPE use detachable fasteners. This is done by the method of socket combination with the help of elastic polymer seals. This method can be used exclusively in non-pressure pipeline systems.
For pipes in which water is supplied under pressure, various fittings are the ideal connection method. Their use increases the lifetime of the entire system, its reliability and resistance to temperature extremes.Fittings are universal and resistant to the conditions of various corrosive environments. They are used both for connecting hoses with the same internal diameters and for different sized products.
The connection itself may be different.
- Flange. In this case, the brass flange or cast flange is connected to the pipe by welding. Most often they connect pipes of different materials or wide pipelines.
- Collapsiblewhen one end of the pipe enters the expansion fitting on the other pipe. Properly connected systems are the most reliable and pressure resistant.
- Threaded. With such a connection on the pipes and fitting, they pre-thread the thread with a special tool. Only systems with low pressure can be connected in this way, as this is not a very reliable method.
Given the stiffness of the material, there are flexible and non-flexible compounds made of metal (brass, steel, cast iron and copper) or polymers (polypropylene, plastic, polyethylene and PVC). The diameter of the hose mounting method is divided into the connection of pipes of the same size and different.
In addition to the method of connection, components for PND-pipes are divided into the following types.
- Welded. Such elements for the PND-systems are produced either by the method of casting (cast fittings), or by conventional welding of short pieces of pipe (welded fittings). Such welding is called butt welding. The diameter of the elements ranges from 63 to 315 mm.
- Electrowelded. In essence, such fittings are just thermistor couplings used where ordinary welded joints cannot be arranged or they are not reliable enough. One of the features of such electrowelded elements is the ability to work without moving the pipe and create separate tie-ins into the system. They can be used to connect hoses of different diameters, as fittings are available with many different diameters. They are not only in the form of ordinary couplings, but also in the form of tees, taps and plugs with both small diameters of 20, 25, 32 mm, and for large systems with diameters of 800, 900 and 1200 mm.
This type of product is widely used and is used for the installation of any branches and plugs that exist. Most often they are installed in gas supply systems or for liquids with the highest temperature of 40 degrees.
- Compression (crimp). Such detachable fasteners are available to combine pipes without welding. Compression elements consist of a polyethylene rigid or flexible body with sealing rings at the ends, clamping connections, the pressing bushings and caps-nuts. The dimensions of such fittings start from just 16 mm, and end with a standard diameter of the riser line - 110 mm. Typically, when installing plumbing and sanitary use fittings with a diameter of 50 mm, as the inlet and outlet pipes of this diameter are installed in most houses and apartments.
In addition to all the above classifications, the fittings themselves are divided into several types, depending on the role played in the water supply system or sewage system.
- Caps - for permanent or temporary closure of the path to the flow of water and gas.
- Collars compress and fix a pipe.
- Tees or crosses - for the device of branches from the main pipeline and connections of additional devices.
- Couplings - elements of connection of two pieces.
- Adapters - for assembling pipes from different materials into one system, for example, HDPE with metal.
- Bends are needed for the angular rotation of the pipes and change their direction. Standard angle bends are available with angles of 45, 56 and 90 degrees, and if necessary, a different degree of bending, they are made to order.
- Babies are used to create branches.
- Lining the new pipes into the system, previously mounted.
Installation
Of all the types of compounds of polyethylene parts for installation on their own most often choose compression fittings. The choice of this type of component is associated with the lack of expensive equipment for their installation. Connect all the details of this mount just need "bare hands".
The installation process itself is as follows.
- Pipe trimming. The polyethylene pipe is cut with special scissors at a right angle. Edge must be cleaned of all burrs and rounded. A special label is applied to the surface of the pipe, which indicates how deep the pipe should be inserted into the fitting socket.
- Parsing analysis. Before inserting the pipe ends into the polymer connector, it is necessary to loosen and remove their plastic caps. It is strictly forbidden to put the assembled fitting on the end of the pipe, as the parts will be connected incorrectly and there is a high risk of leakage.
- Compound. The end of the pipe is lubricated with ordinary soap or moistened with water, and the nut removed from the fitting is put on it. A compression sleeve is placed on the tube. The clamping ring of white color is installed so that its thick part is directed to the pipe, and the rubber ring can be either placed in a special recess of the fitting, or put on the pipe itself.
The pipe is inserted into the body of the fitting, the ring and sleeve are moved close to it. The clamping nut is twisted first by hand, and then tightened with a special tool. After installation of all the connections, it is necessary to check the system by pumping water under the maximum allowed pressure.
Tips
Installation of plumbing using PND-pipes is quite simple, even beginners can build a simple water supply system on their own.
However, there are some common mistakes that are best known in advance to avoid them.
- You should not buy products from different materials. Water supply hoses can be made from polymers of different types, which will reduce the tightness of their connection. As a result, it is possible to get a crack or leak near the fitting.
- A mistake is both an excessively strong tightening of the nut, and a weak fixing thereof. In the first case, it is possible not only to disrupt the thread on the product, but also to obtain a microcrack of the case, imperceptible at first glance. After water supply to the system, such a crack will begin to expand, and the body of the fitting will eventually burst. In the second case, the waterproofing ring will be loosely pressed, and water may leak over the edge of the joint.
In household networks usually put the most inexpensive option with manual control. Nevertheless, devices with a gearbox are also widely used, making it possible to ease the manual force when changing the position of the lever. With a trunk width of 150 mm and more, only mechanical drives are used and they do not manually overlap them.
- When using the welded method of joining HDPE products, their edges need to be adjusted very smoothly. It is best to buy an inexpensive end cutter for this, which will allow you to align the edges of the cut pipes as smoothly as possible. As a locking device in the PND-systems is best to use ball valves. Most often, they are selected in the same design as the rest of the system fittings (plastic, polyethylene, brass or steel).
- In order to have complete confidence in the tightness of the finished system, it is necessary to choose pipes and fittings of the correct diameter and good quality. Preference is better to give a little more expensive, but high-quality European manufacturers or famous domestic companies. Properly assembled and first-tested system will serve for a long time without breakdowns and replacements.
You will learn more about the types of fittings for PND-pipes and methods of their installation in the following video.