The subtleties of the design and construction of houses from timber
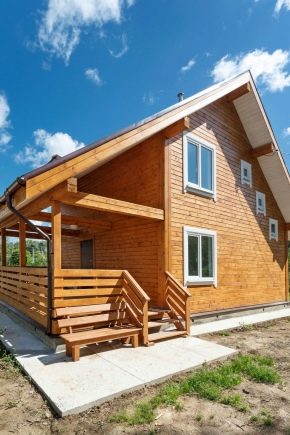
Recently, more and more residents of megacities are moving out of the city, someone for permanent residence, someone like a summer residence. As houses from a bar have a number of advantages, often they choose them for construction.
Special features
The construction of log houses has its own distinctive features. The main are the dimensions of the beam. Its length will be the defining value for the dimensions of the building. Example: glued laminated timber has a size from 6 to 18 meters, which means that it is necessary that the length of the wall corresponds to it. If the joints are made, then the partitions will lose their resistance and thermal insulation will deteriorate.The construction speed is achieved through calibration, which avoids fitting the bar to each other.
The basic properties and service life of a building material depend on the characteristics of wood.
- The soft structure of pine and its saturation with resins does not allow the timber to crack during and after drying. It is recommended for construction in humid climates. Dense structure is difficult to process, but it has its advantages. For example, spruce has a high bactericidal effect.
- Among the deciduous trees there are also representatives who will improve the quality of the timber. Larch is characterized by phenomenal strength, which under the influence of water only increases. Oak wood is durable because it does not rot. Lipa is good for building a bath, as it has a high coefficient of heat saving. Aspen not only is resistant to mechanical damage, it does not start rot and fungi, so it is suitable for the construction of wet rooms, such as steam rooms and saunas.
Types of materials
Sawing is the process of making a log from a regular round log. Sawing can be done in two ways, on which the quality class depends:
- radial, when the annual rings are located in the center;
- tangential, when the incision passes from the edge, so this timber is of lower quality.
After processing, you can get at the exit of 5 main types of timber:
- raw or planed;
- calibrated;
- profiled;
- glued;
- glued veneer.
Planed timber - one of the easiest and cheapest material options for building a house. A characteristic feature of a planed timber is that it must be dried well. It has standard dimensions and an unassuming appearance with some irregularities, therefore it requires lining. In order to build houses quickly and without additional fitting, a construction bar of the same size is required. This is called calibration.
Buildings made of calibrated material are reliable, practical and erected in a short time.
Ideally, annual tree rings should be located in the center and along the entire length. Conifers are considered the best wood for the production of timber. Larch and Siberian pine are considered among the leaders.The latter, as a rule, is harvested in winter. The beam of one batch must have the same dimensions: length, width, thickness. The material must be dried in natural conditions. Artificial drying is acceptable, but it increases the cost. Permissible humidity ranges from 12 to 22 percent.
Construction timber has different sizes and sections. During primary processing, the optimal diameter is 100x150, 150x150, 200x200 millimeters. Calibrated log serves as a blank for the production of other types of timber.
Profiled timber acquired the greatest popularity in the construction of low-rise buildings. At the heart of it is a solid massif of coniferous wood. It is characterized by purity, comparable with the eurolining. Elements have their own fastening system using spikes and grooves. Connections can be simple in the form of two ridges and complex with several slots.
The following advantages are inherent in the profiled bar:
- Sufficiently high degree of resistance to decay. Protection against moisture is achieved thanks to a precisely fitted fastening system, therefore the structure is reliably protected from rotting and mold.
- Castle connection does not allow the bends to bend.
- Small shrinkage ratio.
- Environmental friendliness.
- Resistance to temperature changes.
The main disadvantage is the mismatch of fasteners timber from different batches, which leads to an increase in the cost of purchasing material with a margin. It should be remembered that only large reputable manufacturers can guarantee quality. Otherwise, the benefits can turn into disadvantages. Deviations in size, poor quality wood lead to marriage during construction.
Manufacturers offer more than 100 varieties of profiled timber. Their common feature is only the presence of the castle connection system. The main difference and advantage of glued laminated timber from profiled is its size. In length, it can reach 18 meters, which expands the possibilities during construction.
A timber is obtained by gluing several planks, usually from two to five. After sawing the logs, the resulting boards are dried to prevent cracking during operation. Next, the details are polished. With the help of a hydraulic press and special waterproof formulations are glued. For strength, the boards are arranged in such a way that the fibers are arranged in opposite directions.The next step is profiling and calibration.
For the production most often used spruce and pine. The use of more expensive breeds is extremely rare, since it increases the cost and the substantial price of the product.
Glued laminated timber, like any material, has its advantages:
- High resistance to deformation allows it to be used when creating complex architectural forms.
- Low shrinkage ratio.
- Appearance that does not require exterior decoration of the facade. Even during long-term operation, the surface is not covered with cracks.
- Ease.
It should be noted the disadvantages that are inherent in this type of timber:
- high price;
- it loses solid wood in operational properties, for example, in microcirculation of air and moisture.
Glulam is good for fast construction. Since the period of shrinkage is small, construction work can not stop, and to perform consistently. Glued timber, depending on the destination, is classified as follows:
- For walls.
- For other designs. Bent details, window and door openings and floors are produced from it.
Glued veneer lumber - a new type of building material,which appeared on the market relatively recently. It differs from its prototype in ease, because it is glued together from lamellae. However, the length of such parts is insignificant - up to 6 meters.
Blueprints
A country house can carry different functions on which its size and occupancy depend. A small compact version is suitable as a summer cottage. For permanent year-round living are appropriate solid wooden cottages, which are based on logs or timber.
The first step is to develop a project at home. Depending on the requirements of the customer and his financial capabilities, professionals offer either to create an individual construction plan, or to save money and take advantage of a typical project.
The project must contain:
- a schematic layout of the interior;
- elements of the facade and roof;
- detailed drawings of each of the floors;
- types of materials indicating the place where they will be used.
Also included are plans for all communications and power grids. Small schemes can be made independently by hand. Prefabricated drawings better order specialists.
Architectural and construction drawings contain geometrical parameters of all internal and external parts, characteristics of structures and individual elements. The plan of each floor should show the placement of rooms, corridors, windows, doors, their sizes and area.
Drawings must be made to scale. This will help to visually determine the location of parts in space.
Separately, the project includes a plan for the roof truss system in several sections. It describes the shape, size, angle of the roof, the presence of windows, pipes and other architectural elements. Drawings of longitudinal and transverse sections of the whole house give an idea of the location of the stairs and floors.
Facade plans are designed to describe the appearance of the house from all sides. The constructive section of the project is represented by drawings of individual components of a house under construction. It discusses in more detail the features of the foundation, floors, structural parts in the form of stairs and spans. An important section in the project is engineering and technical, which concerns communication schemes. It contains a description of each system separately, with explanations of the calculations, indicating the specifications of the equipment used.
Space planning
To visualize what kind of house you want to build, you need to sketch it out by hand. Consider how you will move inside, which corridors will be comfortable and how much they need, how to arrange the rooms, where the doors will open, what function to which room is better to provide. Only after the customer has decided on his wishes, he can contact the experts. There are two options for further work:
- Development of an individual project. The result will be more expensive, but effective. The project will take into account all the requirements of the customer, location features, the presence of other factors.
- Selection of a typical project. The option is cheaper than the previous one. In addition, it allows you to see the final result in advance, since someone has already built it, to consider the design features, to evaluate comfort and appearance. In addition, a typical project allows you to build houses from a timber quickly, in one season, which will reduce the shrinkage of the structure.
Space planning is a necessary task that needs to be solved already at the design stage. First you need to determine the number of floors.This is important because the extra space will not be used, and the cost of it will go. If you have a small area, you can combine some zones:
- Kitchen, dining and living room. This is the most popular combination. You can arrange all these functions in the same room, or you can simply connect several rooms with a walk-through enfilade, so that residents can see each other and communicate, doing their own things.
- Living room, study and library. The zone has a more official look and is intended for negotiations, reception of guests, rest of the whole family.
- Sleeping, wardrobe and bathroom. The private area is comfortable as a separate area for adults, children or guests.
- Utility rooms such as laundry and dressing room, kitchen and pantry.
To make the house seem more spacious, designers advise using walk-through facilities.
This technique expands the space, adds air and freedom. In addition, this method will reduce the number of corridors. Almost any building has an attic space that can be ennobled and turned into a cozy and functional attic.
If a country house has a second floor, then its layout should be ergonomic.The fact is that there it will be necessary to conduct electricity, water, ventilation, which will require certain costs. However, if you correctly plan the number, size and location of the windows, you can fill the room with natural light. Good thermal insulation will save on heating.
Without a bathroom will not do any country house. As a rule, if the cottage is small and one-story, then one toilet and one shower are enough. If there are several floors, as well as if the house has a large area, it is better to provide several sanitary rooms.
Basement floors in log houses are usually stone, so they are cool. Most often they have storage rooms, storage space or recreation areas. For example, the base is great for billiards or sports halls.
Houses from a bar are easily assembled and provide an opportunity for creativity, since wood is an excellent building material. Various architectural reliefs are also laid in the design, for example, stairs or built-in wardrobes.
Standard planning rules:
- The division of space into zones.All the internal space of the house is conventionally divided into residential and business areas. Living, in turn, is divided into the premises of the daytime sphere and for night rest, each of which is additionally classified into adults, nurseries and living rooms. The day zone unites such premises as canteens, living rooms, verandas, halls, hallways, bathrooms, and gyms. The night zone includes bedrooms and lounges. The household area includes a kitchen, dressing rooms, storerooms, laundries, workshops, utility rooms, garages.
- Soundproofing is necessary for night zones.
- The smaller the corridors, the lower the costs.
- If the house is supposed to settle different generations of the family, then it is better to provide them with different rooms with separate entrances, and for communication you can equip a common living room.
- Rooms for the elderly and young children should be located on the first floor.
- The place for the fireplace is laid immediately, since it is necessary to build a foundation and a chimney for it.
- Entrance doors in a large house are better equipped in duplicate: one from the side of the street, the other from the inside of the plot.
- Stairs should always be lit, as it is a traumatic item.It will be better to place it next to the window so that natural light helps artificial lighting.
- If in the future it is planned to expand the area of the house, then it must be foreseen in advance during construction.
- Simple forms of the house and the roof will significantly reduce the cost of the project.
- If you properly orient the house to the cardinal points, you can use natural light and ventilation. So, living rooms in the northern regions are better to have windows to the south, so that the sunlight heats it. Business premises are appropriate on the north side, it is cooler there. Comfortable atmosphere in the bedroom and children's room at the eastern location.
- Bathrooms on different floors are more practical to build on top of each other, and on the first floor - closer to the kitchen. This will simplify communication.
- A built-in garage is appropriate in a compact cottage, since part of the technical communications can be brought into it without using the floor space of the house.
- Attic space should be used efficiently, especially for small buildings.
- The entrance portal must be equipped with a vestibule to provide air protection against cold air from the street.
Design
The design of the exterior and interior design of the interior is also laid at the design stage of the building. There are many typical developments that have been tested over the years. The overall design of the house is beginning to be thought through with a stylistic line that will be maintained in all interior spaces and outside. However, this does not mean that you can not deviate from the classical rules. Modern designers often use mixed interiors, the main thing is not to overdo it with the number of styles.
Mostly stylistic solutions for the house are similar to apartment buildings, however there are some preferences. For example, a house in the style of Provence or a chalet could not be better fit into the surrounding natural landscape. The most common variant of a compact house from a bar - with a mansard. It is a compromise when choosing between one-story and multi-storey construction.
Attic saves costs while increasing the usable area of the house. A lumber material makes it possible to carry out construction in the shortest possible time.
Professionals warn that the attic floor must be erected competently in order to preserve all its advantages.To do this, the project is laid roof material. If the attic is residential, the metal roof is not suitable. Metal heats up in the summer, rustles during rain and other precipitations. It is better to consider options with a soft roofing coating or use natural tile.
When installing roof windows in the houses of the timber there are some rules that must be strictly followed. Openings must be placed between the rafters. The number of window openings is also an important factor. If they are few, the room will be dark and will require more electricity. In the attic, steam and waterproofing is needed, which will help to avoid heating costs and make the room comfortable for living.
The interior design of the attic room depends only on the wishes of the owners. The functional component can be absolutely any. Most often, under the roofs are equipped with bedrooms, because here it can be made very comfortable. Designers use for this purpose modern solutions, textiles, wood. Well-built panoramic windows enhance comfort and add romance.
The second most frequently used option is the nursery version.The kids love this kind of solitude, which looks like playing a treehouse. Here, imagination has no limits, starting with the mechanism of descent and ascent to the design of walls and roof beams.
Also, attic space can be equipped for libraries, workshops, offices or dressing rooms. The most technically complex options are kitchens and bathrooms, but they are also feasible.
To increase the useful area of the house, it is not necessary to build additional floors, it is enough to build a bay window. It will not only expand the walls, but also give the home a presentable look. The shape of the bay window can be any, but for houses from a bar it is preferable to be strict with clear corners: rectangular, triangular or pentahedral. The semicircular variant cannot be realized without additional saw cuts, and this will break its strength.
Experts note that for the construction it is better to use glued laminated timber, because it can provide windproof and durable.
Panoramic bay windows not only decorate, but also fill the house with natural light. Designers warn that this stylistic solution is not suitable for all cottages.Bay window is appropriate in cases where the house has non-standard architectural elements: roof, entrance portals or front windows.
Features of log houses with bay window:
- This architectural detail reduces the overall rigidity of the structure, as it increases the number of corners. Experts advise for the strength to lay inseparable crowns on top and bottom.
- Increasing corners requires better heat insulation to avoid heat loss.
- If you plan to complete the glazing of the bay window, then you should take into account that it is better to install only half of the panoramic windows in the houses with permanent residence so as not to reduce the level of insulation.
Cottage type "chalet" is distinguished by the presence of a stone bottom. The house can not be entirely made of wood, because its style does not provide. Usually, the first floor is built of natural or artificial stone, and the upper floors are made of profiled or glued timber. It is permissible to use a brick for the foundation. Stone ground floor due to the presence of a stove or fireplace. In addition, it increases the period of use of a wooden house, because the timber does not touch the ground.High stone plinths provide protection against spring floods.
The roof is provided for a massive, duo-pitch with a large skid from one edge for a balcony or multi-level with a two-story structure. As a roof, use either natural tile or shingles. Since they are heavy, supporting truss systems must be massive. Open large balcony or shingles terrace - a prerequisite for such projects. All openings have simple rectangular shapes and sharp corners. Windows, as a rule, a lot, for this style is characterized by panoramic.
Finnish houses are representatives of Scandinavian architecture. They attract with their simplicity, brevity and practicality. The beam is the best suited for such buildings. The project provides a terrace or balcony, as well as a fireplace.
Technology works
The main difference in the houses of the bar - this is their purpose.
- For the construction of summer country houses, as a rule, use materials of small sizes. Experts recommend using a bar section of 100x100 mm, in rare cases - 100x150 mm. This size is sufficient to keep warm and to be comfortable for living in the summer, while at the same time minimizing costs.
- Cottage for permanent residence.If the house is designed to live all year round, then its construction should be approached more seriously. Here you should use the material section 150x200, 200x200 and more. Thick walls are needed to reduce heat loss during cold periods. After all the preparatory stages: measurements, design, calculations, the acquisition of materials, site preparation, you can start building a house.
First you need to decide on the type of base. To do this, calculate the expected load on the foundation, take into account the type of soil on the construction site, the presence of groundwater and their depth of flow. For the construction of houses from a timber most often use a pile or strip foundation.
The basis on piles will be suitable for any kind of soil. When installing piles, experts advise to apply the grillage. It will equally distribute the load and protect the building from uneven shrinkage, which will prevent cracking of the walls. Tape foundation professionals recommend building in houses with basements and cellars. In the case of rebar installation, all fastenings are done manually with metal knitting. Welding can not be used, because it increases the risk of destruction of the entire structure.
The next step is the construction of walls. The first crown is placed on support boards, which must be treated with an antiseptic, which eliminates the ingress of moisture on the timber. In order to protect the boards, from the ground under them enclose waterproofing. The most rational approach is to lay the first crown on transverse lags-slats.
With further installation of the crowns, it is necessary to control the flatness of the walls at the building level. For connection use pins or castle fixtures, available in the profiled bar. All seams and joints should be treated with moisture-resistant sealants and antiseptics. It is better to saturate the timber before construction with fire-resistant means to protect the house from fire.
Corner joints - an important point. There are several connecting methods, depending on the load and differing in strength and efficiency.
Without residue ("in the paw"). Three main types can be distinguished here:
- "At the junction." The easiest option that does not require additional training. Beam stack to each other ends. Mounts can be used: spikes, nails, staples. Disadvantages: low degree of reliability and tightness.For a residential house is not recommended.
- "Half a Tree". Fastening requires additional processing of the ends. They are cut down to half the thickness of the timber, forming grooves. When laying they need to be warmed. Additionally, you can fasten parts with dowels.
- With root thorn ("Warm corner"). This type of corner joint prevents the occurrence of drafts and wall displacement during house shrinkage. Bruce also requires prior preparation, and steam bath. That is, a rectangular spike is cut out on one piece, a groove is made on its pair. The spike is usually equal to one third of the thickness. The gaps when connecting hermetically insulated, the parts fasten the nog.
- With the remainder. Such corner joints have maximum reliability and integrity, but they are characterized by a greater consumption of wood during construction. The most famous view "in the bowl." In this case, special grooves are cut at the ends of each timber, which provide a locking connection. This type is simple to perform and ensures the strength of the structure during operation.
Fastener
For fixing parts when building a house from a bar, several options are used.The most common are wooden dowels. As a rule, they are made of birch. Such fasteners allow you to create a strong supporting structure.
Experts claim that for the erection of structures from a bar it is impossible to use metal brackets and nails, because during the shrinkage of the building large gaps can form.
The main rule when attaching the dowels is their staggered arrangement. For installation, it is necessary to drill a hole with a diameter equal to the cross section of the fastener in two adjacent crowns. After that, the nog is driven into it, connecting the two beams.
In order to compensate for shrinkage builders use special tools - screw jacks. They are additional supports that contribute to uniform shrinkage. When erecting a truss system with a sliding truss “foot”, a metal mount is used, one leg of which is attached to the rafter and the other leg to the wall bar. Thanks to the sliding system, the excess stress that occurs during shrinkage is removed.
For receiving window openings in a bar-shaped wall use two options:
- Cutting out. Less time consuming, but more costly method, because there is extra material. To this end, an opening of the required size is cut through in the already constructed solid wall. This method will provide more accurate sizes of windows and doors, because the cutting out is done after the building shrinks.
- Laying out. Openings are laid immediately when laying the walls. In this case, material is saved, but the dimensions of the holes after shrinkage can change significantly.
Arrangement of the floor in the log houses is similar to other wooden buildings. Lags are used for flooring. On the floors usually lay a two-layer coating. Rough floor is prepared using boards and plywood. Then fit the heat and waterproofing. Next comes the finishing floor. The ceiling, as a rule, is the final stages of construction and is being built along with the final finishing of the house.
The amount of material needed to build a roof depends on its shape. The simplest is the gable option, having a rigid frame of rafters. It can be collected on the ground, and then set on the house. On top of the rafters make crate, which subsequently mount the roof.After drying and shrinkage of the house, cracks are formed that need to be caulked. To do this, use a variety of heaters, both natural and artificial.
If the construction was used profiled or glued laminated timber, then as a finish it is enough to cover it with varnish or impregnation. In this case, the view of the wooden house will remain. In the case of using raw timber for finishing, any kind of materials will be suitable: siding, brick, facade tile, block house, eurolining.
Frame
The technology of frame construction has been used for a long time. Its main advantages are lightness and rigidity of the structure, as well as speed and ease of assembly. When choosing a foundation rely on geodetic and geological features of the terrain. Various factors are taken into account: the climate of the region, the weight of the structure, and wind loads. In most cases, choose between pile and strip base.
To avoid moisture pulling the wood from the concrete foundation, waterproofing is carried out.
Experts recommend using mastic from bitumen, but there is also a more economical option - roofing material.
If the groundwater lies shallow, then it is better to increase the insulating layers to two or three. The process of laying the floor begins with the floor. This is the first level of two layers of boards that must be treated with antiseptics. Boards have dimensions of 150x50 mm and are fastened with special pins. The second layer is laid in such a way that it overlaps the joints of the first row. Some builders use in this quality timber 100x150 mm.
Next, a strap is nailed along the perimeter along the perimeter, which is placed on the edge. Nails are driven in every forty centimeters. After installation begins lag, which are attached to the strapping with oblique nails, two from each end. Boards stuffed in increments of 40-60 centimeters. If the length of the lag is large, then additional perpendicular bridges should be installed.
Then you can lay the floor. There are several ways. One of the most economical - with expanded polystyrene. This is the only material that is moisture resistant and does not require laying a subfloor. The remaining methods involve a double-layer floor with thermal insulation. Rough surface is made of boards, then comes a layer of insulation plates, after finishing the floor of plywood or planed boards. The walls can be assembled in two ways:
- Ballun The method proposes to use the technology of gradual erection. The frame is erected in place, starting with the bottom trim, corner posts and subsequent intermediate trim.
- Platform. Building blocks, when part of the wall is assembled on the floor, and then attached to the base. The method is characteristic of the factory construction of frame houses.
The supporting legs of the frame are arranged with a certain step, which is better to choose depending on the width of the insulation plates. The distance between the supports should be less than the size of insulation by 2-3 cm to ensure the necessary sealing and the absence of gaps. As fasteners for racks use pins or cuts. In the second variant, the lock fastening is carried out by cutting the stand into the trimming board at half the thickness.
For the geometric evenness of the walls and for their reliability, diagonal braces are used, four on each support: two at the top and two at the bottom. The thickness of the beams and the distance between them depends on the upper level. If you plan to build an attic floor, the step is shorter, the section is larger. In the absence of residential premises - on the contrary.
Beams are attached to the upper trim in several ways:
- On steel brackets.
- On the metal corners. The most common method. Manufacturers offer both conventional and reinforced fasteners.
- With a sidebar. In this case, the overlap beam is filed to the edge at ½ the depth of the top trim and secured with two nails or pins.
If there is a residential floor above, the floor is immediately sheathed with a subfloor. For a frame house, a gable roof is most often built. Unlike the log house, the roof should be lighter.
The modern building materials market is replete with various proposals for thermal insulation. The most famous and popular are basalt wool, cellulose fiber ecowool, polyurethane foam, foam plastic and others. If you plan to use mats of mineral fibers, you should consider their hydro- and vapor barrier.
Tips and tricks
- Before building a house, take care of all regulatory papers. If there is a land tenure agreement and a positive report to the geodesic company, the local administration issues a permit for the development of the territory of the site.Only then can the development of design estimates be started with the involvement of firms licensed to carry out such activities. Everything should be made to the project, an independent change in the details of the project will then be impossible.
- When building a house, the defining characteristic is the quality of the timber and the wood species. The most suitable option is building material from larch, spruce or pine, sawn in winter. When choosing, pay attention to the percentage of moisture bar. The optimal indicator is 15-22%. When buying a bar, ask the seller for regulatory documents and read them carefully in order to purchase material that is safe for health.
- Be sure to process parts with flame retardants and antiseptics. This will increase safety and durability. For prevention, treatment with sealants must be repeated every year before the fall and before the spring, paying particular attention to joints and seams. Every five years it is necessary to update the color of the walls. Once every four years it is recommended to apply a new layer of antiseptic. However, it is necessary to conduct an audit of the house for signs of the appearance of rot and fungus annually.
- The best time to build is summer. The offseason is only suitable if the forecast does not promise heavy rains. Keep the cant correctly. It is better to store it under a canopy, but if this is not possible, then cover it with plastic. You can not keep building materials on bare ground, you need to use pallets.
- Carefully read the service agreementif you hire a contractor for construction. It is better to negotiate with a well-known proven company, even in the case of a more expensive cost. A proven company will justify the investment and will give a guarantee, while a less cheap and unknown company may give a surprise. In the construction of the house, the mistakes are fatal, since many can only show up after the house shrinks after a long time. It will be too late to fix some.
- Experts do not advise spending money to fill the foundation. Since the log house is rather light, it is better to limit it to a pile variant or a tape base. When installing piles use screw options. This will facilitate the task. Do not forget that the supports should be located around the perimeter and in placeswhere interroom partitions, fireplaces, stairs and other massive structures are planned.
- Do not forget about waterproofing, ventilation and grounding. Do not save on a heater: its insufficient quantity will lead to loss of heat. Rafters with a large section for the construction of the roof - not the best option. It is more profitable to install lighter rectangular with a smaller section. They will not overload the structure, but they will withstand considerable loads.
- The roof needs waterproofing and insulation with any functionality at home. In frame construction, bracing should be installed when mounting walls. Insulation inside the frame must be fixed securely, otherwise it will settle over time, and to fix it, you will have to disassemble the skin. Channels for laying cable cut through the beam. The wires must be in a special plastic box or metal casing.
- The balcony in the house of timber rests on an individual support in the form of pillars. It is better to check fastenings annually in order to avoid collapse. When choosing a project, first of all pay attention to the degree of its energy efficiency.All communication systems must be equipped with regulators to adjust the flow of water, heating, gas, therefore, save.
- Increasing the area of glazing increases the cost of heatingbut reduces the cost of electricity. Therefore, you need to find a "middle ground". As a rule, for this purpose, a coefficient is introduced, which is determined by the ratio of the window surface to the floor area. It must be at least 1/8. Planting trees can be used not only for arranging the local area, but also as a heat regulator. Deciduous trees with their crown protect the room from the hot summer sun. When the leaves fall, the sun's rays are already needed to heat the room during cold periods. Conifers protect against winds.
- In the first year of living in the house you need to ensure a constant temperature. inside about 20 degrees to prevent future cracking. It is better to have all common and business areas on the first floor, and on the second floor there are rooms for sleeping, relaxing or working. If the family has young children and the elderly, then experts recommend building one-story buildings,to eliminate traumatic ladders. Or have their residential areas on the first levels of high-rise buildings.
Advantages and disadvantages
Bar-shaped houses have indisputable advantages over buildings from other materials:
- moisture resistance;
- high heat-insulating properties allow to keep warm in winter and provide coolness in summer;
- natural microcirculation of air provides a healthy microclimate;
- speed of construction;
- ease of use;
- resistance to bending, which allows the construction of buildings of complex shapes;
- strength, which guarantees the stability of the whole structure;
- the small weight of structures from a bar allows you to save on the construction of the foundation, because you do not need to fill the entire base; enough bases on pillars or piles;
- long service life;
- environmental friendliness.
Disadvantages are also available:
- wood needs bioprocessing that needs to be done regularly;
- if the house is intended for year-round living, then it is impossible to do without thermal insulation;
- The fire hazard of wood requires the treatment of the materials used with flame retardants.
Often for suburban areas as a summer houses build a more economical frame house. It is made of timber only frame, which is sheathed with any finishing material. Using feedback from owners living in such buildings, we highlight their characteristic pros and cons.
Disadvantages:
- Less durable compared to a house completely made of timber.
- Short life This factor is due to the fact that between the skin is insulation that needs to be changed. The frequency depends on the type of insulation.
- The need for additional sound insulation.
- Environmental friendliness depends on the material of the skin and the type of insulation.
- Frame houses have cavities between the skin, in which rodents infest.
All other drawbacks - fire hazard, dampness and rotting, are common to all wooden structures and are solved by treatment with special means. Benefits:
- Quick and easy assembly. You can buy a house in the factory and assemble yourself according to the instructions. For this, the manufacturer numbers every detail.
- The possibility of transporting a house from one place to another.
- The ease of construction allows you to not build capital foundations.
- You do not need to spend time waiting for shrinkage at home.
- Good seismic resistance.
- Communications can be hidden between the skin layers.
- There is the possibility of quick redevelopment, in contrast to the capital houses of the bar.
It is better to use frame constructions for temporary residence or as permanent housing in zones with a warm climate.
Beautiful examples
One of the most popular is the Russian style. Small houses look like Russian huts, big ones look like terems from fairy tales. Facing a block house under the beam enhances the effect.
Practical options are widely represented Finnish houses and alpine chalets.
Houses from glued timber do not require finishing, as this building material has an excellent surface. In addition, it is well proven in operation.
Timber - an excellent material for the construction of small and economical buildings.
How to build a house from a bar with your own hands, see the next video.