Monolithic frame houses: the pros and cons
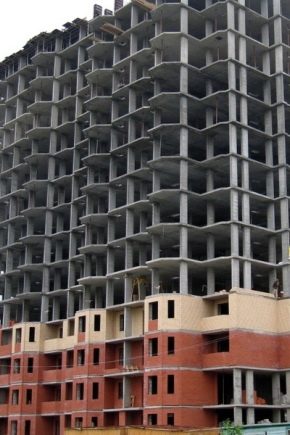
The construction of monolithic frame houses today has become widespread, due to the many advantages of the finished object. The essence of this technology is reduced to pouring pre-prepared frames reinforced concrete. This article discusses the features of this method.
Special features
The technology of construction of frame-monolithic buildings, originally used for the construction of commercial facilities, is becoming increasingly common in urban, private and suburban construction. This situation is due to increased durability and structural stability.
The features of the monolithic frame construction are reduced to the presence of reinforced concrete concreted columns.which are located in areas subject to maximum pressure. Monolithic columns become a transitional element, connecting together monolithic overlap and the foundation.
In this way, the house consists of 3 main elements: the basement, monolithic columns and a reinforcing beltwhich connects the columns and acts as a lintel of window openings (the number of belts depends on the number of floors in the building). At the same time, the technology allows building at a fast pace, which is especially valuable in private housing construction.
Due to the connection between the monolithic floors and reinforced concrete columns, it is possible to ensure unsurpassed strength and reliability of the house. At the same time, monolithic walls are thinner, for example, brick. That is, the internal free space of a monolithic house will be larger than a brick counterpart.
Despite the presence of columns and solidity of overlap, the structure remains airy, not bulky. This is achieved through the installation of columns in increments of 7-10 m. The supporting frame is subject to insulation and cladding.
The internal space of the object remains free and allows you to perform almost any layout.The technology itself ensures the implementation of virtually any architectural design, including floating floors, the construction of high-rise buildings.
The following types of foundations are suitable as a base:
- Shallow-depth tape. This design consists of prefabricated blocks, applied on the ground with a low level of groundwater rise. With such a foundation, the building does not have a basement.
- Monolithic tape. Allows you to build a house with a basement on non-rocky soils.
- Floating. It is suitable for medium to highly lucrative soils, although on such soils it is not recommended to conduct the construction of monolith-frame objects. It is a mobile board installed in a semicircular base. Due to the mobility of the board, the house itself does not change its position.
The foundation assumes the presence of additional reinforcement, which will provide the strength of the bearing elements. For this, reinforced concrete formwork is arranged - reinforcing rods are poured with concrete. Due to this, the valve is protected from temperature extremes, corrosion and oxidation processes.
The strength of the resulting formwork is 150 times greater than the strength of concrete and reinforcing bars separately. It depends on the size of the fittings used and their location. In addition, the monolith has no seams, which also guarantees the reliability of the house, its durability. It is able to serve about 100 years, without requiring major repairs.
During operation, such a foundation becomes stronger, which is associated with the constant strengthening and strengthening of reinforced concrete structures. Thanks to reinforced concrete formwork and pouring columns, high fire safety of the house is ensured.
The issue of fire safety at home is decided at the stage of the organization of supporting structures, so additional protection is not required.
The technology allows building seismically stable objects that can withstand such activity up to 8 points. Monolithic frame houses due to their low weight are suitable for construction on moving soils. At the same time they give a slight and uniform shrinkage, which allows you to start finishing the structure immediately after the construction of the house.
If necessary, construction can be carried out year-round.However, in the cold season, in order to evenly harden the concrete, it is necessary to resort to heating it, which leads to an increase in power consumption. When working at zero and negative temperatures, special components should be added to the concrete.
Durability, durability, fire resistance and freedom in the choice of architecture and planning of the house are the main advantages of monolithic-frame objects.
However, they have characteristic cons. For example, reinforced concrete columns tend to form "cold bridges", which significantly reduces the thermal efficiency of the house. Their elimination requires high-quality thermal insulation, which also affects the total cost of construction. At the same time, reviews of tenants indicate that approximately every 7-10 years in these areas it is necessary to update the insulating layer.
It is also necessary to build a large number of pillars and formwork, which increases the complexity and financial costs of the project. In addition, the concrete does not have high heat and sound insulation properties, and therefore requires the use of insulation and noise absorbing materials.
To build such a building is better to attract professionals.In the absence of experience in the construction of buildings, the project may not meet the specified criteria. You will also need the use of special equipment, high-quality high-strength concrete. All this increases the cost of the monolithic frame house compared to a brick or panel analogue by about 10-20%.
Projects
Before construction, they diagnose the condition of the ground, find out the level of groundwater. It is necessary to take samples of the soil with your own hands and contact a specialized laboratory, where, after the examination, they will issue a conclusion. Taking into account the features of the soil, the optimal type of foundation is selected. In preparing the project should immediately consider the location of communications. If this is not done, then there may be restrictions and difficulties of their installation, which would entail additional costs and delaying the construction period.
It is also important to plan a forced ventilation system, since concrete is characterized by low vapor permeability. This will lead to increased humidity in the rooms, erosion and destruction of concrete.
At the design stage, materials are calculated. Approximate calculation for 1 square.m: concrete - up to 0.7 m3, reinforcement - up to 70 kg. It is also important to select and calculate the volume of material used for masonry walls. For these purposes, it is common to use aerated concrete or other building blocks, as well as bricks.
At the design stage determine the type of formwork. For a private house usually used permanent formwork. The preference is given to an aluminum design, as easier in comparison with a steel option. Choosing between wood and laminated plywood, they prefer the second one due to its higher moisture resistance and the absence of warping. The wooden frame of the formwork should be treated with fire retardants and water repellents.
Removable formwork involves the use of a special design. As a rule, it is cheaper and more rational to arrange its rental, rather than purchase.
Building
Construction of the house on the cast-frame technology is carried out using formwork, which can be both removable and non-removable. The latter with your own hands can be created from metal (aluminum or steel alloys with anti-corrosion protection), wood (glued wood),laminated plywood. They will provide the necessary shape of the foundation, and after pouring they will become part of the structure.
The modern technology of using water-resistant polystyrene foam plates as a permanent formwork also deserves attention. Such plates, among other things, provide additional thermal insulation.
Structurally, the formwork for a frame-panel house can have one of the two types described below.
- Shield. Consists of rigid shields of various shapes and sizes, fixed fasteners. Suitable for creating various architectural elements, for example, semi-circular bases.
- The tunnel. It is a structure created at the factory according to a project prepared in advance and delivered to the construction site as a finished product.
Delivery of concrete to the object is provided by truck mixers. A small amount of concrete solution can be mixed on its own directly on the construction site. In the formwork, the concrete is supplied by a crane or a concrete pump. In the first case, the use of special containers where the solution is poured is relevant.
When pouring concrete, it is obligatory to use deep and surface vibrators, which provide consolidation of the formwork and prevent the appearance of voids in the monolith.
The construction process can be divided into 5 stages:
- preparation of the high-strength base;
- installation of the frame of reinforcement;
- formwork device;
- pouring concrete solution;
- formwork removal (in the case of removable formwork), finishing works.
The preliminary stage will be the preparation of the construction site. It must be cleaned of garbage, make markup. After that, the extraction of soil under the base to a depth corresponding to the project documentation is carried out. If there are dimples and loose areas in the pit, they should be filled and reinforced with a mixture of gravel and sand. After that, formwork can be constructed.
The next step is to pour concrete in the form of a monolithic slab or a strip base reinforced with reinforcement. Now the concrete should harden and gain strength. On average, it takes at least a month.
After the concrete has hardened with the help of reinforcement, a spatial frame is mounted and formwork is assembled, the dimensions of which (from the inside) correspond to the dimensions of future columns.The formwork needs to be poured with concrete, compacted and the structure fixed for 4 weeks.
After a specified period of time, the formwork is removed, after which you can proceed to the laying of walls using cellular building blocks, bricks or other materials. After that, the design of the roof, insulation and insulation of the outer part of the walls, lining the structure.
Reinforcement of monolithic walls is made using reinforcement or reinforcing mesh. In the first case, reinforcement with a cross section of 6–8 mm is used; for erecting a house of 2 or more floors, it is recommended to take stronger reinforcement with a cross section of 10 mm. The reinforcement is mounted horizontally and vertically, with special attention paid to the corners.
It is important to reinforce the reinforcement of high quality, otherwise it will not be possible to buckle it after pouring with concrete.
Beautiful examples
Monolithic frame construction technology allows you to create original design objects, which is especially appreciated by the owners of private houses.
- Compact, but spacious house in 2 floors with a canopy for the car.
- The classic version of a country house, also having 2 floors. Built on permanent formwork.
- Technology monolithic construction is used in the construction of objects in the modern style. The house is in 2 floors with a flat roof, lined with facade panels under the brickwork and wood.
- Perspective, from the point of view of investment, a townhouse for 2 families with garages on fixed formwork according to the technology of frame-monolithic construction. It can be built on a limited (stretched) section. Floors - a house in the 1st floor with a residential attic.
- An example of a spacious home for a large family. It has a bay window, a terrace, built on cast-frame technology using plastered wall panels, the roof is wooden-truss with a coating of ceramic or metal tiles. Formwork type - non-removable.
- Examples of ergonomic country houses for small (no more than 6 acres) plots built on fixed formwork. The increase in usable area is achieved not only due to the reduced thickness of the monolithic walls, but also through the use of the operated roof, where the attic is organized.
In the next video you will clearly see the features of the construction of houses with a monolithic frame.