Welding HDPE pipes: methods and sequence of actions
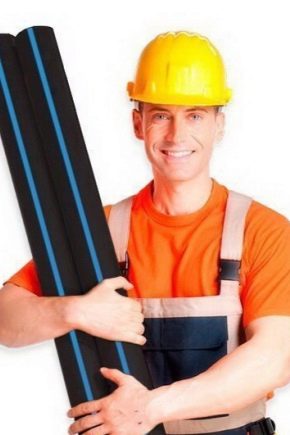
HDPE pipes (low pressure polyethylene) are very popular today. The material is used for various pipelines. In modern conditions, these pipes are almost irreplaceable. The study of methods of connecting highways will help in high-quality welding and home, and professional craftsman. First, let's look at the features of the HDPE pipes.
Special features
The main difficulty is that the operational and technological qualities of polyethylene pipes are in many respects similar to the quality characteristics of polypropylene pipes. They are also not subject to corrosion. The inner surface of the pipe is not covered with bloom.Pipes have high chemical resistance. The material is eco-friendly, has a long service life.
Of the differences, professionals say low temperature resistance. Therefore pipes PND are used only for systems of cold water supply and ventilation. Sometimes they are used for the installation of gas pipelines. The use of polyethylene pipes is possible when transporting in an environment in excess of 40-50 degrees. The exception is cross-linked polyethylene, which is allowed to operate at temperatures up to +95 degrees. Polyethylene pipes have excellent frost resistance, which allows their use at temperatures up to -70 degrees.
HDPE are commercially available in diameter from 20 to 1200 mm. Due to the variety of options they are widely used in various fields. In addition to plumbing, large-diameter highways are bought for sewage, and for both internal and external.
Technical characteristics of HDPE pipes are determined by the properties of the base - low pressure polyethylene. It is lightweight, which makes it easier to install the pipeline, resistant to pressure of tens of atmospheres. Of the negative qualities of the material, it is worth noting the limited possibility of using at temperatures below zero (HDPE glacier),and at elevated temperatures (more than 40 degrees), the HDPE loses its rigidity. When heated to 70 degrees, the base of polyethylene adds in size, but not much.
The range of HDPE is governed by GOST, which was published in 2001. All markings applied to one of the surfaces of highways meet the standards. Marking makes it very easy to choose the right options. The first letters include the name of the supplier, then the PE gauge, the value, for example, 1000 mm. The table also contains the designation of the thickness of the lines, the possible working and maximum pressure, the date of issue and the batch number.
The flow chart of markings also contains color designations in the form of stripes. If the bell is painted yellow, pipes can be used for gas pipelines; if the strip is blue, then only pipes can be laid out of pipes. The pipe connection scheme is drawn up taking into account the standard pieces available on the market - from 5 to 25 meters. Trunk water pipes are usually made to order, have a length of up to 0.5 km, and therefore contain a minimum number of connections.
Polyethylene lines are cheap, which is why they are so popular.Consider the main types of possible connections PND segments among themselves in more detail.
Kinds
The most popular and practical connection of plastic HDPE - welding. The technology of connecting by welding high-pressure polyethylene pipes is simple, but, as in any work, there are some nuances. Technological features familiar to specialists in the field of installation and construction work. Masters during welding use various methods. The quality of work will depend on the equipment and tools used. It is also important to observe some technical features. Popular methods - extrusion, thermistor, socket welding. Also known electrofusion, electrowelding and butt technology.
In any case, the connection of PND welding is considered the most durable and monolithicwhich surpasses in reliability even the material itself. The process involves heating and subsequent melting of the ends of two pipes, there is also a box or fitting welding. At the same time, experts determine a strictly standard exposure temperature. In addition, experts use additional parts and tools.Let us consider in more detail the main types of work carried out.
Electrofusion
The electrofusion method of welding high-pressure polyethylene pipes also requires care and accuracy.
Electrofusion welding requires the following conditions:
- degreased and alcohol-cleaned surfaces;
- the coupling diameters fixed strictly in the center;
- inserted into the coupling lines;
- connected and heated to a certain temperature apparatus;
- electricity for heating couplings;
- cooling of couplings in a free, but fixed condition.
Electrofusion welding can be used to connect pipes with a diameter of 20 mm or more. The method is especially often used where it is difficult to reach the pipeline. To place the machine for butt welding requires a certain position. Other tools (threaded and fittings) also require space. In the work should apply current to the coupling. They heat up, and the ends of polyethylene pipes melt. In this case, the pipe surfaces are tightly connected to the inside of the coupling. The method is considered suitable when connecting highways of a different size. It can also be used if the brands of polyethylene are different.
Electrofusion welding can create strong node and saddle pipe joints. The method is suitable for creating plumbing of a private house. At the same time you can even install a sewage yourself. Elektromuftovy method also claimed because it is convenient to use it to connect pipes made of polyethylene, which have a metallized threaded connection. The many facets of this method greatly increase the popularity of its application.
Butt weld joint
Butt welding, or work on butt welds, is suitable for highways with a size of no more than 50-70 mm, with allowable walls no more than 4-4.5 mm.
For welded work it is worth considering the rules:
- Work should be carried out only on a flat and stable plane.
- The size of the walls of the welded lines should be the same.
- When working on the street, you need to close the return ends of the lines with plugs. It is believed that the draft inside the highways created by the wind reduces temperature. This will interfere with quality work.
- The parts to be welded must be clean both inside and on the surface. Garbage and dust will interfere with welding.The clamps of the welding unit must be as clean.
To adjust a sufficient temperature, you need to make one or two test joints. In the absence of skills, this will help to understand the process of welding itself. Before grinding, wipe the discs clean. The facing process is simple, but requires precision and continuity of work. At the end of the grinding of the pipe ends, the tool must be left on a special stand provided by the manufacturer. For cleaning chips from the chassis you need to use a special additional tool. Hands it is better not to carry out this work. At the end of grinding you need to check compliance with the dimensions of the pipes. The optimum temperature for welding is -15- + 45 degrees.
It is desirable to combine variants of the same brand, but sometimes HDPE is also combined with different markings.
The works should take into account the fact that we should not allow:
- sharp temperature changes;
- uneven heating;
- quick cooling of joints in the field of welding.
The connection of the molten ends to each other should not be extremely sharp. You still do not need to move or twist them, but there should be no gaps between the holes.It is more convenient to hold the end part with special fixing devices. A special heating mirror is placed between the latches. The ends should be melted to softness, and then the mirror is removed. Pipes are held together by hand mechanically.
Too much bonding will give an increased build-up inside the pipes. This rib will reduce the quality of operation of the finished pipeline. With insufficient effort, more time will be spent on welding. Because of the long wait for the desired setting, polyethylene will have time to cool. The force and pressure for each type of lines can be found in the table, which is available in the documentation for the welder. The table also indicates the amount of time required to cool the material. During this period, it is better to hold the welded parts of the aqueduct in the same place for a while.
Welding Socket
The method of socket welding allows joining pipes of different sizes. In this case, the trunk of a smaller diameter is placed in a segment with a larger diameter. The principle of connection is similar to the electrofusion option, since all the same couplings are used here. They securely and tightly connect different highways.The sequence of work is identical to how you need to organize work at the butt joint. The difference lies in the tools used. For example, here you need to install a centralizer. Heated and trimmed need also the polyethylene pipes themselves. In the works, you can use only the coupling without threading.
The way of joining of highways differs. Since the rubber ring is characterized by buoyancy, the rubber parts are softened with household soap to weaken the resistance. Only then can the pipes be easily connected to each other. Even before welding, it is also advisable to strip all parts of dust and dust. The pipes are inserted into each other and tightened with a sealing ring inside. Sometimes for high-quality welding of highways on them knock with a hammer. Work is carried out when using a wooden bar. A blow to the pipe with a hammer should not be powerful. The pipe of smaller diameter just needs to fit tightly into the socket. Details between themselves must be clearly recorded.
In addition to welding, such parts for connection are known as:
- screw plug;
- compression cap.
Parts are installed at the junction points of the two pipes. Special tools are used for their welding.
They will contribute to a tighter connection. If a gap is formed inside the fitting at the pipe docking site, a leak will be observed at that location. It is also worth remembering that the pipes connected by fitting caps cannot be concreted, since in the event of an accident the weld points cannot be repaired.
The flange connection is such an element that allows you to fix not only two pipes, but also segments with cutters, counters, valves, and other fittings. PND flanges standard, correspond to GOST. In everyday life, these parts are mistaken for clamping connectors. This corresponds to the principle of the work of parts. They are clamped using wedge-shaped anchors. To fasten the bolts need a shock force.
Tools and equipment
The main equipment used in the works:
- manual welding machine for the socket method;
- butt jointing machine;
- additional mounting parts for processing.
When working with HDPE, it is important that the heating elements of the unit are non-stick.Parts with such a coating do not need to be scraped and cleaned after welding the seams. Units usually have control indicators as well as thermostats. All of these additions will help especially during welding.
In combination with a welding machine are usually supplied:
- heating parts and nozzles;
- mounting parts;
- special stand, which is called a clamp;
- box in which it is convenient to store details.
Units for connection of polyethylene easy, convenient in work. The heating plates of the apparatus in case of breakage can be easily replaced. These parts look like round plates with PTFE-coated. They have a temperature and mains light as well as a fuse. The temperature can be adjusted by a special regulator, and for the unit itself there is a clamp on which it should be installed.
If you need to weld pipes larger than 400 mm, experts use:
- butt joint machines;
- socket machines;
- electrofusion machines.
Welding units are:
- mechanical;
- hydraulic;
- automatic.
Hydraulic units are particularly versatile.These machines can fix a lot of seams on different highways. In this case, the timing of the work will be minimal, since the equipment already includes all the necessary additions to work.
Of the additional tools worth mentioning are:
- parts for removing oxide deposits;
- fasteners for large saddles;
- kinks for HDPE;
- positioners;
- leveling device;
- fasco-removers;
- files for the separation of highways.
Neglecting any kind of tools is not worth it. Pipe connections may turn out to be poor quality or even defective. The life of such a pipeline will be clearly reduced.
Stages of work
Welding plastic highways with their own hands is possible by the method of electrofusion.
The instruction can be presented as follows:
- training;
- fixing by centralizer and installation of the coupling;
- connection of the welder to the coupling;
- welding;
- removal of the device from under the connection.
Despite the fact that welding is assumed at home, the ends should still be cut with a special tool - a pipe cutter. This will provide better alignment when connecting.It is more convenient to remove the oxide deposit from the junction with a manual scraper or using a bar. The layer to be removed should be about 200 mm from the edge of the pipes. The resulting chips must be removed with the same scraper. Dock the parts need to degrease with alcohol. At this stage, you can apply special wipes. For the most accurate placement in the centralizer, the highway can be marked in accordance with the dimensions of the coupling. According to these values, the pipe and coupling will be more convenient to fix.
The assembled structure must be fixed in compliance with safety regulations. The connectors on the coupling need to connect the terminals of the welding machine. The device turns on and recognizes the bar code that is on the surface of the coupling. Most svarochnikov automatic mode. The period of heating and cooling of the coupling is set just at the time of recognition of the cipher. The welding process will start after the code is read and ends with a beep. To cool the pipe, it must be left alone for seven minutes. Only then can the clips be released from the centralizer and the equipment pulled out from under the soldering point.
To achieve an optimal result, it is important to be guided not only by the instructions, but also by the recommendations of the pipe manufacturer and the welder.
Quality control of seams
An obligatory part of work with HDPE is quality control of connections. All completed seams must be inspected. Only then can you continue processing. For welds there are established technical requirements. The connection is considered quality if it corresponds to GOST. In this case, no additional repair and maintenance for the welded joints of the water supply system is not required.
Welding quality can be checked visually:
- the connection should look like a smooth groove;
- No displacement of welded parts is allowed.
The height of the rollers formed inside as well as outside should not exceed 2.5 millimeters. With a polyethylene thickness of 20 mm, the thickness of the roller may be 5 mm. The welding technique is usually chosen depending on the size of the lines. The technology of the available methods is quite simple. You can master it by the above theoretical recommendations.
How to weld pipes from HDPE with your own hands, see the next video.