Pipe benders for profile pipes: design features and independent production
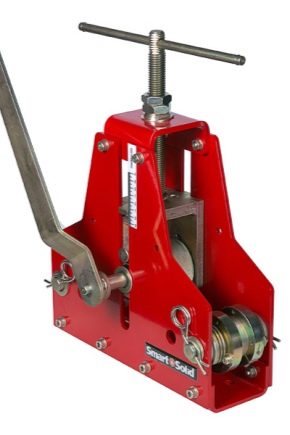
The pipe bender is a special device of manual type or a production machine designed to bend a pipe of various materials at a certain angle. Serial devices differ in the principle of operation and may have different types of drives, but to work on any of these devices requires some experience.
You can use aluminum, chrome, copper, ordinary and stainless steel or plastic pipe with a diameter of from 5 to 1220 mm or a profile with a different section. Bending angle - up to 180 degrees.
Device and purpose
Rectangular, oval and square pipes in section are called profile. This machine can be made by hand, purchased in a store or on the market of building materials. In this article we will look at how to make such a device with your own hands.
In the manufacture of a canopy, a greenhouse frame, a canopy, metal furniture and other structures, it is preferable to use bent-shaped pipes, since such pipes have flat surfaces, making it convenient to mount the roofing material. In living conditions, it is not easy to bend the pipe without deformations and creases.
Therefore, a pipe bender is used. In most cases, this device is equipped with a hydromechanical or electromechanical drive. With its help it is possible to bend the pipe under any degree. For the manufacture of parts, you can bend pipes on special production mechanisms. But considering their high cost, it is better to assemble a pipe bending machine with your own hands at home. Assembly is made from available and frequently available materials. Lightweight construction does not take up much space in the garage or in the yard.
The main parts used for such a machine are the shafts (rollers), the lever (jack), the drive chain, the hydraulic cylinder, the axis of rotation, the frame for the device. The frame can be closed and open. The main component of such a device is considered to be the hydraulic cylinder that performs the power role. The principle of operation of a homemade pipe bender is always the same - the workpiece is placed on the roller stops, and in the middle is a stop roller, which exerts pressure on the pipe, bending it to the desired radius.
The rollers establish cylindrical or grooved, which depends on the size and shape of the workpiece. For a wide and flat profile, smooth rollers are convenient to use, for high and narrow rollers with a groove guide are required. More in demand universal rollers. When necessary, guide rails are attached to the tubular base. This mechanism requires the expenditure of physical strength. In order to facilitate the work of machines equipped with hydraulic drives. In addition, they are equipped with an electric gear motor (single-worm worm). The choice of the type of gearbox depends on the diameter of the pipe. Such additional installations make it possible to perform bending.pipes with a large diameter.
Principle of operation
The bend of the profile pipe occurs according to the principle of rolling or rolling. To bend pipes of small section, simple methods at hand can be applied, which do not require the creation of a complex mechanism.
These include:
- Filling with sand. The inside of the prepared pipe is filled with fine sand, previously dried and sifted. Holes on both sides are closed with traffic jams. Further, the pipe bends in a pattern of the desired shape. If necessary, the place of the fold is heated with a blowtorch or a gas torch until reddening. This method is time consuming, has a low quality and low accuracy.
- Filling with water. To bend a profile with water, it must first be frozen. The pipe is sealed at one end with a stopper, filled with water and placed in the cold. In no case should both ends of the pipe be closed with a stopper so that when the ice expands it will not break the pipe. Next, the frozen profile is bent using a template. This technology is well suited for thin-walled copper and aluminum pipes.
- Spring. In advance, a spiral is curled from the metal wire, the dimensions of which are 3-5% less than the internal profile section. The spring is placed inside, and after the pipe can be bent in a simple way using a template.After completion of the work, the spring is removed, leveled, and it is possible to reuse it.
- Welding, cutting. This method is used if the bending radius is minimal and the pipe is thick-walled. From the inner side of the intended bend, according to previously produced geometrical calculations, segments are cut with the help of a grinder. The pipe is tilted to the desired radius, and the connected sides of the cutouts are welded using a welding machine. For aesthetic purposes, the weld seams are ground by a grinder.
- The simplest design is pipe bending using a template. This method is intended for the manufacture of blanks of the same type in large quantities. For the manufacture of such templates use wooden boards with a thickness of at least 2-3 cm. Limiters (sides) of any material are installed along the edges of the finished sample so that the profile does not slide off during work. Fixing the system to the floor or any plane, determine the emphasis for the metal profile. Having built it between the anvil and the template, gently press on the opposite end, ensuring uniform pressure across the entire plane.In order to facilitate the pressing of the pipe, an additional lever, a winch is used. This method is suitable for a profile with a diameter of not more than 1 inch. When using a larger profile instead of a wooden template, reinforcement blanks are used, maintaining the desired radius, they are fixed in a concrete base.
The advantage of this method is its low cost and ease of work, but the accuracy and quality of workpieces during processing will have low rates. In addition, you will need to produce a new pattern every time you need to bend a different radius. This option is well applicable to bending aluminum and copper pipes.
The methods given above operate with the help of muscular strength; therefore, they are used only for thin-walled profiles of low strength. For pipes of larger cross section, special machines with an electrical mechanism are needed. But this does not mean that it is necessary to buy a production machine without fail. Manual gear is easy to assemble yourself.
Types of machines
According to the requirements of operation, there are fixed (stationary) and manual machines.Stationary structures are used to a greater extent in factories. A hand-made device made with your own hands is more suitable for domestic work.
Depending on the drive, there are several types of pipe bending devices:
- Hydraulic (hydraulic jack applied). There are stationary and manual. Bend pipes with a diameter up to 3 inches. Such machines are used in special industries and can carry out an impressive amount of work.
- Mechanical. The pressure is formed manually using the main screw or lever.
- Electric. Bending occurs at the expense of the electric motor), suitable for bending of any pipes - both with thin and with thick walls. Thanks to the electronics, accurate calculations of the bending angle are made. Such pipes have no deformations.
- Electro-hydraulic. The hydraulic cylinder is powered by an electric motor.
Pipe bending machines according to the ability of pipe bending are divided into mechanisms operating with pipes whose diameter is up to 16 mm, 20 mm, 32 mm, 50 mm, 76 mm.
To bend the pipe in various ways.
In this regard, the benders by the method of bending is divided into:
- Segmental.They are supplied with a special device, which simultaneously pulls and bends the workpiece at the right angle around the segment.
- Machine crossbow view. Equipped with a special mechanism consisting of a bending component.
- Spring devices. Equipped with springs. On such machines it is possible to handle metal parts.
- Sod. Consists of a guide, which is placed inside the pipe before starting work. Such an element with a mandrel protects the part from deformation and flattening. This machine is used in the manufacture of automotive pipes and for bending aluminum pipes.
- Lint free Bending is performed by winding the part on the bending roller.
The length of the workpiece, which must be bent, use devices of two types:
- lever machines;
- rolling devices.
Lever-type devices are considered to be the most common. Also available in industrial production are turf and crossbow pipe benders. The principle of operation of such machines consists of two guide rollers and a pressure gauge (mandrel). Such a mechanism makes it possible to carry out cold processing of round metal pipes in small areas.Due to its small size, the crossbow bender is considered to be the more common device among professional installers of technical communications. The device got its name due to the fact that the design is similar to a crossbow.
But this kind of method leads to a pipe to a fair stretch along the external radius of the bend, which affects the reduction of the wall thickness and its rupture. In particular, the crossbow method is not suitable for bending thin-walled pipes.
For the production of a significant number of monotypic parts of small radius of bending, it is possible to use a pipe bender-snail. This unit consists of two pulleys (wheels) of different diameter, fixed on the shafts. By securing one end of the tube to the wheel, a roller of the smallest diameter (main wheel) pressurizes the workpiece, while at the same time rolling the roller over the part being processed. Because of what the pipe is bent along the surface of a large pulley, acquiring its shape. The only drawback of this method is the impracticability of extracting curves of a larger radius.
Practical and versatile in the work are rolling (bending) machines, hand-made, in which you can adjust the angle of deformation of a metal pipe. The simplest system of the rolling machine consists of a base and a drive shaft fixed on it, located at a certain distance from each other. The pressure is exerted on the pipe by a movable roller, and its pulling is performed by rotating the main shafts. When creating small radius bends, you will need to complete 50-100 runs. To avoid deformation, you should roll the product with the same speed. Assembling the rolling mechanism independently in the domestic environment will be difficult, as turning and welding will be required.
Necessary tools and materials
First you need to develop the correct scheme (drawing) with accurate measurements and the necessary materials. Before you assemble the machine, we determine which profile bend radius will be more necessary. On the basis of this select the size of the impeller.
In drawing up a drawing of a homemade machine, you must adhere to the main rule - strength and lightness of construction. The following power tools will also be needed: a welding machine, a screwdriver, a Bulgarian, cutting and grinding wheels, a hammer, a vice, a drill.
Construction scheme
It is possible to construct a hydraulic machine for point bending from 2 parts of a channel, 4 angles and 2 parts of fingers from a tractor track. The deflection of the pipe provides the usual hydraulic lever (jack) with a force of at least 5 tons. A metal “shoe” is mounted on it. It can be ordered and purchased from a turner or made the most of the old pulley. The width of the "streamlet" should correspond to the latitude of the profile. Cutting off half of the pulley and drilling a socket in it for the jack rod, we get a hydromechanical drive system. The base of the homemade machine is 4 corners (shelf 60-80 mm), which are attached to the metal plate. Two channels are welded to the upper corners synchronously. Holes are symmetrically drilled in the channel walls to regulate the bend angle of the blank.
Such a machine is very easy to use. In the holes in the channel are placed 2 metal fingers and put on them rollers stops. The jack with a shoe is raised in such a way so that a profile can fit between it and the stops. After installation, the pipes act on the jack handle, forming the desired bend.
The pipe bender can also be designed with your own hands. To build it, you will need two linear meters of the channel (wall level 15-20 cm), which will be the rack and the base. For rollers, you can use 6 small pieces of metal pipe, which will serve as a holder for bearings. For this reason, the internal size of the pipe must correspond to the external value of the bearing. After the turner makes shafts for bending rolls, proceed to the assembly of the bed.
Due to the rotation of the handle attached to the shaft of the intermediate stop, bending of the profile tube is performed. It is possible to set the bend radius of the profile using the tilting of the swing channel and the rollers located along the edges. For this purpose, the rolls are not welded to the frame, but are made sliding. Hydraulic jack can be replaced by car.
For the simplest machine will require the following elements:
- jack;
- strong springs;
- steel profiles for frame assembly;
- rollers (shafts) - three pieces;
- drive chain.
Next, collect the device. We install a strong frame, the parts of which are joined by welding or bolts. According to the drawing, set the axis of rotation and rollers.The shafts are fixed in such a way that the two outer shafts are located above the middle one, forming an arc. The distance between the rollers determines the bend radius of the profile pipe. For the operation of such a mechanism, a chain transmission is used, which consists of three gears and an old chain (spare parts from a car, motorcycle or other equipment). To bring the entire assembled system into action, you will need a handle that attaches to one of the rollers (shafts) and creates the required rotational force.
The machine for bending the profile pipe can also be created by hand. For this mechanism, the bed consists of a channel with a length of 77 and a height of 10 cm.
We assemble the construction according to the instructions:
- From the metal strip with a width of 5 millimeters 4 main stands are cut for small shafts, the profile will move along them. In the upper end lobe cut out the opening for the axis of rotation of the rollers. The size of racks - 5 * 10 cm.
- Racks are fixed to the channel with a welding machine, keeping a distance of 30 cm. Rollers for shafts can be found on the building materials market.
- Next, a plate under the machine is cut from a metal sheet 8 mm thick. The size of the plate is 25 * 25 cm.A central roller is placed on the plate, by rotating which the profile will move.
- At the ends of the plate are placed strips of wood with a width of 10 millimeters, which are attached with superglue. So that when turning the roller does not catch the plate, we need these supports.
- To install the roller, you will need 2 bearings, in the depth of which the shaft axis will rotate. The bearings are fixed with the help of bolts in the openings drilled from the inside of the supports.
- Then it is necessary to make 4 stands of 40 cm in length, using the 50th corner, and fix them on the edges of the plate with the main shaft by welding, securing it on the machine station (channel bar). The plate is placed in the central part of the pillars, keeping a distance between the axes of the rollers, equal to the size of the profile with which you plan to work.
- Plugs are cut out of 8 mm metal sheet, their welding is attached to the upper fragment of the racks. Then you need to make a plate under the cover of the machine, in which the adjustment screw is installed. From the inside of the plate an opening is drilled corresponding to the diameter of the screw used.
- The plugs are drilled openings for bolts (10 mm in diameter) and the cover plate is fixed in the racks.
- A thread is cut into the opening in the lid and the heel is screwed in, in the middle of which the clamping screw rotates.
- A 15 mm corner is welded to the plate, which is an external screw stop. In the corner under the screw is drilled aperture, synchronous axis of the heel. A proper thread is cut in the opening.
- It remains to attach the handle for the main shaft and fix it to the axis of the roller. The handle can be made from the valve from the shutters or a piece of reinforcement of the desired length.
Assembly technology
In order to protect the assembled structure from moisture, it is covered with a special solution that will protect against rust, and then painted. In hydraulic machines it is possible to carry out the bending of a shaped pipe of various materials and thick-walled products. Carry out a similar procedure possible cold and hot (pre-heating pipe) method. The purpose of the hot method - the pipe is heated outside or hot air is passed into the pipe, which increases its plasticity, respectively, the bending quality indicators increase. Cold - this method is simple, it is used for plastic pipes.
Before bending, such pipes are filled with salt, oil, sand, water, which makes it possible to produce the most high-quality bend without significant damage to the pipe.
Useful tips
- Removable rollers of various types will provide an opportunity to work with both the shaped tube and the round one.
- In order for the bending mechanism to be the most multifunctional, the thrust rollers should preferably be made mobile. Due to this, it is possible to change the radius of the pipe break.
- If the bending is carried out using a template, then in order for the pipe to fit snugly to the sample, it is possible to use iron hooks for the stop.
- If the profile pipe must be bent under the largest radius, then it is more correct to use a three-roller pipe bender.
- It should be remembered that at the place of bending the profile loses its strength. For this reason, if angles closer to 90 degrees are used, it is more correct to cut the pipe and, using welding, give it the desired bend angle.
- A detailed instruction manual is attached to each factory machine, in which all characteristics and technical data of the device are indicated. In order for the machine to serve for a long time and without breakdowns, it is necessary to familiarize yourself with the instructions before starting work.
- Do not forget about personal protective equipment.During work with the grinder, it is necessary to use glasses or a safety shield, and to carry out welded cases in special clothes, gloves and welding mask.
In the next video you will find complete instructions for assembling a pipe bender at home.