Pipe welding: technology and types of connections
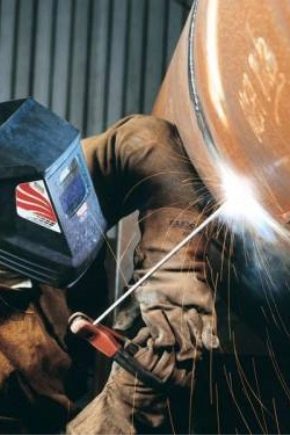
Today, in industrial organizations and in domestic life one cannot do without the installation of pipelines. Their elements are connected in different ways, taking into account the material and the size of the diameter of the pipes, but welding is particularly popular. This method allows you to fix parts in any position and is considered the easiest and cheapest, providing a tight and high-quality docking.
Special features
Welding is a universal view of the connection parts of the pipeline, made of metal, plastic, concrete and ceramics. Since the pipeline is the engineering communications used for the transportation of oil, gas, water and other substances, it is important to connect its parts correctly and securely.Welding works well with these tasks, so it is often chosen during the installation of boreholes, sewage, industrial and process lines, where large-diameter stainless steel pipes, flanges or titanium alloys are used.
This technology is also suitable for joining plastic, chrome-plated pipes of various diameters. All elements of pipelines, both small and large, are fixed according to the established standards, which correspond to the regulations of the State Standards.
Depending on the features of the installation and the root of the seam, a certain temperature and type of welding is selected. Butt thermal technology is based on heating the edges of pipes, thermomechanical is characterized by boiling parts by heating welded wire. The mechanical view is used in industry for fastening horizontal pipes by friction. As for cold welding, it is carried out by treating the parts with a chemical composition that guarantees a durable and reliable seam.
The main feature of welding is that for its implementation they use centralizers, which are devices that simplify the centering of pipe ends. Thanks to centralizers, work is fast, and the seams are of high quality.
The advantages of welding include the following points:
- metal saving and cost of work;
- excellent alternative to casting and forging;
- the ability to connect pipes of various sizes;
- high quality and sealing; ease of implementation.
As for the disadvantages, then during the deformation of the metal is possible.
Tools and equipment
Welding is the most affordable and common type of pipe connection. Docking parts requires not only a certain experience, but also a special device that has switching modes. Such a machine can be started with both electricity and gas, and can also include a socket welding device in its design. For household fusion of pipes, many craftsmen also prefer to have a machine equipped with an inverter. To the rate of consumption of material and energy regulated, the devices are equipped with control circuits.
Depending on the complexity of the work and the diameter of the pipe suitable equipment is selected.
Electrodes
In many cases, electrodes are used for welding. If you want to dock large diameter pipes, then choose electrodes covered with cellulose film.For the formation of corner seams most often prefer products with a rutile coating. In the case when complex cooking is planned, then combined (cellulose-rutile) electrodes are used. The most common are electrodes coated with UONI 13/55, they are designed for welding of low-alloy and carbon steel pipes. Due to the unique composition of these products provide plastic seams, resistant to all kinds of loads.
The only disadvantage of such electrodes is that they require preliminary preparation of edges. Untreated edges in contact with water, oil or rust can cause the formation of welding pores.
Welders
Before you start welding, you need to worry about the availability of appropriate equipment. The most common apparatus are transformers, they have a simple design that allows you to convert the voltage in the mains. The principle of operation of transformers is based on the change in the intermediate current between windings. Welding transformers are characterized by high efficiency, which reaches 90%.
A more advanced type of welding equipment is a rectifier. It consists of a diode unit, adjustment, protection and start-up elements. Unlike transformers during cooking, rectifiers allow joining parts not only from black, but also from non-ferrous metal, cast iron and stainless steel. Rectifiers are inexpensive and provide good quality seams.
Semi-automatic devices whose design is represented by a rectifier, a transformer, a special drive, a sleeve with a burner and a gas cylinder are also in great demand among welders. In the case when welding is carried out without gas, flux wire is additionally used. Usually for joining metal pipes, the apparatus is started on carbon dioxide. The advantage of this equipment is high-quality seam, and the disadvantage is the high consumption of material.
Inverters have also proven themselves well. Such equipment is also called pulse. It is expensive, but has a low weight and high efficiency. Also for welding work using spot machines. They are economical, durable, reliable and allow you to get seams with high-quality sealing.The equipment heats the connecting elements instantly due to current pulses, which are 0.01 s. Therefore, it is ideal when you need to perform a large volume welding in a minimum amount of time.
Types of stitches
Regardless of what pipelines are boiled for their intended purpose, they have welds that are formed by alternating electrical current according to the previously selected technology. To date, there are seams at an angle, butt and overlap. All of them have their own individual technique and features.
Butt joints are the most common, since they tend to lack the deformation of the metal. In addition, they are minimally subjected to internal stress and are characterized by high strength in relation to dynamic and static loads. Butt joints are divided into single, used for pipes with a cross section of up to 500 mm and double, intended for pipes whose cross-section exceeds 600 mm.
Corner joints are considered a butt feed. They are selected when it is necessary to fix the parts at an angle. Such seams are obtained in two ways: without a bevel and with bevel edges.Corner joints are not as strong as butt joints, but still have good quality. Overlapped seams are great for docking plastic pipes. They are rarely used when boiling metal elements. This is explained by the fact that the connection is not very reliable.
When welding pipes with thick walls also use a longitudinal seam. It is formed from several layers, and the work is performed, as a rule, simultaneously by two specialists.
Ways
Welding is a physico-chemical method of joining individual elements, which in the process form a solid pipeline. Such installation is carried out using high-pressure plastic deformation or fusion. Welding seams that are formed during cooking may be different, as they depend on the choice of technology.
To date, there are the following types of welding:
- electric welding;
- cold
- gas;
- argon;
- diffuse.
The primacy among the methods of cooking pipes is electric welding, it is characterized by low price and ease of operation. This is the so-called contact method. To make a connection in this way, a transformer or inverter is required.The equipment supplies a charge to the electrode, which, in contact with the surface of the pipes, heats the metal strongly, which is then cooled using special mixtures or water.
The main advantages of electric welding are versatility and versatility. It is often also performed without electrodes. If the latter are used, they are chosen, taking into account the wall thickness and cross-section of pipes.
Cold welding is strictly regulated by established standards and documentation. This is one of the best options for getting sealed sealed joints. This technique allows you to completely eliminate the heating of the welded elements, and the seams are formed due to the processes of deformation and pressure exerted on the part. Depending on the technique, cold welding is divided into butt, seam and spot welding. The main advantage of this method is that all work takes place without the cost of electricity. In addition, the technique is absolutely eco-friendly and opens up opportunities for creating compounds in large areas.
Often, different types of pipes are connected using an automatic gas burner.This is a rather old but well-proven method with blowing, which heats the metal to high temperatures. Gas welding is well suited, if it is necessary to carry out the installation without butt-separation, as well as for obtaining pivot welds.
It has the following characteristics:
- high efficiency;
- simplicity of work;
- getting a quality and neat seam.
Argon welding is necessary when it is necessary to weld materials that are difficult to connect — for example, aluminum, copper, or titanium.
All of the above pipe welding techniques are suitable for the joining of metallic material, while plastic parts are welded using diffuse welding. Its implementation requires a minimum set of tools, work is fast and inexpensive. To obtain hermetic seams, preparation takes place, then plastic pipes against the lumen are heated with a special apparatus equipped with different nozzles. Each nozzle is selected for a specific pipe diameter. Orbital welding is also considered to be an effective method when, thanks to special techniques and technologies, pipe parts are placed on a special device and mechanically turned 360 degrees.The result is a smooth seam without gaps.
Causes of defects and marriage
An indicator of high-quality pipe melting is considered to be no defects on the welds. This is especially true of thin-walled and plumbing products placed in hard-to-reach places. If welding is done by hand, it is important to pay great attention to its quality, otherwise any mistake can lead to a decrease in strength or destruction of the entire structure.
Defects of welded joints are divided into the following types:
- solid inclusions;
- distortion of the external forms of the seam;
- cracks;
- craters, fistulas, cavities.
Cracks are usually caused by a local fracture near the suture. They are placed in the base of the metal or in the area of temperature exposure. The reason for the appearance of such a marriage is the high voltage that appears in the joints during cooking. Most often, defective cracks are observed when boiling pipes made of alloyed and high carbon steel, which after heating cools too quickly.
Cavities, on the other hand, are formations of arbitrary shape that have no corners. During welding, they linger in the heated metal.Their varieties are fistulas and craters. Such flaws appear when there is contamination, paint or rust in the area of the welding surface.
Rejects can also occur when using dry raw electrodes. Pores are often seen with the wrong choice of welding wire.
As for solid inclusions, these are foreign elements of different origin, which after welding remain in the weld metal. They are oxide, flux and slag. Inclusions are characterized by a different shape and are most often located on the border of the directional and base metal. These defects are obtained as a result of high cooking speed, in the presence of dirt on the surface of the pipes or shedding of the coating material of the electrodes.
Sometimes there are the so-called "lack of penetration", this is when there is no connection between the metal and the seam. Such defects are usually observed in the root of the seam, on its side surface or between the rollers. To avoid this type of marriage, you should carefully clean the edges and control the speed of the device. In addition to "poor penetration", a common problem is a violation of the seam shape, which has the appearance of undercuts.This problem is caused by high voltage and speed of cooking, resulting in a “humpback” joint.
If the slope of the electrode is chosen incorrectly, and a large arc length is used, this may cause an "influx". The seam in this case does not have fusion, since the metal is improperly distributed under the action of gravity and leaks onto the horizontal shelf, forming incrustations.
Other types of defects in welding include: spatter and metal thinning, random arc and external teasers. Random arc is most often manifested when a short circuit of the electrodes occurs in contact with the base metal. Splashes are considered defects that have the form of solid droplets that occur when the welding current is claimed. Bullies are uneven surfaces at the joints that do not correspond to the established dimensions and width of the seam. They are caused by the slippage of the welding wire, as well as the flow of liquid metal into the gaps.
ATAll defects listed above must be eliminated. To do this, they are detected using ultrasound or radiographic monitoring and carry out a number of activities.
On how to solder polypropylene pipes yourself, see the following video.