Choosing automation for the pump
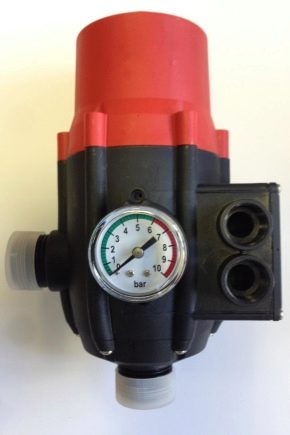
The well for the water at the site is almost a mandatory phenomenon, it provides many benefits. In order for her work not to be clouded by constant breakdowns, it is necessary to install automation. It can be different in layout, it can be purely mechanical or have an electronic control unit, but any automation ensures the proper operation of the pumping system.
Special features
Automatic equipment for the pump, as well as for heating, supports the normal operation of the system,watching for many parameters, such as pressure, temperature of the pump, carries out the distribution of water in the system, and the like. For correct operation, several nodes of various types are needed and their adjustment for specific specifics, ranging from the type of pumping equipment and the depth of the well to the number of intake points and the required working pressure.
Regular operation of the pump is supported by the work of automation important nodes.
- Distributing collector device. It provides water to several points of water intake throughout the service area.
- Relay. Monitors the start and stop of the pump. Necessary to control the optimal pressure in the system. When selling has basic settings from the manufacturer, which may vary according to the needs of a particular system.
- Manometer, a device that measures the operating pressure of the system.
- Dry running sensor. Necessary to prevent overheating of pumping equipment in the absence of water in the system.
The minimum amount of automation for the pumping station includes a controller and protection system.
- The controller that regulates the power of the pump.Necessary for the system to work optimally.
- Protection system:
- dry run sensor;
- overheating sensor;
- sensor that determines the gap in the pressure line.
Positive and negative points can be noted when using automation.
Automation, like any complex device, is designed to improve the performance of the mechanical component, in this case the pump, in this regard, its use provides certain advantages, these include:
- A wide range of specialized units allows you to choose the right option for the pump with almost any parameters;
- the automation kit is already grouped into the system and is ready for operation, therefore, it is possible not to select individual nodes, not to check the details for compatibility and interaction synchronization;
- The main advantage of automation is to work in a smooth measured mode of the entire pumping system, while at the same time it is not necessary to monitor its balancing, because this is also the task of automation.
In addition to positive qualities, automatics also has its drawbacks, and these are:
- an assembled system is more expensive than assembling it from separate nodes independently;
- if you have certain knowledge, you can pick up each node so that it perfectly meets the requirements of the pumping system and adjust it for optimal performance; with a complete system, such a complete coincidence is rare, but if you search, you can find a good version with high consistency;
- Automatics mostly do not fit well with vibratory pumps due to their specific requirements for inlet pressure of 0.3 atm, for which it is not designed.
Kinds
All automation used to control the operation of the pump is divided into 3 types in chronological order according to the sequence of its creation.
1st generation
This is the first and simplest automated control system for pumping equipment. It is used for simple tasks when you need to provide a constant source of water in the house. It consists of three main parts.
- Dry running sensor. Required to turn off the pump in the absence of water, which serves as a cooler, without it the pump will overheat and the winding will burn. But an additional float switch can also be installed. Its function is similar to the sensor and is repelled from the water level: when it goes down, the pump turns off. These simple mechanisms reliably protect expensive equipment from damage.
- Hydroaccumulator. It is an essential element for system automation. It performs the function of water storage, inside which the membrane is located.
- Relay. A device that controls the level of pressure should be equipped with a pressure gauge that allows you to adjust the operating parameters of the relay contacts.
Automation of the first generation for deep well pumps is simple due to the absence of complex electrical circuits, and therefore its installation on any pumping equipment is not a problem.
The functionality of the system is as simple as the mechanism of operation, which is tied to a decrease in pressure in the accumulator when water is used up. As a result, the pump turns on and fills the tank with new liquid. When full, the pump is turned off. This process continues in cycles.. It is possible to adjust the minimum and maximum pressure by means of a relay. The pressure gauge allows you to set the lower and upper limit of automatic operation.
2nd generation
The second generation differs from the first using an electronic control unit to which the sensors are connected.They are distributed throughout the pumping system and monitor the operation of the pump itself and the condition of the pipeline. All information goes to the electronic unit, which processes it and makes the appropriate decisions.
When using 2nd generation automation, a hydroaccumulator may not be used, since the pipeline and the sensor installed in it perform the same function. When the pressure in the pipe drops, the signal from the sensor enters the control unit, which, in turn, turns on the pump and restores the water pressure to the previous level, and at the end turns it off.
To install automation 2nd generation requires basic skills in handling electronics. According to the principle of operation of the 1st and 2nd generation systems are similar - pressure control, but in terms of cost, the 2nd generation system is much more expensive, as a result, it is in less demand.
The lack of a hydroaccumulator is a compensation, and, consequently, money is saved for its purchase, although it also has its advantages, since the system based on it continues to work even in the absence of electricity.
3rd generation
Such a system is highly reliable and efficient, but it also costs more than its predecessors.Exact operation of the system is provided by advanced electronics and allows you to save on electricity. To connect this system, you need a specialist who not only installs, but also sets up the correct operation of the unit. Automation provides a full range of equipment protection against breakdowns from “dry running” and rupture of the pipeline to protection against power surges in the network. The principle of operation, as in the 2nd generation, is not associated with the use of a hydroaccumulator.
The main difference is the ability to more accurately regulate the operation of mechanical components. For example, when turned on, the pump standardly pumps water at maximum power, which is not necessary with its low consumption, and electricity is consumed to the maximum.
The system of the 3rd generation varies the pump capacity depending on the intensity of water intake, increasing and decreasing its speed. This not only saves energy, but also extends the service life of the unit.
Wiring diagram
Depending on the type of pump connection scheme may vary.
Installation and connection of the submersible pump and automation
For each generation of automation, the connection to the pumping system has its differences, often its features are described in the instruction manual.
Consider the wiring diagram on the example of equipping a submersible pump with automatic equipment of the 1st generation with a hydraulic accumulator.
- First, the accumulator is strapped. The scheme consistently connected nodes. To seal the threaded connections used fum-tape.
- The first “American” sits on the thread, with its help, during the operation, the accumulator will be serviced to replace the membrane.
- From the second side, a bronze adapter with threaded branches is screwed to the “American”.
- Two knots are screwed to them: a pressure gauge and a pressure switch.
- Next, a PVC pipe is installed by means of a fitting adapter on the end of a bronze accumulator adapter.
- On the other hand, the pipe is attached with a fitting to the pump.
- The supply pipe and pump are laid on a level surface.
- A safety cable with a spare length of 3 meters is attached to the loop of its body.
- At the pipe with an interval of 1.5 meters with clamps attached cable and cable. The second end of the safety cable is fixed next to the casing.
- After which the pump is lowered into the well, and the safety cable is tensioned.
- Next, the casing is covered with a protective cap protecting the well from clogging.
- The cable is connected to the relay and is led to the control cabinet.
- Immediately after connecting, pumping of water into the accumulator begins. At this point it is necessary to bleed the air by opening the tap.
- After the water flows without air, the valve closes and the pressure gauge is checked. As standard, the relay has settings for the upper limit of pressure - 2.8 atm, and for the lower limit - 1.5.
For other indicators, the relay is adjusted using special screws inside the case.
Installation and connection of the surface pump with automatics
With this type of pump, the automation connection has a number of differences, although the sequence of its connection is the same as that of the submersible type. The differences are as follows:
- PVC pipe is connected to the pump inlet to collect water from diameters from 25 to 35 mm;
- through the fitting, a check valve is attached to the second end and lowered into the well, while the pipe should be long enough for its end to sink into the water by about a meter, otherwise air will be trapped;
- before starting the engine through the filler hole and the intake pipe filled with water;
- with proper hermetic connection of all components, switching on the pump will be accompanied by water pumping.
Manufacturers
Selection of any technological equipment of the borehole pump is associated with the risk of buying low-quality goods, and to avoid this, you should give preference to a manufacturer with a good reputation.
Among such companies there are several.
- "Unipamp" Russian company producing reliable quality equipment at a reasonable price. Automation has a wide choice for various pumping systems, designed to work with units with a capacity of not more than 1.5 kW. The construction of the pressure gauge is combined with a pressure switch, this feature simplifies installation.
- Grundfos - High quality Danish automation. The main features of the products are:
- protection level - IP52, automation with such a marking can be installed in almost any conditions;
- trouble free quality;
- some products are designed for voltage less than 220V;
- a wide range of models for different types and capacities of pumps.
- Condor - German equipment of impeccable quality.Their products are distinguished by such qualities:
- bipolar pressure switches;
- universal mode settings;
- high price.
- Italtecnica - Italian company that produces high-quality automation at a reasonable price. The equipment is designed for a pressure range of 1-5 bar. Warranty period of products - 1 year. And also they produce automation for pumping stations, the operating parameters of such devices are as follows:
- working pressure - 1.4-2.8 bar;
- polymeric material of the housing with an insulating gasket;
- silver anti-stick with nickel;
- copper terminals.
Among the manufacturers of high-quality water supply products, one can also highlight the brands “Dzhileks”, “Prescontrol”, Espa, “Vistan 3”, “Akvaraboot”, “Malysh” and Alco.
Tips
In the process of selection, installation and operation of automation for the pump with their own hands there are nuances, knowledge of which can improve the efficiency of the system of the circulating and drainage pump.
Setting too high a pressure in the system adversely affects the operation of the pump, and in addition, leads to a disproportionate overrun of electricity. Sometimes it just doesn't work.
The water pump automation of the 3rd generation uses frequency control of the pump speed, if the existing pump does not support this technology, there is no point in installing the 3rd generation automation.
Connecting the wiring, you must ensure that it is well fastened to the terminal blocks. At the same time, a certain polarity of the pump and voltage are unimportant.
How to connect the pressure switch to the pumping station, you can find out further.