Specifications and methods of installation of profile pipes
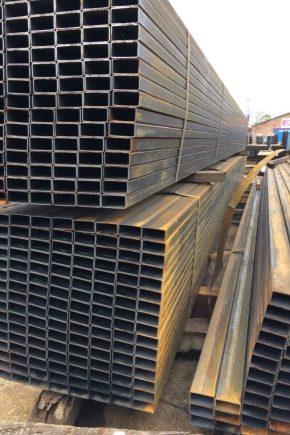
Modern building material is a profile pipe, which offers us the metallurgical industry. Conveyor production of core pipes was started in the middle of the last century, but only now the use of such material has become relevant in construction work.
Special features
Empty rod-type pipes can have various sections, for example, square and even oval. They are made using various materials.
It may be:
- stainless steel;
- carbon steel;
- low alloy steel;
- plastic.
As for the process of manufacturing such pipes, it consists in changing round sections to the required form: square, oval or rectangle.In the production of used strip, which is a kind of billet of metal, or a material that will later be used for manufacturing. And thus the pipe already in finished form with the help of specialized equipment acquires the necessary shape of the section.
The profiled pipe can be aluminum, metal, galvanized. In addition, it is different in appearance - it can be square, rectangular, including thick-walled and thin-walled. Profile view has a diverse section. The minimum section of the profile pipe is 1x1 cm, but the maximum size of the section can reach 50x40 cm. As for the thickness of this product, it can be from 1 mm and reach 2.2 cm. These types are able to withstand the maximum load, since the flat surface is even distributes it to the segment. The weight of such a product is small due to the fact that the pipe in the middle is empty. Thus, the fabricated design is substantially lightened in weight.
Profiled pipes are used:
- for the organization of the framework for future construction;
- for arrangement of platforms and big stadiums;
- for the construction and reconstruction of arches and bridges;
- for the construction of spans on farmer sites;
- as the basis of billboards;
- for the construction of mansards or buildings of low type;
- for the construction of partitions or premises for industrial use.
Very important in the work of the mass of material. In order to understand how much the pipe weighs and whether it is suitable for the required work, you will be helped by a table which the manufacturer attaches to each brand of pipe. Based on her data, you can determine whether it will be able to bend at home. It should be noted that this material is basic in some construction works and in structures. It can be used to organize the framework of the overlap of a warehouse building. Thus get a reliable and fairly affordable design.
If scaffolding is designed from shaped pipes, then you can easily get to the facade of any building for repair or facing works.
Due to the fact that pipes of this type are easily connected in a short time, with their use you can install a tower crane and you will not need to use heavy machinery.
As for the features of this material, among them are the following:
- the use of these pipes is an economical option, since the construction of large buildings requires little material;
- the speed of installation and its lightness are a significant advantage, which allows you to construct a bulky building in a short time;
- in the manufacture of pipes of the type used anti-corrosion treatment, which is fully suitable for sanitary and hygienic standards;
- Another feature of the structures of the profile pipe is the replacement of one of the entire structure, since in such work there is no need to disassemble it to the damaged section, and it is enough to remove the old pipe and install a new one in the same place;
- ease of transportation is justified by the fact that the pipes are square or rectangular in shape and thus securely fixed in one position;
- such pipes are resistant to high loads and to bending;
- their use makes it possible to design structures of any type of complexity.
Due to the fact that the pipes of the profile type have such featureswhich are much superior to the options with a round section, they gained popularity and became relevant for use in different purposes. But many consider as a disadvantage the high cost of such a product and the low level of corrosion resistance.
Kinds
It is more difficult to make proftruby, than options with round section. The manufacturing process in this case takes place in several stages. At the first stage, the plant purchases a semi-finished product, namely, metal tapes with a thickness that will be the thickness of the walls of the finished profile pipe. Next, the tape is unwound, produce longitudinal cutting, straightening, cut off the ends of the strips, perform welding work and place it on the storage equipment. On this equipment, a pipe with a round cross section is manufactured, then it is installed in a molding machine. This machine performs preliminary welding of pipe sections and launches equipment that conducts temperature processing and forms a profile section of a round pipe.
After completion of production, the product is checked for compliance with GOST standards. For such a test, flaw detection is carried out,visually inspect the product and check the conformity of the sizes. At the final stage, the manufactured pipes are cut into certain pieces and packed.
The manufacturing process may differ, as the pipes can be seamless, hot rolled and cold rolled. In addition, even the technology for creating materials with a profile section can be different.
Types of pipes:
- Seamless hot. This option has a high strength, corrosion resistance.
- Profile cold-rolled. Designed to withstand large and regular pressure. In addition, such a product has an excellent indicator of density.
- Welded with a profile type section. This type has a good indicator of density and is designed for long-term operation.
If we talk about the areas of use of such pipes, then those that belong to the standard variety can be used to conduct pipelines, pull cable equipment, create scaffolding, and also as a fence for a specific section. Trunk pipes are used to construct a pipeline where pressure drops are possible.There are also heat-resistant varieties that are used in industrial and food industries, and special pipes of the profile type, which are used in the process of creating parts for automobiles. As for the pipes, which are used in the process of erection of buildings, these are structural profile varieties. With their help in construction, there is no need to use cranes and other heavy equipment for the construction of high-rises.
Separately, should consider the shape of the pipe. They are made in an oval, rectangular, square and flat section. In addition, they differ in material. It can be metal or plastic. Metal is referred to the most demanded material as it is durable. As for plastic, its stability is lower, but the price is more acceptable.
Production stages
The process of manufacturing a pipe consists of several stages:
- processing the resulting strip;
- production with a round section;
- change from round to shaped;
- heat treatment and cutting to the required dimensions;
- control compliance with GOST.
The material for the manufacture of the profile pipe is supplied to the plant in the form of metal rolls. These rolls are unwound and cut into a slitting machine. After the roll is cut to the required width, the strips are welded into one long and wound onto the drum. This is necessary so that the milling machine does not stop functioning. Thus, failures in production are avoided.
After that, the workpiece is fed from the drum to the forming machine, which produces a pipe blank with a circular cross section. At this stage, a pipe is obtained that is not closed by a seam. It is at the stage of forming the blank that the metal undergoes heat treatment. After processing, the workpiece is installed on the mill for welding, which welds the pipe. The welding itself is carried out in an oven way, that is, using shielding gas or using high-frequency current. As for the seam, it can be straight type or spiral. In order for the welding seam to be reliable and durable, the machine expands the seam edges. In this way, a burr is obtained — the excess drips of molten metal are pressed into the surface of the shaped tube, the extra burr is removed with the help of a cutter, and at the end of this stage the tube is cooled with an emulsion composition.
At the next stage, the required cross-section of the profiled pipe is formed from a circular section of the pipe. This procedure takes place in one or in two different versions. So, for example, if there is a need to create a pipe with an oval or flat section, then for this, the workpiece must be passed through rollers of the calibration type. They are designed to align the workpiece along the entire length. If there is a need for a square, rectangular, or any other section, then another step is added to the previous step - skipping the workpiece through a profiling machine. He is already in automatic mode forms the section established on the control.
At the end of the production, the resulting pipe is cut into segments of the same length, a study is conducted for compliance with the standards, and if everything fits together, it is packed and sent to the addressee.
In order for the pipe to be additionally protected, it is cold or hot galvanized. If hot galvanization is performed, then for this the pipe is cleaned and dipped in a bath with boiling zinc, and if a cold method is used, then a layer of powder or polymer paint is applied to the surface of the product.
Dimensions
According to the standards, the sizes of pipes of different sections are calculated based on the raw materials used for their manufacture. This metal has a density of 7.85 grams per square centimeter. For pipes with a profile section, there are certain criteria that are specified in GOST 8645-68.
Product requirements are:
- the outer wall has a length of from 1.5 to 18 cm;
- outer width can be from 1 to 15 cm;
- wall thickness can also be from 1 mm to 1.2 cm;
- section can be the most diverse;
- weight is calculated by meters, for example, one meter can be 300 grams and 55 kilograms, it all depends on the pipe section.
Thus, the profile tube with a square cross section can be made according to GOST, which allows the manufacture of pipes with external ribs from 1 to 18 cm in length and wall thickness from 1 to 6 mm. In this case, the cross-sectional area can vary from 0.343 cm2 to 90 cm2. Weight can be from 269 grams per 1 meter and up to 70 kg per 1 meter.
If a structure with an oval cross section is made, then in the manufacture of such products it is allowed to use larger and smaller sizes. As for large sizes, their diameter can be from 6 mm to 9 cm, and the smaller diameter can be from 3 mm to 50 mm.The thickness of the walls can be from 0.5 to 2.5 mm. Also with this production, an outer diameter from 5 mm to 11 cm is allowed. If the pipe was manufactured according to these parameters, then the weight of one meter of the product can reach 4 kg.
The GOST specifies the dimensions and other parameters of pipes that are most in demand among consumers. In the manufacture of such pipes for a single customer with a large number of products, a separate provision in GOST can be discussed.
Load calculation
When choosing profile pipes, the buyer should know how important it is to calculate the parameters and loads for the supporting structures. But not every person knows how to properly conduct such calculations and purchase a pipe of such a cross section so that the loads are suitable for the future construction. If a railings, fences or greenhouses are constructed from pipes, then it is possible to do without calculation, but if a canopy, a roof, a visor, etc., will be constructed from these pipes, then it is necessary to carry out accurate calculations.
Any material has the properties to withstand certain loads. In this case, no exception and the steel from which the pipes are manufactured with a profile section.If the structure will be affected by a proper load, then it will be able to withstand it, but, unfortunately, it will bend. But after removing the weight from the structure, it will be restored to its original position. And if you exceed the permissible load, then it will bend and after you remove the weight, it will remain in a bent position.
When performing load calculations, it is necessary to take into account the following parameters:
- pipe dimensions and section type;
- construction stress parameters;
- the quality of the source code from which the pipe will be made;
- types of possible loads that the pipe construction must withstand.
Installation
Profile pipes are created according to the standards established by GOST. It gives the opportunity to use the material as the basis of supporting structures. In order for the structure to be built in a short time, the specialists developed special fasteners. It can be either clamps, or different plates and clips. In modern construction, crab attachments are most often used. They can combine several materials. They may be X-, G- and T-shaped. Produce such fasteners from galvanized steel.The main advantage of such a fastening system consists of two components, which make it possible to completely wrap around the products and securely fix them.
Also use a system of clamps and fittings with which to connect the pipe. Connectors are cross-shaped, triple and angular shapes. Cross and tee can connect several pipes, and with the help of a corner you can bend the structure.
If there are several types of fasteners, you can not use welding, which is very convenient when designing a small-sized construction, for example, tents and similar small items.
Tips
To make the pipes, which are considered in this article, use special rollers. They can have great power, with the help of which the pipes under the established section are deformed. If you yourself wish to make a pipe of this type, which will not bear a large load, for example, for the manufacture of furniture or greenhouses, then it is enough to purchase a small machine that can make a metal profile. And if it is necessary to produce shaped tubes that will withstand certain loads,that is, they will be used to design load-bearing structures, then it is already necessary to buy ready-made elements that are manufactured using a special technology and under factory conditions.
Manufacturing in the factory takes place according to the following steps:
- The plant receives large coils of rolled iron, which are cut into strips corresponding to the section of the pipe being manufactured;
- then, using a welding machine, all the strips are connected into one long strip, which is wound on a drum;
- then put this tape in the machine, which forms the strip in a pipe with a circular cross section;
- after that, the blanks are welded into one whole round pipe;
- then the welded elements are cooled and processed;
- after processing, the pipes are placed in a machine that already forms a round part with a cross section installed, that is, a pipe with a square, rectangular or oval cross section.
Experts recommend using 4 rollers in making a square-shaped pipe, and a machine with 2 rollers in making an oval-section pipe.
Also, after the manufacture of pipes, they must be tested for compliance with the standards of GOST.
To do this, use these control methods:
- Flaw detection vortex method, which reveals magnetic and electrical reliability.
- A visual inspection reveals the possible presence of defects, grooves, irregularities and similar criteria that the previous stage of the inspection cannot reveal.
Upon completion of the test, the structure is heated and cooled. Thus, the product undergoes heat treatment. If self-fabrication is carried out, it is best to treat it with high temperature using a blowtorch. But it is better not to make such a pipe independently, since it requires the presence of 4 rolls, as well as a specialized machine that performs work with a high noise level, which is unacceptable for living conditions.
If a pipe with a square cross section is produced, the product must fully comply with GOST 8639-82 standards. If it is with a rectangular section, then the standards of GOST 8645-68 must be observed, and if the pipe is with an oval section, then it must comply with GOST 8642-68. But after production, it must be tested, since it is in this way that you can be confident in the quality of the product.
In state standards the presence of such defects is allowed:
- on top of the finished material may be small nicks, dents, dross and traces of scrap cleaning;
- According to the standards, a small mechanical damage, a thin layer of scale, residues of metal stains and traces after the elimination of defects are allowed at the weld.
After production and inspection, the ends are adjusted to one size, trimming is carried out strictly at an angle of 90 degrees.
In the event that such parts will be used as a material for moving liquids under pressure, then it is necessary to take elements that are able to withstand possible pressure drops. Such a criterion can be calculated by a specially created formula. In order to calculate the pressure effect index with the presence of a rectangular or square section, it is necessary to use formulas that are designed for a specific section shape.
Also watch the video on how to produce shaped tubes.