Faults of Baxi boilers and the process of their elimination
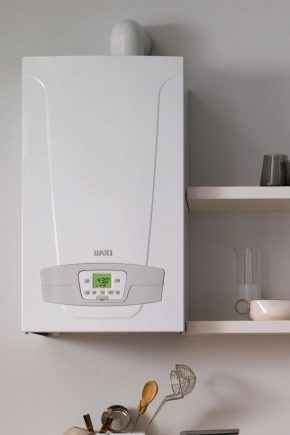
Modern boiler equipment has gone far from simple stoves and fireplaces. But even all the power of modern technology and the excellence of engineering achievements do not allow completely escape from the occurrence of defects. No manufacturer will undertake to assert that its products absolutely exclude all possible malfunctions.
Special features
The Baxi boiler, as befits a modern heating equipment, is equipped with "smart" automatic devices. They do not just stop working when problems arise, but also inform users about possible violations. Anyway, the company's products are able to serve any kind of heating system. The company's engineers have created a number of devices suitable not only for residential buildings, but also for production facilities.
Systems require strictly defined conditions and parameters:
- boiler rooms should have a volume of 15 cubic meters. m .;
- ceiling height - not less than 220 cm;
- ensuring intensive air exchange.
The manufacturer claims that all the latest technological developments of the industry are combined in its products. Significant experience gained over the past decades, together with the involvement of trained specialists, has made it possible to create many attractive designs. There are among them single-circuit and dual-circuit apparatus, products with an internal boiler. The power and temperature of water heating, the heated area and the automation used differ. But all this does not allow, again, to consider such boilers completely protected from malfunctions.
Codes
Very often, Baxi boiler breakdowns are labeled with the code E10.
Such an error may indicate on / about:
- malfunction of the sensor controlling the circulation of the coolant;
- that pressure drops below a dangerous mark;
- the absence of contacts between the pressure measuring relay and the electronic board;
- degradation of the relay itself;
- error in the pump sensor;
- damage to the pump;
- heat exchanger contamination.
Defect E01 is associated with a critical state of the apparatus. The system issues such a code if the boiler cannot continue its work until the true cause of the failure has been eliminated. In Mainfour 240f, this error is issued for the same reasons as in other models. But in Eco Four 24f the problem with ignition is often caused by a malfunction of the electronic board. After all, the igniting module is placed directly on it, and the bundle is very dense - there is practically no chance to understand without special knowledge.
Additionally, the cause of violations with this code can be gas shutoff or its weak pressure, insufficient air flow. If this error occurs again, you should immediately call the specialists from the service center. The final diagnosis is made only after checking with a differential pressure gauge.
For your information: it is worth checking whether the gas is coming in (if the tap is open and the meter is working, if there is an accident on the main or if the tank has run out). If the cause is rooted in the gas valve, it is almost always necessary to change it.
E03 - an error code that appears on the signals from the thrust sensors. In some boilers this role is assumed by a pneumatic relay, in others - by a thermostat.If the removal of harmful flue gases is disturbed, there is a danger to the health and even the lives of people.
Often the cause is the excessively small diameter of the gas passages and their entanglement. This kind of design errors are corrected only by altering the entire system.
In some cases, the thrust sensors register a reduction in air flow due to clogging of the chimney, its icing, covering with soot or blockage of the inlet (outlet). Also, the problem may be related to the excessive length of the smoke extraction circuit. It is necessary to check the company recommendations again and find out if they are observed for a specific boiler model. A pneumatic relay malfunction is indicated by a special click sound as soon as the feed tube is discharged. This discharge can be reproduced artificially in order to better and more accurately assess the situation.
In boilers versions Main 5, Eco-5 Compact, the root cause may be an error in the configuration of control automation. It is enough to specify an incorrect parameter so that the E03 code appears constantly, although there will be no objective reasons for it.
E00 mostly occurs when the boiler is poorly or improperly grounded.You can also assume that there are problems in the logical operations of the electronic board. These problems may be caused by the inability of the capacitors to accumulate charge in the intervals between pressing the control buttons.
The problems with the Baxi boiler are not always due to the fact that it does not heat hot water. Sometimes the situation is reversed: the temperature in the heating circuit is increasing too rapidly. Error E25 is shown by automatics, if the heating exceeds 1 degree per second. When exactly such a situation arises in reality, simultaneously with stopping the device and issuing a signal, you can detect a typical crash. He publishes boiling liquid in the heat exchanger.
It also happens that the movement of the coolant through the heat exchanger is extremely slow, and even with normal intensity of combustion, the water warms up excessively.
The slowdown of its flow is due to:
- faulty or blocked pump;
- dirty filters;
- powerful hydraulic resistance;
- the occurrence of air congestion.
We should also mention the wall-mounted boilers, where pumps with wet rotors are widely used. The torsion of the rotor occurs in the water, lubricating the bearings, but also affecting them. Gradually, parts of the device are covered with bloom and dirt.Therefore, there are situations when the rotary unit is wedged or the bearings themselves break. You can also assume failures in the electrical infrastructure of the pump, which is also experiencing significant loads during operation.
An important place in the structure of faults takes E35. It arises mainly due to improper grounding of the control board. Even the periodic occurrence of an error under such a code should immediately alert the owners of the boiler.
The fact is that under the action of an incorrectly connected current, the board itself can fail. And its replacement will cost at least 1/5 of the cost of a completely new boiler.
Worse, the board may continue to seem to work, but at the same time it loses the ability to monitor the normal operation of sensors and executing mechanisms. Therefore, this device is configured to carefully control the quality of the connection, and sometimes even to the polarity of the incoming current. An elementary test can be undertaken using a tester or an indicator screwdriver. Such tools are a must-have attribute of any responsible house owners, especially since they are needed in many other cases.
Quite often, users of gas boilers are faced with an error codenamed E98. If you turn to the official forum of the company, you can find the opinion of its representatives that This problem is almost always caused by a deviation from the electrical installation rules:
- illiterate connection;
- presence of potential where it should be absent;
- unfulfilled or poorly thought out grounding.
This fault is diagnosed by the absence of a signal that must come from a relay installed on the gas valve. In addition to problems with the relay or with its power supply, it is possible to assume a violation of the action of optical pairs.
It is impossible to do anything with your own hands in such a situation - you will have to call skilled craftsmen with the tool. Almost always have to change the board, except in cases of recent replacement and errors with configuring the operation of the device.
E26 - a code indicating that the temperature specified by the board is exceeded by 20 degrees or more. The main sources of violations are the same as in case of failure No. 25. Testing is usually started with a circulation pump, which very easily and quickly loses its working capacity during deformation.But information about the defect E96 is extremely small, in the company documentation of the Italian concern it is reported sparsely.
The main source of such a failure, according to professionals, is the understated supply voltage of the boiler. The appearance of this code is usually ignored if the heating is not blocked. Immediately after the restoration of normal voltage automatics resume heating.
Only with frequent or excessively long stops it is necessary to diagnose the system itself and the power supply circuit. Occasionally you have to contact the organization responsible for network power at home to eliminate problems on the line and input.
In conclusion, the review of the most frequent problems with Baxi boilers should be said about the error code E06. This combination of characters is displayed on the display if the automation detects a malfunction in the temperature sensor or an excess of permissible heating. In addition to failures within the sensor itself, the control board may fail, and you can also assume a violation of contact with it. The test should be started by testing all the contacts with the tester and measuring the resistance on the sensor (it must comply with the documentation).
Causes of breakdowns
Readers of this article already know about a number of reasons why a notification with this or that code is activated on the displays of Baxi boilers. But it is important to understand that the gas apparatus is a technically sophisticated device. Therefore, in addition to error codes, you should know about the actions in case of actual violation of one or another kind. Suppose the burner does not reach the maximum power. This may be due to an incorrect pressure setting in the heating system.
You can also assume violations of the gas valve modulator or diode bridge disorder. If the actions specified in the instructions did not lead to success, you should immediately give up trying and contact the experts. Sometimes there is another problem: stopping work immediately after launch.
Most often, the pressure in the supply gas pipeline is too low or the burner is clogged. When it seems to be working, but the coolant is warming up poorly, the main reason is the incorrect setting of the smallest and largest power values on the valve.
With the modulation mode inoperative, it remains only to change the valve. If the temperature sensors show incorrect values, they will also have to be replaced.Returning to the weak heating of the coolant, it is worth noting such a possible source of violations as a not fully open three-way valve. It is possible to diagnose its failure by waiting some time before the circuit cools down and closing the shut-off valves. As soon as this is done, the boiler is transferred to the water supply system; if heating starts to warm up instead, the output is confirmed.
Sometimes the ignition of the boiler is accompanied by slamming sounds. They are provoked either by a small gas pressure or by changing the configuration of the supply line with inaccurate movement of the boiler. Distances (clearances) are checked once every 6 or 12 months.
If the coolant has suddenly become colder than usual, the clogged filter is almost always the culprit. But we can not exclude the overflow of pipes with dirt, covering them from inside with ice.
There is a situation in which the indicator shows the lack of water. This is mainly due to the clogged secondary heat exchanger. To minimize the likelihood of damage, you should consult a professional before selecting and installing boilers. Periodic calls to service centers for maintenance also reduce the risk.If any of the listed problems is found, the reasons for them are sought in descending order of probability.
How to fix?
Repair when an error occurs E10 on their own is not always possible. Without the help of specialists, it is possible to eliminate the disturbance in the operation of the pump. You can also clean the filter systems yourself. Finding problems in other systems of the boiler, most often have to turn to professionals. When the boiler does not start at all, you first need to check whether the phase and zero are connected correctly.
If this installer’s error is not eliminated in time, the heating system will actively saturate with air., and automatic equipment will naturally prohibit the heating unit to work. In the presence of a weak flame of the burner, you need to re-configure the key parameters of the system. It should be guided solely by the instructions of the instructions, and not by someone's "authoritative" advice!
It is possible to cope with a quick unauthorized stopping of the boiler after it has been put into operation by reducing the minimum gas pressure level (25 mbar) provided in the system to 5 mbar. The same technique helps occasionally eliminate pops when the boiler is running.
If neither this method, nor the adjustment of the distance between the igniter and the gas pipeline helps, it is necessary to reduce the intensity of the thrust. The frozen tubes are removed to areas of 100–150 mm long, after which a new fragment is inserted. Water boiling in the pressostat is almost always caused by condensate entering the boiler and the resulting increase in pressure.
You can change the flame modulator or adjust it only using special spare parts of factory origin. Similarly, when the stabilizer is stopped.
The pressure drop in the system is sometimes triggered by an inoperative gearbox. The solution is only one - his replacement. And here there is a fork: whether to choose original or foreign parts. The latter have only one major advantage, that is, low price. But all responsible consumers choose only a branded product, because this is not the case when saving is appropriate.
In the event of error No. 3 on the boiler Baxi Eco Four should examine the chimneys. Sometimes the tip of the coaxial flue gas outlet, more precisely, the inside grid to protect against coarse pollution, is clogged with frost.In the summer, it is often necessary to clean the cobwebs or even bird nests from the inside.
Many "incomprehensible" interruptions are generally eliminated if you inspect properly the supply and discharge air pipes. In the turbocharged models, they check the operation of the fan by removing the front cover.
When the blades do not rotate, you need to try scrolling them manually. Sometimes it allows you to detect jamming. Also, violations in the operation of the boiler may be associated with the exhaustion of the lubricant resource, clogging of the blades, and wear of the axial sleeve. What to do in each of these cases is understandable and true.
The inability of the fan when starting the boiler is cured:
- restoration of the quality of contacts;
- replacing the motherboard relay;
- replacing the entire ventilating unit.
For more information on eliminating E01 error, see the video below.